- Client: Waitrose
- Lead Contractor: Simons Group
- BIM Tools: Navisworks, 4Projects, Autodesk, Solibri
Simons Group spent three years bringing a Waitrose store to the Wiltshire town of Malmesbury. Only 27 weeks was spent on site, however: the rest of the time was taken up with consultations with client, planners and residents to agree a design for a sensitive site. The result was a complex curved steel shell surrounded by habitats for owls and swifts, and partly masked by berms and gabion cages.
The project is also a good illustration of where the industry now sits with BIM, according to Darren Wallace, Simons’ design director. Waitrose and Simons took BIM beyond the construction of the shell and into the retail fit-out, creating a data-rich model using multiple software platforms and a high degree of input from designers, suppliers and manufacturers.
The result has provided a baseline for Simons and Waitrose to judge the success of future projects. Wallace says: “We’re really proud of the achievements from Malmesbury and I’d like to think the future of BIM is shaping up to the point where, at some stage, a live model will tell the end user when a building element or product needs maintaining – much like the modern car tells now tells us when it needs to be serviced.”
He adds: “This has been a real exemplar for both Simons and Waitrose in working together to push BIM on a retail project. It’s relied on ‘buy in’ from everyone involved to ensure people are prepared to work with us. It’s not often you sit in meetings with the developer’s architects and design team, the client’s architects and design team, the client stakeholders and end users, all wanting to be part of the solution.”
The project was unusual in that it involved four architectural practices: Simons Design handled the shell; Farrell & Clark and Bamber & Reddan both worked on the retail fit-out; and a fourth firm, WCEC Group, was employed by Simons Construction to act as a neutral “BIM manager”.
Wallace says: “The BIM management role was fundamental to the success of this project. They act like the design manager on a traditional contract. They set out the client’s requirements and manage the expectations as to how everyone is going to operate, and they also ensure that basic points, such as working to the same point of geometry, are always monitored.”
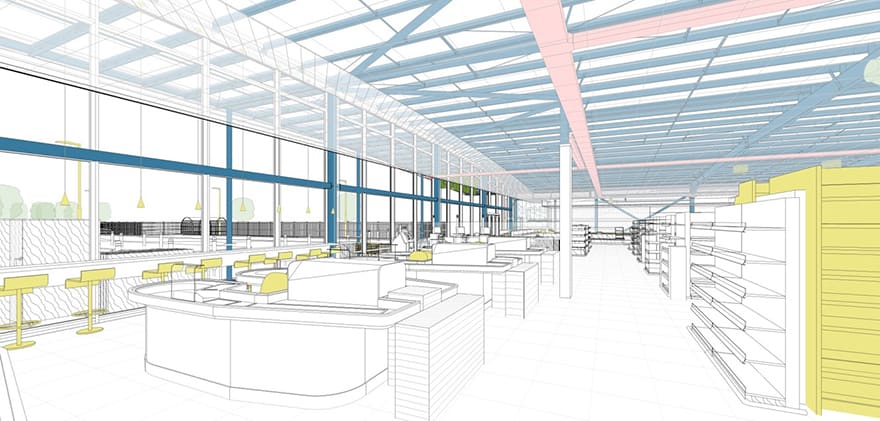
Simons was also awarded the fit-out contract, which allowed the team to maintain BIM momentum
Simons Group was the developer, shell architect and main contractor, so Wallace could follow the BIM workflow through the project team and its suppliers. On the shell, for example, this meant getting the steel fabricators, cladding manufacturers and glaziers on board, with a total of 16 disciplines adding data to the collaborative model.
The large number of subcontractors and subconsultants involved in any construction project creates challenges in implementing BIM. “If you talk to a structural engineer you’ll find they’ve been using this type of software for 10 years, but when you get to the point of combining architects, M&E and structural disciplines together, then add a contractor, a cost estimator and a programmer into the mix, BIM does form a fairly exciting and unique platform,” says Wallace.
As far as BIM is concerned, the firms formed a mixed ability group. As Wallace says, “There are a growing number who have been working this way for a couple of years, but then others say ‘sorry – what’s BIM?’”
Simons’ response was to bring elements of the design that were beyond a given supplier’s capabilities back in-house, or to provide direction in improving that firm’s skills. “In the longer term we need to work closer with our preferred suppliers to bring everyone up to speed with BIM,” he says.
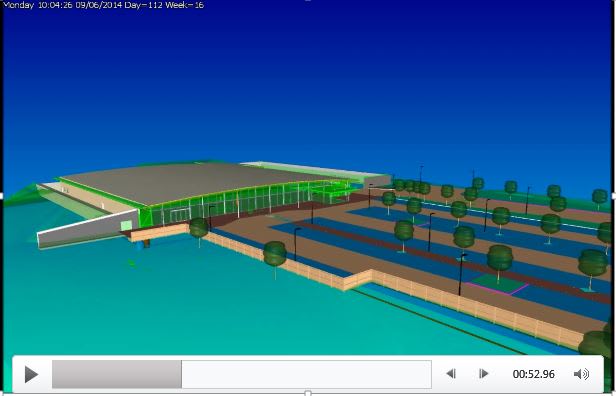
A significant issue was getting five BIM software tools across 16 disciplines to contribute to a common BIM environment
Just as the demand for BIM within the industry is growing, so is the demand for IT expertise, and data storage. Wallace says: “Our demands on our IT department and also the hardware and software houses means a constant discussion in ensuring we can meet the customer’s needs. Take the size of files for example. The size of BIM libraries, and the individual files within them, is going to increase, therefore the demand on memory, graphics and bandwidth will increase as well.
“A typical example from Malmesbury was cladding and the use of Kingspan’s BIM elements. Kingspan has developed a library of parts that contain all the detail you need in a single sheet, but when applied in multiple across the whole building – the file becomes unmanageable.” Wallace’s team found a work-around by reproducing the cladding element with just the key data, then re-applying it.
To take a contrasting problem, other products do not yet exist in much detail in BIM, such as the gabion cages and landscaping features, which were shown as a simple family and part entity with a specification and supplier information.
Language problems
Perhaps a more significant issue was getting five BIM software tools across 16 disciplines to contribute to a common BIM environment. Navisworks was used by BIM manager WCEC to combine everything together, and check it was working. But Simons found that not all data from each discipline model was retained when transferred into the common model using the industry foundation class (IFC) format.
Wallace says: “The government wants all its projects to be in the IFC format, and we try to align ourselves with that. We run Bentley AECOsim Building Designer, which allows us to view IFCs anyway. But at the moment Revit doesn’t readily view or use IFC, so you need another piece of software, such as Navisworks, to do that. At Malmesbury we had to be sure that if we sent a file to, say, Bamber & Reddan, they were seeing the same thing that we were – so we sent an AutoCAD Revit file, an IFC file and a Navisworks file, and let them look at all three and work out which was the best version for them.
“In our experience, a lot of consultants and suppliers are convincing customers to focus on the use of Revit, whereas what we need is an industry concentrating on getting their chosen software to export into IFC without issue, regardless if it’s Revit, Bentley AECOsim, ArchiCAD, StruCad, Tekla or any other.”
Simons uses 4Projects as its document management system for live projects, to which it has added a plug-in called 4BIM that provides some BIM processes aligned to the government’s standards.
Embracing fit-out and FM
Simons was also awarded the fit-out contract, which allowed the team to maintain BIM momentum, and ownership of the model (alongside Waitrose’s fit-out architect and consultants). It also helped ensure that the single model would achieve Waitrose’s ambition for a data-rich model that could be tested by the end users and FM teams.
As with the shell, where fit-out suppliers didn’t yet have the capabilities to work in BIM, the client’s architect and other design consultants complemented the model with additional elements themselves. Wallace says: “Everything’s achievable, but you need people who are prepared to work closer and more openly.”
Simons has not estimated how BIM affected the outturn cost at Malmesbury, but Wallace says it did “establish is a baseline against which we can measure like-for-like schemes in the future”.
He concludes: “Simons will be committed to ensuring the learning continues with our customers, we’re working into cost profiling and scheduling and then linking it into FM, and realistically, we are not that far away.”
In our experience, a lot of consultants and suppliers are convincing customers to focus on the use of Revit, whereas what we need is an industry concentrating on getting their chosen software to export into IFC without issue.– Darren Wallace, design director, Simons Group
Comments
Comments are closed.
Is this yet another example of systems complexity masking the real issues of getting a team together who will talk, take action and deliver to a common goal? If you haven’t been able to sit in meetings with the developer’s architects and design team, the client’s architects and design team, the client stakeholders and end users, all wanting to be part of the solution then frankly the client has not put the right team together under the right procurement strategy in the first place! Technology, as has been proved before, will not solve the ills of the industry, people will.
As a local resident it is a real pity that with all this technology the Waitrose brand signs cannot apparently be set to turn on and off automatically to ensure compliance with local operating agreements.