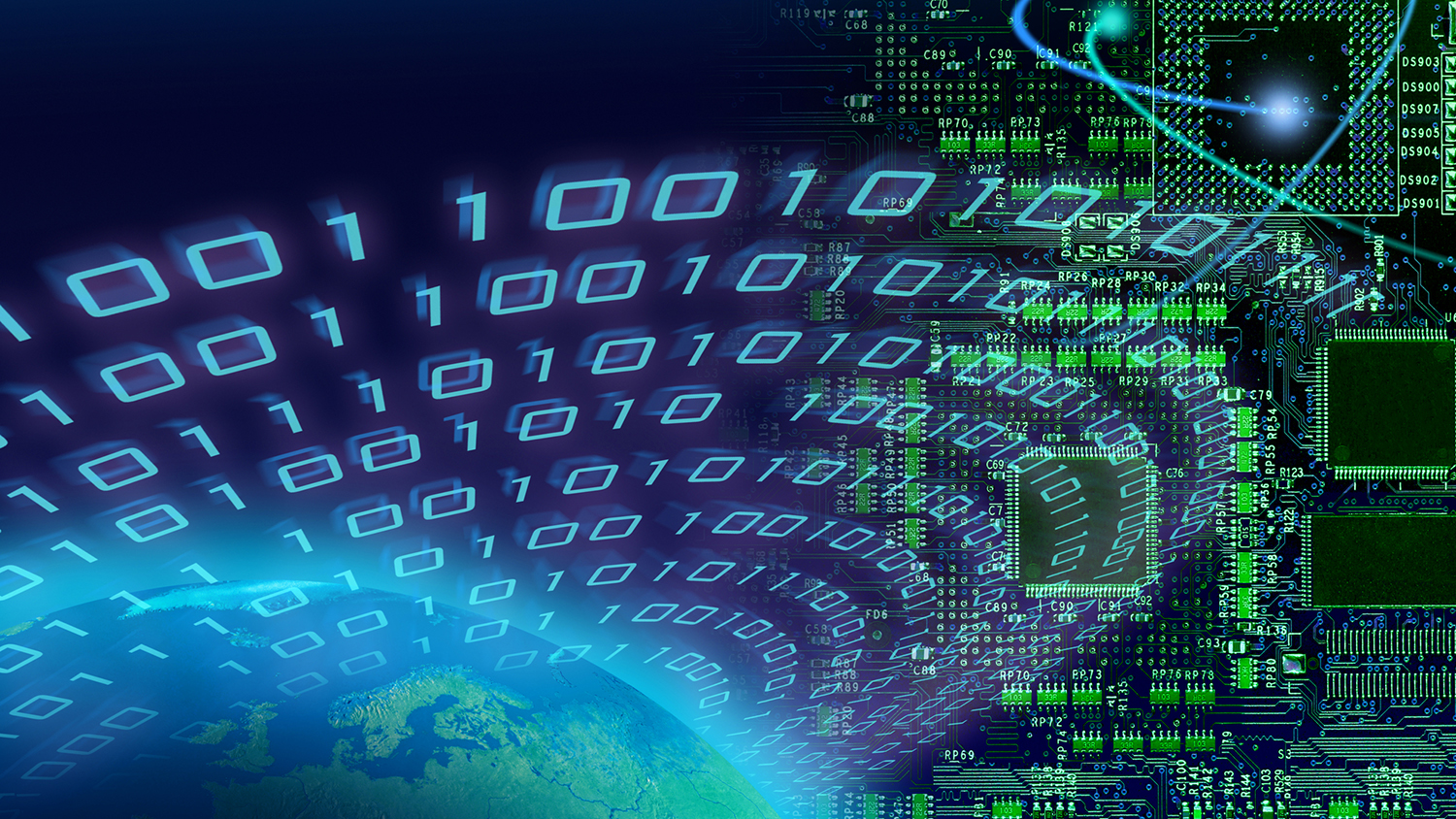
To fully maximise the benefits of integrated digital solutions, the industry must continue to focus on developing its workers’ digital skills, argues Andy Flood.
The construction industry has been investing in digital solutions since the early 2000s, but the pandemic significantly accelerated technology adoption. There has been a shift from project-based tech to integrated systems, with many construction businesses looking for easy-to-use solutions such as remote site management software and automated machine control.
Throughout the pandemic, businesses were forced to explore more radical digital solutions. With limits on human contact during lockdowns, contractors had to think innovatively about how they could get projects completed on time, accurately and within budget remotely.
Digital technologies made construction possible, even under covid restrictions. Project teams could gather and analyse accurate data and carry out high-quality work from any location. The result was a 14% increase in technology investment across the construction industry between 2019 and 2021. For example, the Sisk motorway bridge replacement project was managed remotely via Microsoft Teams and Bentley Systems Synchro, which allowed for a digital rehearsal of the build.
As the industry now looks to increase productivity and tackle pressures on material and labour supply chains, contractors are evaluating how they can use digital to build more efficient workflows. One thing is holding them back: a lack of digital skills.
Digital solutions may have been available for decades, but the sudden increase in pace of widespread adoption means that operator skills have not kept up. According to the McKinsey index, construction is one of the least digitised industries in the world. The reason these solutions feel new is because many onsite construction workers have not been trained in how to use them correctly and have given up on adoption before seeing the benefits.
What are the blockers to machine control adoption?
One of the key issues that can impact successful integration of new technology is the after-sales experience. Following a significant financial investment, contractors look to manufacturers for support with how to use the solutions, getting their team on board and understanding what data they need to be able to provide to maximise the compatibility of the technology with their fleet.
That is why, just like tablets and mobile phones, companies designing tech for the construction industry need to prioritise intuitive operation and easy-to understand visual displays. This allows the user to immediately understand how to use the tech and exploit the full potential of the system without specialist digital knowledge to maximise the potential ROI of a digital workflow.
Another factor is the setting of industry standards. Unlike other technologies, for example, an industry standard has not yet been set for machine control to ensure that customers understand what is required from them prior to the purchase to make the most of their investment.
Customers need access to particular radio frequencies and localisation data and manufacturers should be supporting with seeking this data. Unfortunately, many don’t.
What support is available?
The government is supporting the built environment by offering funding to adopt digital and upskill teams, enabling contractors to reduce the initial cost of implementing a new digital system. For example, the chancellor has confirmed there will be £65m available to digitise England’s planning system. This funding will support contractors as they move to digital by streamlining the planning stage, creating a fully digital project workflow.
Additionally, there has been significant investment in post-16 education with new T-levels in surveying, planning and onsite construction and £170m for apprenticeships and training that will help contractors to welcome new skilled workers and to upskill existing employees.
Manufacturers are also supporting adoption and upskilling, dedicating time and expertise to ensure customers understand how to make the most of the systems they invest in. Through training and support solutions (like the free myTopcon platform), users can receive online training and firmware and software updates to help them operate new and existing tools effortlessly.
New training needs
During the pandemic there was a shift in attitudes as contractors had the time to review their processes and assess how digital solutions could improve how they work.
High demand for skilled workers – fuelled by large projects like HS2 – means site managers are requesting more training for teams to ensure their employees can effectively use whatever technology they have introduced.
With practical, onsite skills a finite resource in the current market, demand for digital technology and training to help bridge the gap is increasing. Companies have realised it is difficult to find skilled workers for tasks like building foundations. Rather than competing for expensive engineers, they are purchasing machine control kits and training existing operators to use them as a long-term investment.
Looking to the future
As the industry embraces digital, it’s important that companies realise they cannot replace skilled workers with technology – the two must work together. Training and ongoing support are resources that companies must not neglect, and technology partners like Topcon are ensuring that these services are readily available to help the industry to tackle the skills shortage head on.
Andy Flood is UK business manager at Topcon Positioning GB.
Don’t miss out on BIM and digital construction news: sign up to receive the BIMplus newsletter.