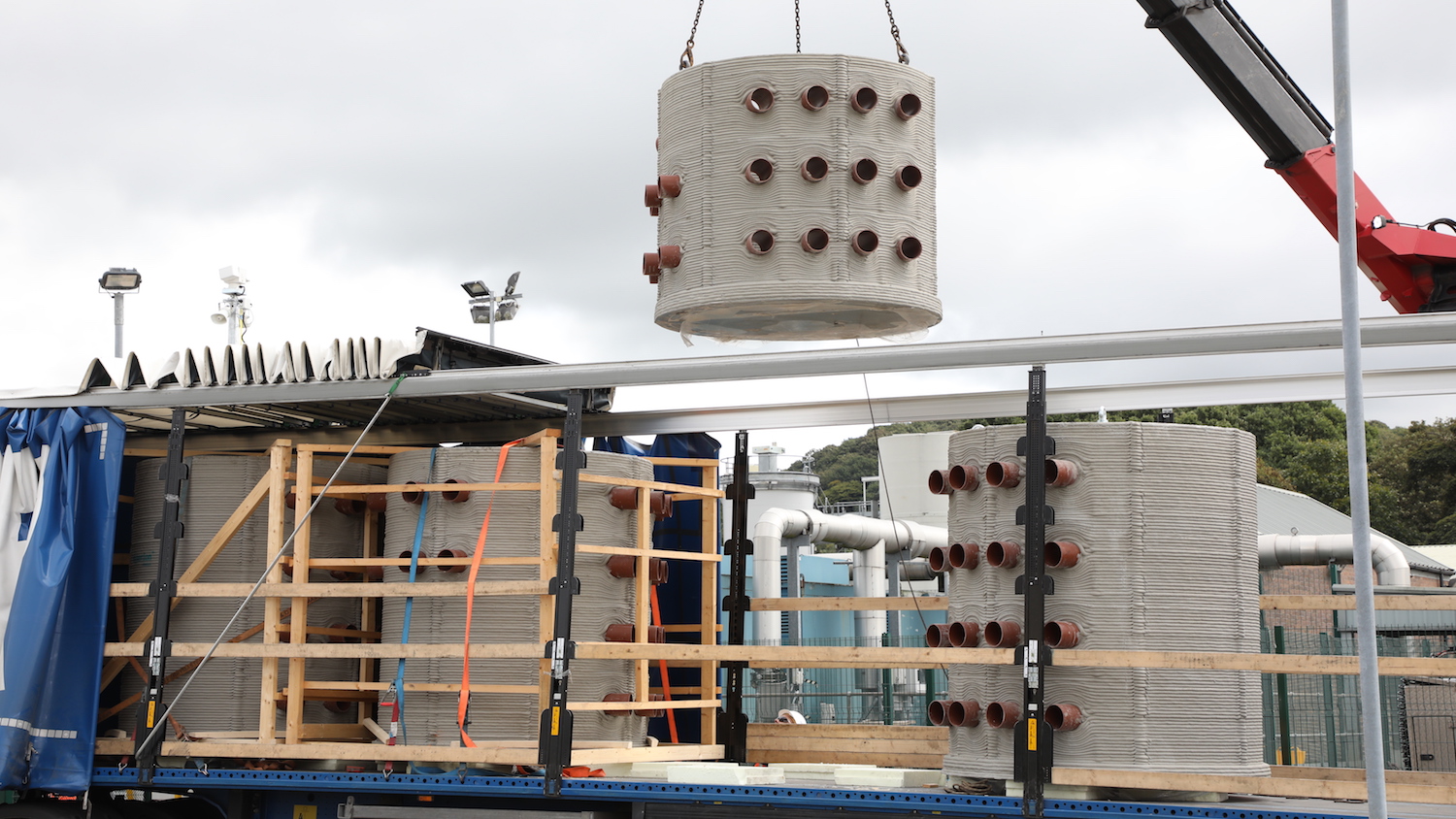
The team of Mott MacDonald Bentley (MMB), Tarmac and Finnish technology firm Hyperion Robotics have combined to reduce carbon on a Yorkshire Water project by using 3D printing.
3D-printed concrete has replaced standard applications for a major upgrade of Yorkshire Water’s largest sewage treatment works – Esholt Waste Water Treatment Works – in Esholt, near Leeds.
Following Yorkshire Water’s inaugural net-zero partner event in January 2023, lead contractor MMB joined up with Hyperion and Tarmac to explore sustainable construction solutions and techniques.
As a result, four bespoke drawpits – traditionally heavy, box-shaped structures placed underground for the containment of electrical cabling – have been designed, 3D printed, and put in place at Esholt.
The drawpits, which meet Eurocode standards for structural engineering, have been positioned to allow for cabling to be installed from a new motor control centre leading to a set of newly-refurbished deep bed sand filters and the site’s backwash pumping station. Together, the equipment combines to control and ensure high-quality water filtration on site.
The 3D-printed design has resulted in a 40% reduction in embodied carbon when compared with a conventional, in-situ drawpit.
Robert Gossling, head of commercial engineering solutions at Tarmac, said: “Together with MMB and Hyperion Robotics, we’ve unlocked new opportunities to embrace exciting new 3D-printing technology and remote construction techniques for Yorkshire Water.
“Combining structurally designed 3D-concrete printing with dry silo mortar factory production methods and the latest low-carbon cement technology offers multiple benefits. By continuing to provide expertise to Hyperion, we’re excited to explore how the key learnings from the project and how 3D printing could be extended across the wider construction industry.”
Thinking out of the box
Henry Unterreiner, Hyperion co-founder and head of engineering, explained: “By thinking out of the box (literally), and proposing a more structurally efficient circular structure, we managed to use 50% less material when compared with a conventional drawpit structure.
“In addition, the technique incorporates less concrete and steel rebar than traditional methods, due to the construction technique enabled by 3D printing.
“Drawpits are only a small part of the catalogue of cost-competitive and low-carbon structures we have developed. Our on-demand manufacturing approach supports the construction industry in its transition to net zero.”
Marc Lupton, capital delivery programme manager for Yorkshire Water, said: “This pioneering piece of technology allows us to reduce our carbon footprint and has the opportunity to replace our traditional methods of construction.
“It’s exciting to see this 3D concrete printed structure. We are looking forward to seeing how we can develop further applications for expanding its use across our capital programme.”
Don’t miss out on BIM and digital construction news: sign up to receive the BIMplus newsletter.