Willmott Dixon Interiors’ transformation of a former factory in Islington into the London Screen Academy (LSA) film school, completed earlier this year, showcases best practice in the use of BIM on a fit-out project.
The contractor completed the 54-week project for LcatED working in conjunction with the Department for Education. It involved the partial demolition of the central and southern section of the existing four storeys plus basement building, to be replaced by a three-storey plus basement building with an open terrace on the third floor to be used as an amenity space.
One of the customer requirements on this project was to implement a BIM Level 2 process to support the construction plus operation and maintenance stages.
Willmott Dixon Interiors head of digital construction Amador Caballero takes up the story: “At the tender stage, the LSA was completed up to RIBA Stage 3. It was our responsibility to engage the design team to complete the design and deliver the project according to the customer’s expectations.
“As a contractual requirement, we were requested to comply with the BIM Level 2 process, and the Employers Information Requirements (EIR) template was provided to us. However, no BIM Execution Plan (BEP) was produced at this stage, although we had 3D models from the architectural and M&E design.
“Our approach was to support the customer to develop and ensure that the content of the EIR template was suitable for the project requirements. As no asset data deliverables were identified in the EIR, our technical services manager collaborated with the customer to define the most appropriate data for collection during construction.
“Once we agreed on the modification and clarification in the EIR with the customer, we developed the appropriate BEP to establish the correct manner to develop the model and data format.”
We established information workflows with the correct security access and approval process to ensure the appropriate management and information exchange between the different stakeholders involved in the project– Amador Caballero, Willmott Dixon Interiors
The use of VR proved to be “a very effective and valuable way to engage our customers, our team, our designers and our subcontractors with the overall design,” according to Caballero.
He adds: “Architecture Initiative prepared high-quality videos that allowed our customers and colleagues to explore the 3D model. Created with immersive 360° panoramas and viewed using VR headsets, the model made the experience of presenting the project much more interactive and clearer to everyone involved.”
Design validation
As the design was based on existing information, the contractor undertook a point cloud survey to verify and identify any discrepancies between the RIBA Stage 3 design and captured 3D data of the existing building. “This approach ensured and supported the correct development of the RIBA Stage 4. We completed the point cloud survey while the demolition works were in progress and captured all the structural elements and ensure the accuracy of the developed design,” says Caballero.
“Our approach also included the use of the BIM models to produce more accurate and faster quantities during the tender and construction stage with the use of 5D quantities take-offs software. By interacting with the model in this way, we verified that the different information provided by the consultants and subcontractors matched with the content in the model.”
Information management
Supporting the design team and subcontractors is essential for a successful BIM implementation on any project, Caballero says. Therefore, a number of workshops were staged to ensure that the development of the design and the exchange of the information went according to the agreed BEP.
“We established information workflows with the correct security access and approval process to ensure the appropriate management and information exchange between the different stakeholders involved in the project,” he says.
“To support the design coordination and management of clashes, we used BIM Track, a web-based collaboration platform. It allowed our team to better collect and record all actions, conversations and decisions regarding each individual clash in a single place, reducing the inefficient use of email. This approach enabled a smoother and clearer flow of communication. It maximised the quality of our information exchange and our overall execution of the project.”
With BIM Track, the project design could be reviewed at any time and anywhere, either from a desktop or mobile device. Having a clear dashboard, with identified issues, resolutions, and outstanding actions, provided a clear overview of the current status of the design, Caballero notes. “While clash detection was carried out by the lead designer, our project team undertook a collaborative approach and performed additional revisions to identify any further design challenge,” he says.
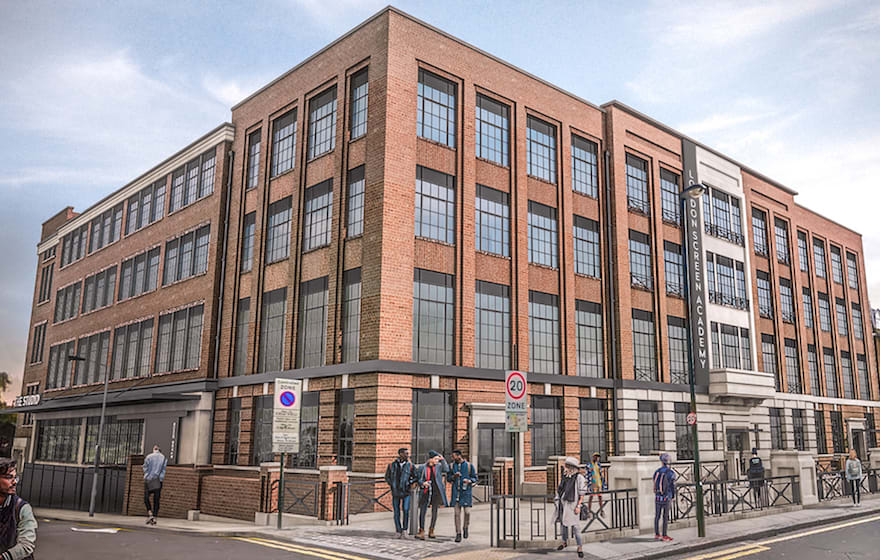
A CGI of the London Screen Academy
Taking the models on site
Making the models accessible to all users is a key step to achieving the correct level of engagement and collaboration for all stakeholders with BIM, Caballero states. “Therefore, we introduced and implemented the use of Dalux Field [see image, right] on this project. This software allowed the whole project team to have access to the latest model, drawings and data available from their mobile devices.
“This also supported our sustainability approach of reducing the number of paper drawings on site. These tools further enabled access to the latest information through the common data environment.”
Screenshot from Dalux Field
Augmented reality
Additionally, AR tools helped the site team to verify the works completed on-site, helping to avoid future clashes or design challenges. Caballero explains: “In other words, this technology provided a more accurate view of what would be built and gave our team a better understanding of the project, ultimately facilitating its execution.
“One of the driving factors for the use of tools like Dalux and BIM Track was the use of industry foundation classes as an open standard approach to delivering information to the different stakeholders. Some of our supply chain partners use different authoring tools. Therefore, the use of this technology drove easy collaboration among the team members. It also ensured data models were developed before construction, ensuring better planning, design and clash detection process.”
One of the contractor’s supply chain members supports this assertion; Jarek Wityk, design manager at Winters Electrical Services, says: “We have used a few different workflows to deal with clash detection and management: the use of BIM Track and Dalux Field on the LSA project supersedes all workflows we have come across to date.
“I really like the integration between different platforms and the ease of collaboration between all project members.”
Asset information model
The collaboration with the customer at the tender stage ensured that the contractor had the asset data deliverables clearly defined. As a result, Willmott Dixon Interiors was able to include this as part of the supply chain appointments and engage with the consultants and subcontractors to provide the correct information in a COBie format.
“From our appointment, the production of COBie data was carried out during the different stages of the project. The aim was to gradually collect all the data that had been agreed with the customer at the beginning of the project, so we could guarantee the availability, integrity and correct transfer of information during the operational phase.
“One of the key successes on the project was the use of open standards, collaborating and sharing knowledge with all the stakeholders involved in the project to achieve the desired data outcome to support the FM team during operations and maintenance of the assets.”
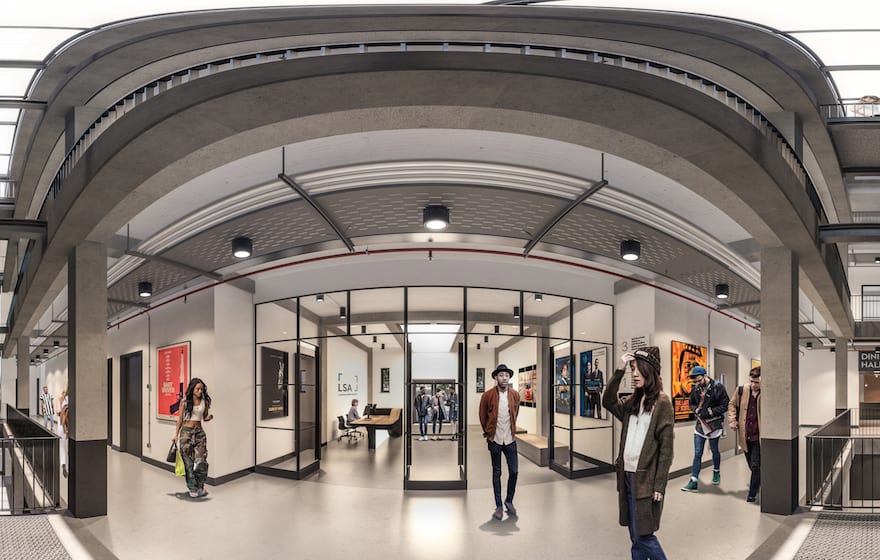
Architecture Initiative’s high quality 360° panoramas proved useful for supply chain and client alike
Results encourage further BIM use
Caballero says: “The benefits and perceptions of BIM are very difficult to convey [in fit-out] projects and remain one of the key challenges to overcome throughout the industry. However, the benefits produced during the different stages of the project, [specifically in] information management, logistics, costing, coordination and overcoming issues, are beginning to convert opinions.
“A key goal in our business is up-skilling our people’s knowledge and giving our teams ownership and responsibilities to deliver BIM projects. A large amount of training is provided to our team members to ensure that they can deliver the BIM process and use the appropriate digital tools as business as usual, without the need of BIM or digital managers resources.”
Peter Nicolaides, senior technical services manager at Willmott Dixon Interiors, supports Caballero’s assertion: “I have used both BIM Track and Dalux Field on the LSA and found both to be extremely useful. The latter gives a very user-friendly and mobile opportunity to view the project in 3D.
“BIM Track is an excellent management tool that provides easy-to-view reports on the current status of clash detection. Each clash is given a unique reference, which is kept on file with the latest status and who it is assigned to. The assigned accountability encourages all parties to search out and deal with all clashes.”
Caballero concludes: “The LSA project has been an example in our business of how our people can take ownership and pride to deliver the BIM requirements according to the agreed standard using digital tools with minimum support and supervision.”
Comments
Comments are closed.
I agree the BEP did help to manage the expectations and provided clear guidance, the use of BIMTrack really helped with coordination and the Dalux’s Augmented Reality (AR) was especially useful for our teams on site. What stands out on this project was the successful cross-team collaboration.
I am not saying everything went smoothly, we had many issues, but I dear say much less that we typically have on a similar project.
The LSA project is one of the best-run projects I was involved in during the last nine years.
Its an excellent example that BIM can work and be beneficial not only for the client or Tier 1 but also for Tier 2 and below sub-contractors, resulting with systems installed once and in the correct sequence!
Id say the excellent results are not down to the use of technology alone, but a combination of new processes, technology and most of all the right people with sufficient knowledge and drive.
I am sure more people were critical to the success of this project. However, without the leadership of the Peter Nicolaides (WDI TSM) and Architects Rowan Parnell, Daniel Donnelly and Rob Dutton the whole process would not be as smooth.
From our team special thanks for Ray Minns for his exceptional social skills, technical knowledge and drive, plus everyone else who was involved in this project at WES, we truly worked together on this one across each department Construction-QS-Design-Admin.