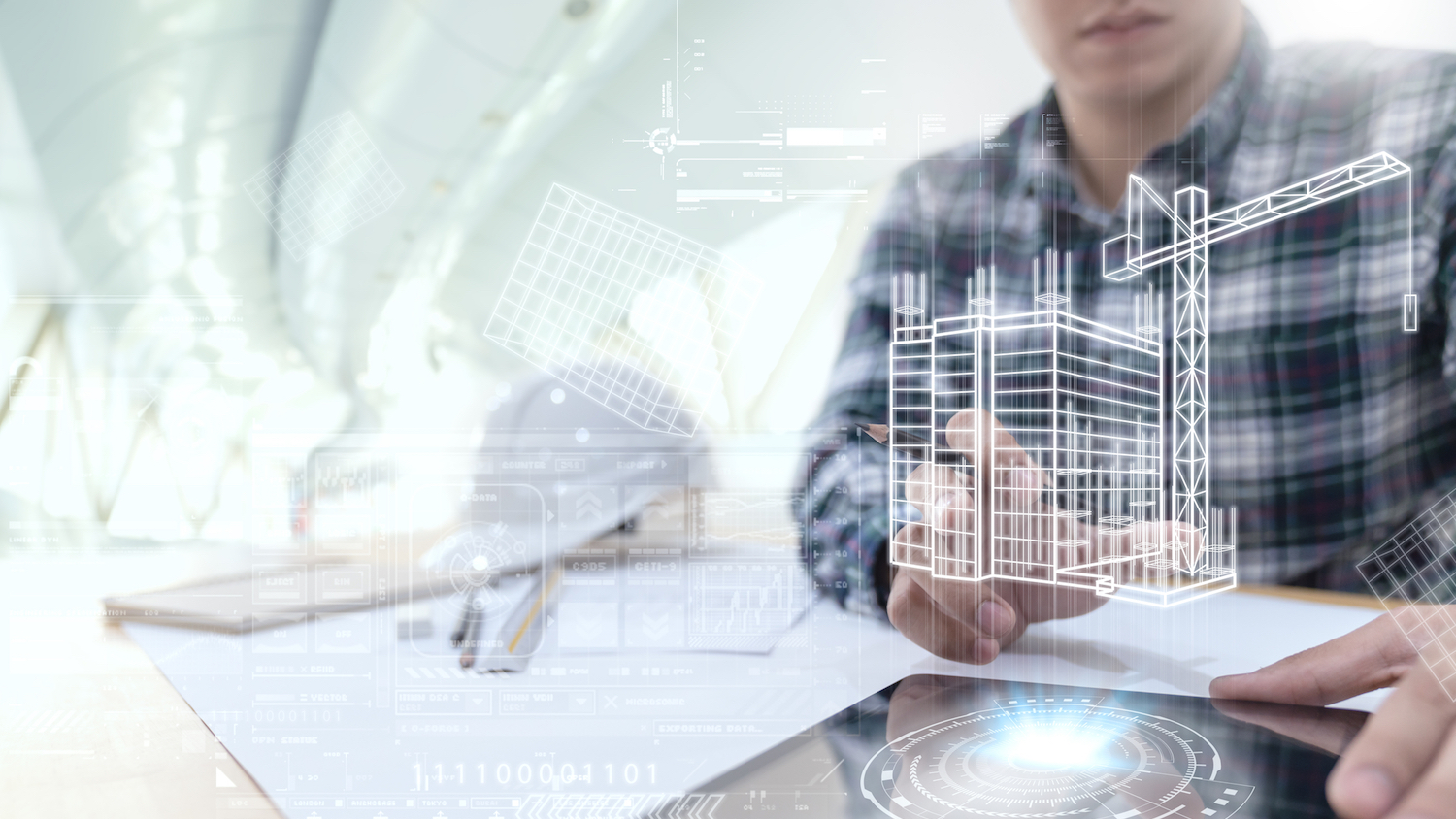
How much further can the design for manufacture and assembly (DfMA) approach go? Joel Hutchines calls for data to drive design for constructability.
As the construction industry continues to adopt the DfMA approach, it is moving beyond its buzzword status. Key thought leaders have recently been advocating this movement, notably Autodesk’s Amy Marks, head of industrialised construction strategy and evangelism, who believes that the approach is really about data and collaboration – getting the right data in the right people’s hands as early as possible. It is, in her words, “data for manufacturing and assembly”.
This approach to data is much greater than industrialised construction or prefab, as it is really about design for constructability, the need for more data throughout the entire pre-construction phase.
Data needs to be available to each stakeholder before, during, and after every decision that is made because otherwise, designers have no chance of reducing rework and decreasing waste, whether it be in time, money, effort, or resources. According to studies from both Swinburne University and The Journal of Engineering, the cost of redesign work could be as high as 21% of the project cost.
Through design for constructability, both project cost and risk can be dramatically reduced while quality and efficiency can be increased. The three principal areas where this can work are design intent, the bid tender process, and change orders.
Design intent
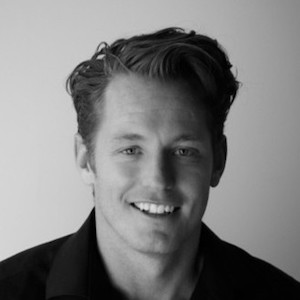
“Through design for constructability, both project cost and risk can be dramatically reduced while quality and efficiency can be increased.”
The very notion and process of designers producing a design within building information modelling, without easily being able to understand whether it is achievable, seems a little ludicrous when you compare it to any of the manufactured items people interact with daily.
Imagine Apple designing a new iPhone without full consideration and development of the manufacturing methodologies and process? Apple CEO Tim Cook would never let that happen, but in the construction industry this is common.
Design intent is produced by the design team with the best intentions of it being easily built, but without them engaging suppliers or contractors early in the project, there are many elements that can’t be accounted for. Are there suppliers available in this area? Is it an appropriate methodology? Does the supplier have a more efficient way of designing it? Will the timing of the project affect any of this?
No matter how you look at this, it is very clear that both the design process and participants need better ways of understanding contextual and multi-criteria data to make the right decisions.
Bid/tender process
The bid/tender and pre-construction process on every project can account for as much as 18% of the overall project cost. This very labour-intensive process requires both the main contractor and subcontractors to invest substantial amounts of time and resources to manage the process. The very notion of shipping design intent to suppliers (in the form of 2D drawings and specifications for them to interpret, take off, and estimate cost) highlights the need for a better transfer of data.
The entire bid/tender process could be dramatically streamlined by simply taking a product approach to construction elements, namely process as a product: automated processes that can both ingest design intent (in the form of both 2D and 3D geometry) and automatically create the relevant information (data, design and cost) to dramatically streamline the entire process. This would provide the right data early in the project lifecycle and eliminate the notion of design intent and the need for a bid process.
Change orders
All this cost, time and rework is far from finished once the contracts have been appointed. Most subcontractors will have feedback and requests for changes based on their knowledge or even material and labour availability or overall cost. These changes require even more effort for approval and rework as this continues throughout the entire construction process – changes required resulting in more time, cost, and effort.
It would be very hard to eliminate changes in projects, but they can be dramatically reduced by providing more data to all stakeholders. If designers knew more about the available methodologies and the impact, then main contractors could easily select from subcontractors based on all available data, without running a tender process and the entire construction process would be streamlined, requiring fewer changes throughout.
“The entire bid/tender process could be dramatically streamlined by simply taking a product approach to construction elements, namely process as a product.”
With access to the right data, changes can become opportunities for positive impact, rather than the current situation where they are far more reactive to unseen problems or knowledge.
Computational design breakthrough
Some people believe a DfMA approach will resolve many of these issues, but the process can still be productised to make DfMA feasible across most projects. When I founded my former company Splash Modular, it was my intention to highlight how computational design could do this. We believed that if we leveraged computational design techniques, we could automate the entire process of design and allow for configuration of an element at the front end and have automated outputs, including shop drawings, bill of materials, machinery files, assembly details and even price calculations.
This led us to developing a customisable digital product (CDP), which enabled us to provide the architect with the limitations and knowledge of how to design the element without the need to engage with us directly. It enabled us to move away from a standard library of preconceived designs and rather than designing from scratch each time, we could focus on developing the process as a product, innovating on manufacturing methodologies and driving efficiencies.
Although this approach achieved our goal of helping DfMA adoption, it was very limited to the relevant manufacturing data available, restricting the designer to what was achievable rather than being intuitive and offering insights into why and how. What is now clear is that computational design needed help from AI and machine learning.
The promise of AI and data delivery
The development of AI and machine learning tools have the potential to move DfMA into the notion of constructability. By bringing forward and using the knowledge and data that usually sits downstream in the project lifecycle, designers in the construction will no longer have to rely on the hard-coded approach of rules-based, automated processes with limited inputs and predefined outputs.
It will allow designers to be far more dynamic: rather than deploying computational design scripts as a configurator, AI tools can consider design intent (geometry) and then assess and offer multiple design solutions based on a set of adjustable criteria.
The data freed up by AI tools, however, can only be used if it can be delivered to the right stakeholder and at the right time. Paired with the right computational tools, AI-unearthed data can empower designers to make decisions not based just on their experience and knowledge, but also through multi-criteria data analysis, establishing a new baseline for how well-resolved buildings are designed.
Much-needed efficiencies
If timely data can reveal key elements, like the physics of moving materials, labour resources and equipment needed to make a design easy to construct, it would have a profound impact on design decisions and would provide the much-needed efficiencies throughout the project delivery process.
This is the endgame of design for constructability: a process involving computational and AI/machine learning tools that empower designers with accurate, quantified, and unseen contextual data at the right times, saving time, money and effort by avoiding costly redesigns. Design for constructability can become the baseline for how efficient buildings should be designed.
Joel Hutchines is vice-president, industrial construction at Slate Technologies, an AI software platform for the construction industry. Prior to joining Slate Technologies, he was the founder of Splash Modular, a company that developed solutions for industrialised construction.
Don’t miss out on BIM and digital construction news: sign up to receive the BIMplus newsletter.