We have not had to be overly contractual about the process as everyone has worked collaboratively. Building a fully coordinated model for the MEP services before we tendered construction enabled us to de-risk the process.– Jason Clark, project manager and director, UBS
Jason Clark, project manager and director at UBS, on embedding BIM at 5 Broadgate, the financial services firm’s new headquarters currently being fitted out in the City.
5 Broadgate started in 2009, so how advanced is its BIM implementation?
Pretty advanced. Although BIM wasn’t within the original brief, we were aware of it and kept a watching eye on where things were moving, then things started to change in 2010-2011. At that point, we realised we couldn’t construct a building to last 25 years and beyond and not have a full BIM model at the end of it. Somewhere between RIBA Stage D and E we asked our design partners whether they were experienced in BIM enough to take on the extra challenge of delivering a BIM model.
Some felt the task was too large – it is a highly technical, 700,000 sq ft building for 5,500-plus staff – but the interior architect, TP Bennett, and structural engineer, Watermans, were up for it, so we developed a strategy to produce architectural and structural models. Our construction manager [for the interior fit-out] ISG, then took responsibility for modelling M&E services to same level of detail, as well as creating a federated model.
What are the key benefits to UBS as client?
The main value is the ability to link BIM to our asset management tool, or computerised maintenance management system (CMMS). We also saw potential to synchronise it with our space planning tool, Archibus.
In terms of our soft landings programme, it has enabled us, for the first time, to assemble all our assets in one repository, which are currently held in numerous software tools and spreadsheets.
Was it tricky deciding which asset information would be useful?
Given the absence of COBie, at the time, we worked with the operational team to identify the asset data and data fields we needed to be embedded and populated in the model at handover.
A major challenge was overcoming the assumption that you need a high level of data detail for everything held within the model. Once we started to drill down into things we realised that, in reality, a lower level is okay for certain assets. For example, the cook suites in the catering areas are modelled with low detail in Revit, with links to provide much greater O&M and asset detail in the supporting documentation.
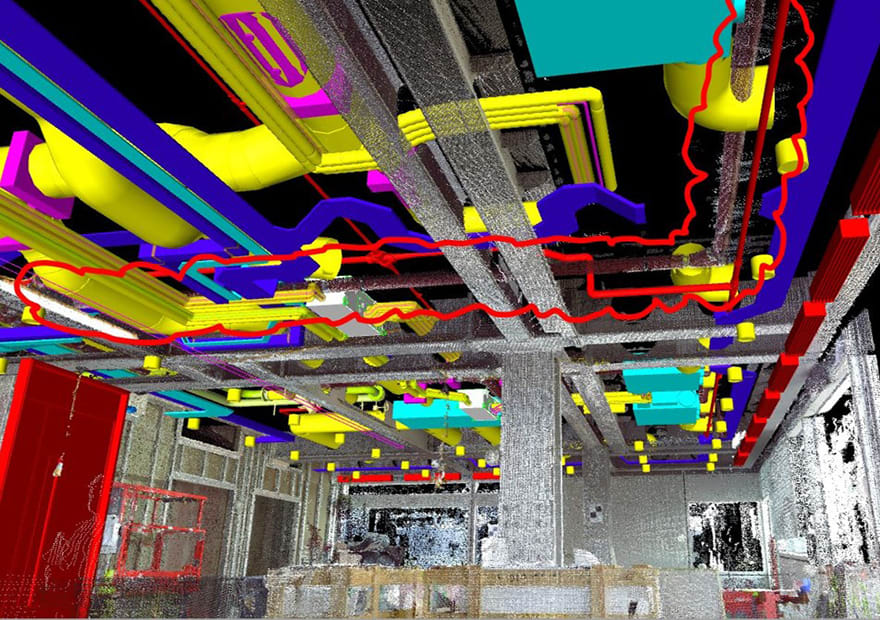
The MEP services model enabled UBS to de-risk the process
Is there enough guidance and best practice out there to help clients?
There is enough documentation and case studies, but it is critical to get your FM service delivery teams engaged, otherwise you are going down the COBie route of creating a generic asset database that might not fit your precise needs. You need to get the delivery team together to agree common asset strategies, data field requirements and how you will use the tool for on-going operations. The emergence of the NBS BIM Toolkit should really help people focus on the level of information and detail they want.
What has been your biggest BIM challenge on 5 Broadgate?
The fact that contractors prefer to utilise their own software tools. We designed in Revit, but our building services supplier wanted to continue using its Fabrication MEP software, which is great for installation and ordering materials and so on, but not so good for design and asset information. We faced the difficult decision of whether to continue using the Fab MEP tool, and Revit for architecture and structure elements, or to impose Revit MEP on the services team. You have to be flexible in your strategy.
Will you be requiring Level 2 BIM from supply chains going forward?
We won’t be mandating it, as it will become a natural choice for designers and contractors when they come to understand the benefits and how it can de-risk projects and improve efficiency. There will also be more of a pull from building operators when BIM integrates fully with their operational tools.
Have you seen any concrete cost savings as a result of using BIM?
We haven’t observed true cost value. At present, BIM pioneers are sponsoring the use of the technology and the cost savings the government is expecting have not yet transferred to the end user. However, I suspect that as more and more consultants and contractors become BIM savvy, and BIM becomes the tool of choice, rather than an option, those savings will start to emerge.
Are design consultants all charging a premium for delivering in BIM?
To some extent, on this project we have supported our designers’ development in BIM because they were appointed to design in 2D. As BIM becomes more commonplace that cost should level off, but designs will certainly not become cheaper. However, you could argue that clients are getting more for their money due to the higher level of detail and quality of the completed build.
Have BIM contractual arrangements been a challenge?
We have not had to be overly contractual about the process as everyone has worked collaboratively. Building a fully coordinated model for the MEP services before we tendered construction enabled us to de-risk the process. Having coordinated information to go to tender with took away some of the coordination issues when contractors came on board and worked up their own designs.
Are lower tier contractors lagging behind on BIM?
Some are, but that shouldn’t necessarily mean that you exclude them from projects. Do you select a contractor because they are up to Level 2 BIM, or because of their track record for quality and delivery? Currently that’s a difficult question to answer. On this project, we chose our delivery partners based on their experience and ability to deliver the job, then provided them with assistance with BIM where necessary. We took a collaborative approach, viewing BIM as just one aspect of the task.