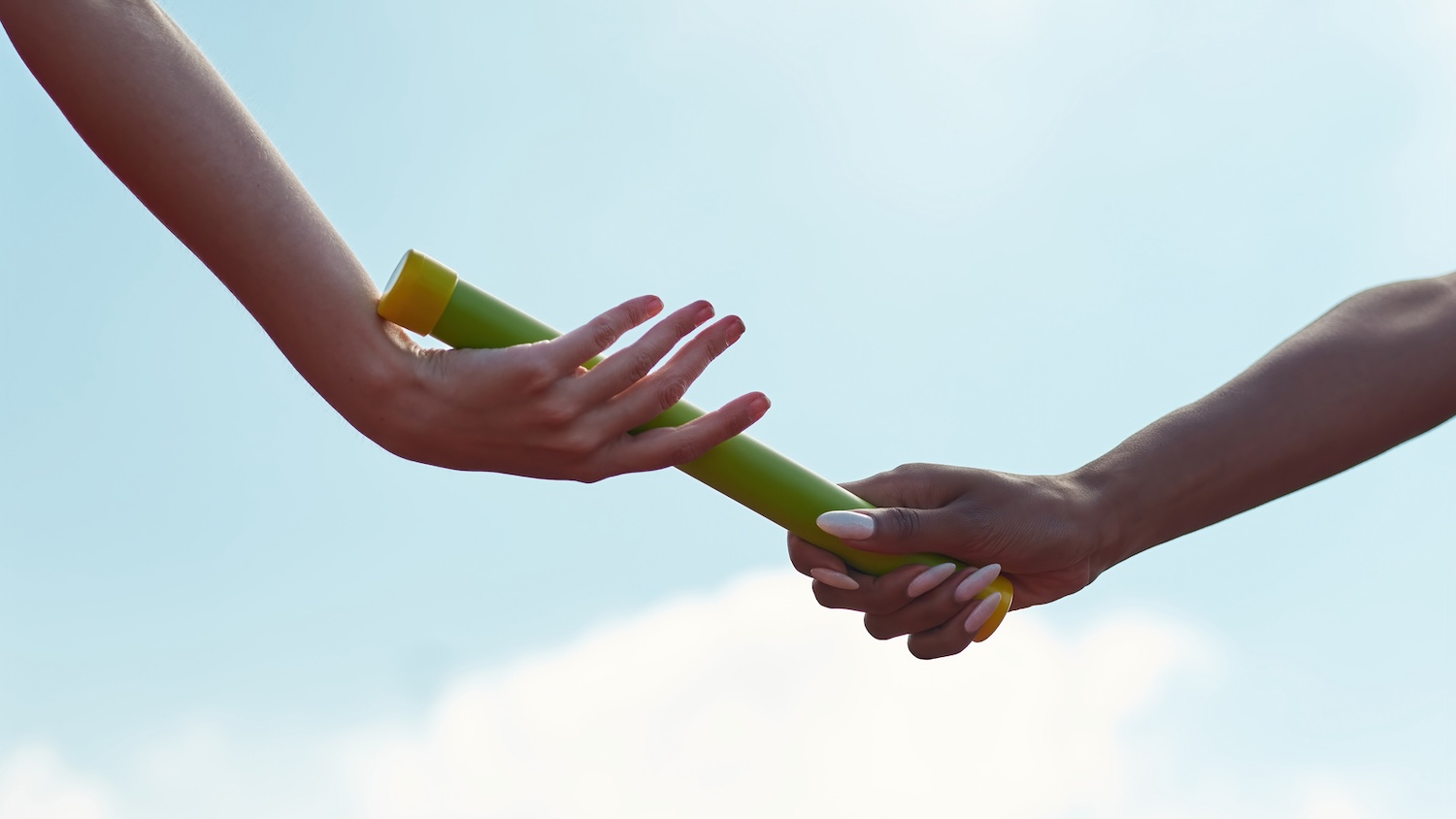
The handover part of information management is broken, Johnny Furlong of Dalux declares. Here he details how it can be fixed.
O&M manuals, H&S files, Regulation 38 and handover packs are essential for the effective management of buildings and to comply with the Building Safety Act.
A recent LinkedIn poll revealed that everyone thought the system was either completely flawed or somewhat flawed. For something so important, why is no one happy with the way this information is collected and handed over?
Paying multiple times for building information
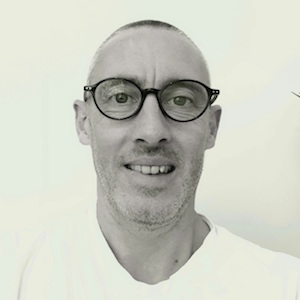
“Using third-party O&M production companies results in paying twice for the same documents and data.”
During the construction phase, detailed information is collected. Contractors pay for this information as part of their contract with subcontractors.
The problem arises when information that is essential for O&M manuals, H&S files, Reg 38, etc… that should already be documented during the construction phase is often gathered anew by third-party O&M production companies.
Using these companies results in paying twice for the same documents and data. This cost is not small either – typically £50,000 for a £100m project. That is 0.05% of construction value wasted.
It gets worse as we often pay for the asset data a third time as FM managers will typically resurvey a new building to get the asset data they require for compliance and planned preventative maintenance (PPM).
Root causes of cost duplication
- Historically we employed O&M production companies because it was a laborious task collating the information in ring binders. In the digital age, we have, for the most part, failed to align our procurement to digital ways of working.
- There is a lack of integrated information systems throughout the construction lifecycle. This is particularly acute for data, which is often shoved around between multiple systems using Excel. This fragmentation necessitates re-collection and re-verification of data, leading to additional costs and delays. Having CDEs and then a completely disconnected handover system makes no sense.
- Lack of standardisation adds yet more cost. This is evidenced in a study by RICS. The study suggests that standardised practices can significantly reduce the effort and cost involved in producing O&M manuals.
- The handover process itself is a critical weakness. Often, there is a disconnect between construction teams and FM teams. This gap necessitates additional effort to compile and verify information post-handover. The Soft Landings framework, developed by BSRIA, aimed to bridge this gap. Unfortunately, the framework rarely seems to be used.
- Digital technologies such as BIM should have significantly addressed these inefficiencies, but haven’t. There are a few reasons for this, one being that BIM and information managers are rarely given the responsibility for production/management of the handover information as this is subcontracted out to O&M production companies. And when BIM and information managers are given the responsibility for production/management of the handover information, they tend to use COBie, which does not work as intended.
Recommendations for improvement
To address these flaws, several steps can be taken:
“The current O&Ms and COBie is not what facilities managers want. It is therefore imperative to understand what information FM teams want and in what format.”
- Subcontracting Ditch subcontracting to produce the handover information. Do it in-house. With a £50,000 saving per project, any technology or additional staffing required will be easily paid for by the savings made and you get better quality.
- Handover information in a useable format The current O&Ms and COBie is not what facilities managers want. It is therefore imperative to understand what information FM teams want and in what format. This is often by product/asset, with asset data and documents (PDFs) linked using product and asset data sheets. These data sheets need to be easy to read and contain the critical information required for maintenance, such as the PPM schedules. With building safety being a priority, you now need to include the building safety inspection schedules.
- A platform approach that has integrated tools for the collection and handover of information will enable project teams to collect information once. An efficient CDE should have a dedicated handover module that makes it easy to collect and handover both the documents and product/asset data.
This can even be taken further whereby the CDE and handover systems also have a CAFM asset management system. A direct link from the CDE to the client’s FM system may not always be realistic due to contractual issues and contractors and clients running different systems. However, contractors should also consider both the commissioning stage of projects and defects liability period. In both these phases, contractors can reduce risk and save money by having a CAFM asset management system.
There are systems out there, such as Dalux, that take a holistic integrated platform approach, with CDE, handover and FM along with 360-degree photos, tendering, clash detection and more all in one integrated platform. To be future-proof, any platform should be a BIM platform. The platform should also be able to link a 3D model’s spatial information from design teams with site and manufacture information in an easy-to-use way.
The Dalux approach is to use product and asset data sheets. These data sheets can be completed easily online by subcontractors and manufacturers without the need for spreadsheets, Revit or complicated BIM workflows. - Company standardisation Establishing company-wide standards for what documentation and data will be handed over, and how and when this information will be collected.
- Soft Landings Using technology better and having a company standard could help re-energise Soft Landings, and get FM involved earlier in the design, construction and handover of buildings. This reduces the amount of time and effort required by FM teams in the handover process and delivers a higher-quality handover.
- Training and awareness Ultimately, we need to change the culture. This can only be done with conversations, education and training.
This is an abridged version of Johnny Furlong’s original article, which can be found on LinkedIn. He is staging a webinar on this topic on 4 September, while Dalux is running an in-person event for building owners on 3 October.
Don’t miss out on BIM and digital construction news: sign up to receive the BIMplus newsletter.
Comments
Comments are closed.
Well done raising the profile of this problem.
As a former Design Manager familiar with the CDE and regulatory compliance issues specific to each project – the best contractor I have worked for kept me assigned through to the end of their projects to manage the commissioning and handover process including all the documentation being prepared in-house – with the help of excellent in-house staff.
Yes – I did liaise with the client’s FM teams but there is massive scope to improve on this.
The BIM agenda is misaligned with the true needs of the client organisations in my opinion, and we are in danger of the golden thread of digital information being ineffective at handover and for the ongoing in-use phase in the project life cycle. Another example where outsourcing should be avoided.
Max Muncaster