The introduction of BIM to our industry was meant to be boost efficiencies and save work. So why in the design of services has this not resulted in more streamline processes, asks Dominic Sibbring, director of Digital Engineering Studio.
Digital Engineering Studio is a BIM outsource provider that specialises in the delivery of BIM projects for the MEP sector, and as such our client base is a mixture of MEP subcontractors and consultants. One of the first questions we ask when pricing a project for a contractor is: ‘Will we receive the consultant’s model? Our clients expect us to deliver the most cost-effective solution and taking over the model from the consultant often means that the bulk of the work is already in place.
Long before the MEP contractor is awarded the project the consultant has produced the design in a BIM environment. It is fair to assume that the consultant will have the technical expertise to deliver the proposal to suit the overall requirements of the project, but do they possess the specialist knowledge of the install? As such, the consultants are producing coordinated designs using BIM tools that provide enough detail for the project to satisfy the requirements at RIBA Stage 3/4 before the successful contractor takes over and develops further into RIBA Stage 5/6.
For many, BIM was first introduced in 2011 with the release of the Government Construction Strategy, with the Cabinet Office mandating its use on public sector projects with a deadline of April 2016. Back then the case studies surrounding the benefits of BIM were limited, but one of the biggest selling points was how BIM would save time for all involved.
Ambitious promises were made that through BIM, the information would be shared freely, rework would be eliminated, and issues would be resolved digitally before they had a time and cost implication on site.
Recently our experience has been different – on several of our latest projects, we have been employed by contractors and commissioned to take the consultant’s model and amend to LOD6. Consultants’ models are generally developed to LOD4 which typically entails detailed MEP designs, with items of plant, ducts, trays and pipes in positions that have been spatially coordinated between engineering services.
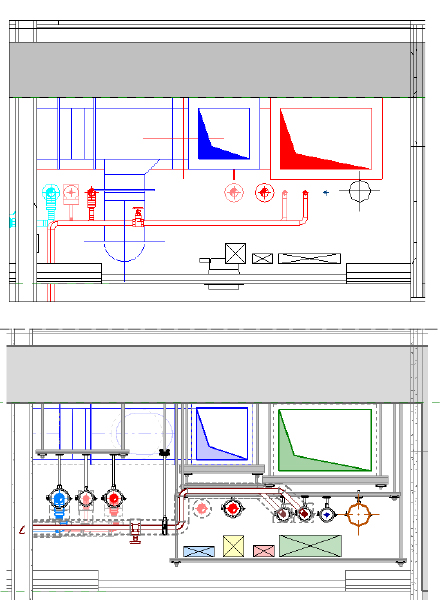
Top: How a typical consultant’s model may look. Above: How a typical contractor’s model may look
A technical design model such as this will present enough information for the tendering contractors to price from and confidence that proposal is achievable within the constraints of the building.
However, an LOD4 model is not inclusive of all of the components required by the contractor to deliver an installation model, for example, there will be no Unistrut, service hangers, bracketry, correct pipe/duct insulation (occasionally) or structural openings. Adding in this additional detail will often lead to an extensive adjustment and by the time it is complete has led to an almost complete remodel.
If the building services have been modelled at RIBA 3/4 without consideration for insulation or spatial allocation for supports then often adding these in will cause a multitude of conflicts. Adding a simple 41mm Unistrut to the underside of a duct can be the difference between pipework seemingly passing below through a space, clash-free, to requiring an entire rethink of where they can be installed.
After encountering issues like this on numerous projects we considered if our time would be best spent if we started the project again rather than constantly tweak the existing design. We decided to explore further and asked our followers on LinkedIn to get involved in a poll. We asked MEP contractors “do you amend the consultant’s RIBA Stage 3/4 model and develop it further or do you start again?”
We had 148 participants take part and from the population, 82 people said that they develop the model they receive whereas 66 people said they start again. A percentage split of 55% in favour of developing the model.
The findings will come as a surprise to many who were encouraged by the notion that BIM would reduce rework and save time. It is disheartening to see such a high percentage of participants choosing to start the work again and all of the initial time/effort the consultant has spent at the expense of the client made redundant.
Many of the contractors we spoke to suggested that developing the consultants model would be their preferred solution however changes are inevitable as they take the model to the next level of detail. They cited the lack of supports, insulation and bracketry means that once added, the building services cannot remain in their current arrangement and their comments corroborated our findings with the consensus that as the model progresses and more detail is added one minor change leads to another, which leads to another and by the time the project is finished it is almost a complete start over.
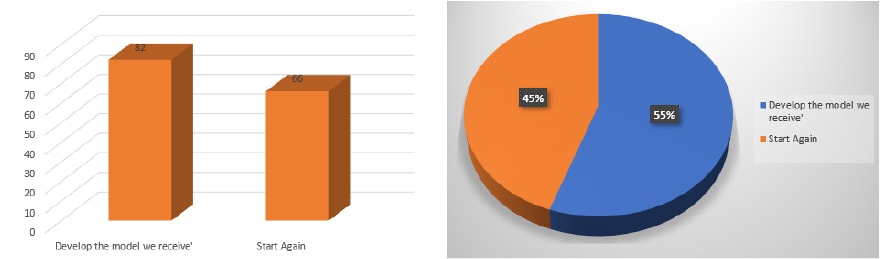
It is no criticism of consultants for not including the information within their models, they are delivering an acceptable solution to fulfil their requirements for the project at that stage. Likewise, the installation requirements of MEP systems are a specialism within itself and contractors are the best placed to include this information.
However, this doesn’t change the fact that modelling the information twice is an incredibly inefficient and costly process for the client to agree to and not aligned with the core principles of BIM. As an industry, we must look to bridge the gap and bring design and install closer together so the transition of information from one team to another can be done with minimum waste.
We as a business, with an interest on both sides, undertake a process of modelling with the install in mind. Our experience of modelling at Stage 5/6 allows us to deliver a more realistic product at Stage 3/4 that considers parameters such as access requirements for maintainable equipment and spatial allocation for the services for sufficient install of bracketry and support systems that will follow thus reducing the need for the contractor to make significant modifications to model at the later stages.
The introduction of BIM to our industry has been a positive addition but we must not stand still, we must continue to streamline processes and ensure that rework is eliminated where possible. If contractors willingly accept that building the model again is just part of the BIM process then we are at risk of losing one of BIMs key assets, and if we are doing everything twice are we moving forward at all?
Comments
Comments are closed.
What a great challenge to issue! The current system is producing LOD3/4 information that isn’t fit for purpose (as a foundation for development with minimal rework to LOD5/6). Surely, an AI assisted design software package could incorporate specialist knowledge of insulation, bracketry and maintainability/accessibility to create a LOD3/4 design that can be developed with minimal adjustment. Who will take up the challenge?
This is further evidence that specialist contractor engagement must move upstream to Stage 4 at least and to Stage 3 where the main contractor also enters early. Consultants modelling without suitable volumetric allowances are naive and clients should not pay for wasted work. They should practice early contractor involvement instead.
Thank you for this very insightful article, Dominic.
I recognize all of the above-mentioned issues and challenges. This issue is particularly prominent in D&B projects. Traditional procurement route is not as severely impacted by this gap in LOD as the design team is largely retained which gives the task teams more control and leeway. Their entire approached is, in fact, shaped by knowing that it’s going to be them upgrading their own models and taking them to the next level of detail, so naturally, they tend to ‘care’ more?
I deliver Information Management services and frequently author the Information Requirements for project. This includes specifying the Level of Information Need (formerly known as LOD). I feel like the current ISO 19650 standard doesn’t sufficiently cover the different approaches to modelling associated with the different procurement routes.
I believe this issue could be greatly reduced if the same duty of care was applied in D&B projects as it is in traditionally delivered projects. Leaving the model in a good state and well thought-trough for the Contractor’s seamless take over, should be picked up as a requirement in the information standards.
Starting the model over from scratch is, indeed, completely against the fundamental principles of BIM.