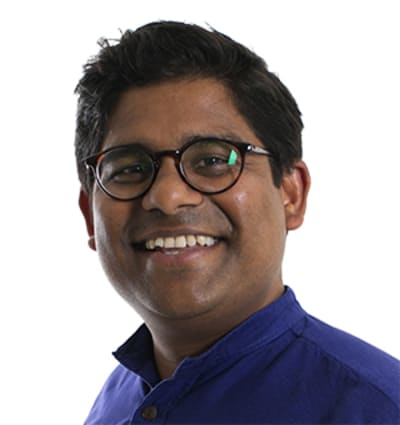
‘Using BIM Level 2 protocols, combined with the expertise of the design team and supply chain, allows a robust digital record to be created for all operations and changes to the project.’ Andrew de Silva
Andrew de Silva, director and architect at David Miller Architects, discusses how BIM can be used in practice to deliver information continuity.
Much has been written about construction’s “golden thread” since Dame Judith Hackitt’s report on the findings of the Grenfell Tower disaster, and what we’re hearing resonates in what seems to be an increasingly fragmented building process.
The report clearly highlights the failings which, as an industry, we are continually repeating by not delivering accurate asset information to the standards required for running our buildings effectively and efficiently.
A large part of this is down to a lack of good record keeping throughout the design and build process and I believe this is something that can, and should, be easily rectified.
The necessity for a Common Data Environment is now more essential than ever and, if used correctly, can simplify the project at each stage of the build, so that once a project approaches completion an easily accessible and useful digital operations and maintenance manual is in place. Having this can allow everyone in the supply chain to contribute and ensure that all data is readily accessible post-build.
On a typical construction project, an enormous amount of information is generated. Much of this is often unstructured and poorly coordinated, which is why using digital methods of recording and storing this information can eradicate waste, reduce risk and save on costs.
An effective Common Data Environment hosts all project information, such as models, product details, COBie data sets, FM systems and so on. All of this information exists on any project – it is how we manage it which is important.
We are seeing an increased level of buy-in on digital methods of working throughout the private sector, but some clients are struggling to take advantage of the benefits because it is all about short-term actions to allow long-term wins.
These actions require investment in time, resource and budget, all of which are under increasing pressure, and it is this that appears to be hindering public sector implementation.
To try to overcome this, we recently ran a workshop specifically for public sector clients, together with Devonshires Solicitors, Airey Miller Project Managers, ActivePlan BIM Consultants and Notting Hill Genesis HA, to communicate why we need to be using BIM on housing projects and how this is led by the need to weave that ‘golden thread’ through each project stage.
Using BIM Level 2 protocols, combined with the expertise of the design team and supply chain, allows a robust digital record to be created for all operations and changes to the project.
The workshop attracted more than 150 attendees, which shows there is an interest in how this can be done. In the workshop, we highlighted how, at the very beginning of a project, a detailed set of Employer’s Information Requirements (EIRs) that capture the organisational and asset management team’s goals, are needed. They define the level of BIM to be applied to the project and set out the roles and input required for each member of the design team and supply chain.
However, we often see that clients don’t have, or know how to create, EIRs. Therefore, DMA, in collaboration with Airey Miller, ActivePLan and Devonshires, has been delivering in-house training and support to clients on how to develop their own EIRs as well as helping them to manage the Common Data Environment throughout a project.
In the workshop, we also shared our experience at Parsons North (pictured top), a project that will create 60 new homes for Westminster City Council in London. Here we set up and managed the Common Data Environment and discussed with the client their aims for RIBA Stages 1 to 3 to achieve planning.
We’re continuing to apply the same approach with our contractor-client, Osborne, through workshops to discuss detailed requirements at key milestones – for example at financial close and at handover.
There have already been significant benefits:
- Full transparency between all consultants and client, with the client having full access to structured data that gives the right levels of detail and information. Westminster City Council were very keen at the outset to have visibility and this was the first time they have used a Common Data Environment in this way.
- Everyone has the most up-to-date, fully coordinated information. In this scenario, where we had 13 consultants appointed by us, it enabled them to access the data individually, rather than having to go through us, making the process much more efficient.
- The decision process is tracked so it is easy to see why and when decisions were made and by whom. As the client team evolved, this made it easy to explain and justify the decisions that had been made and so keep on programme.
- This process can be developed, refined and used for future projects as clients digitise their large estate portfolios. We are currently working on six new projects with Westminster, three of them up to planning stage and three of them post planning, using what we have learnt and recorded together along the way.
George Stevenson, managing director at ActivePlan, commented: “We need the ‘golden thread’ to ensure the organisational need for a facility/space is considered through the design and construction process into operations. This should ensure a safe environment and one that is delivering the expected value in years to come, hence retaining the designer’s defined specification through product selection, value engineering, installation, testing and commissioning into operation and replacement.”
This point was reinforced by Lloyd Patman, information manager and BIM coordinator at Airey Miller: “By connecting the design and construction with the operations, the digital as-built records can easily be updated as changes are made during the life of the facility.”
This is fundamental to the ongoing management of any asset and would hopefully help to prevent such disasters as Grenfell from being repeated. By engaging the entire supply chain and with client buy-in, the implementation of the golden thread is not a difficult one. All of this information currently exists – we just need to better manage the collation process for a safer environment.