A prototype robotic production line that will demonstrate how standardised offsite components could be manufactured for schools and housing is being developed in Coventry.
The Manufacturing Technology Centre (MTC), the government-funded research facility focused on applying manufacturing systems to different sectors, is converting one of its manufacturing halls into a mini-factory that will utilise robots and automated assembly systems to produce components and modules for prototype homes and schools.
The facility will function as a live demonstrator to encourage visiting companies to adopt the advanced techniques within their businesses.
An initial project will see the hall used to produce modules for a reconfigurable “house of the future” designed by school children.
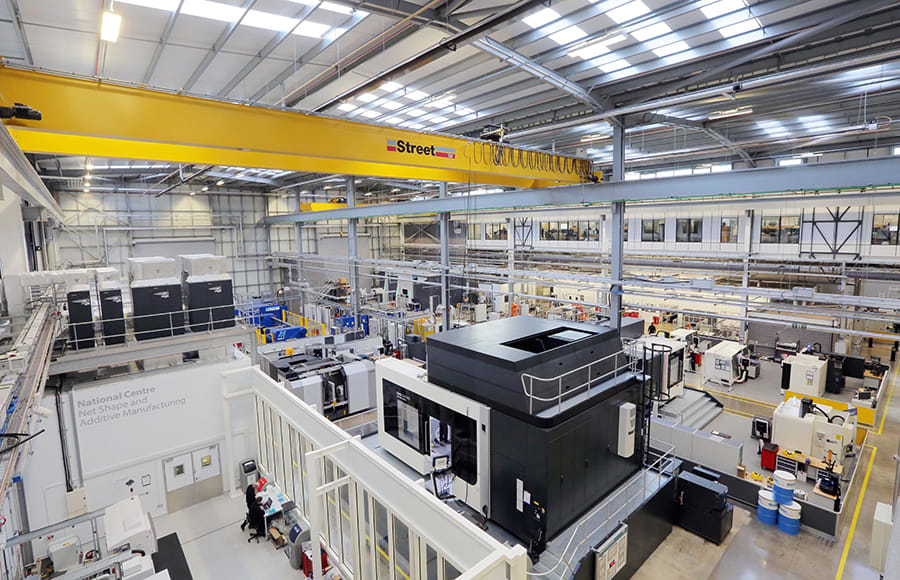
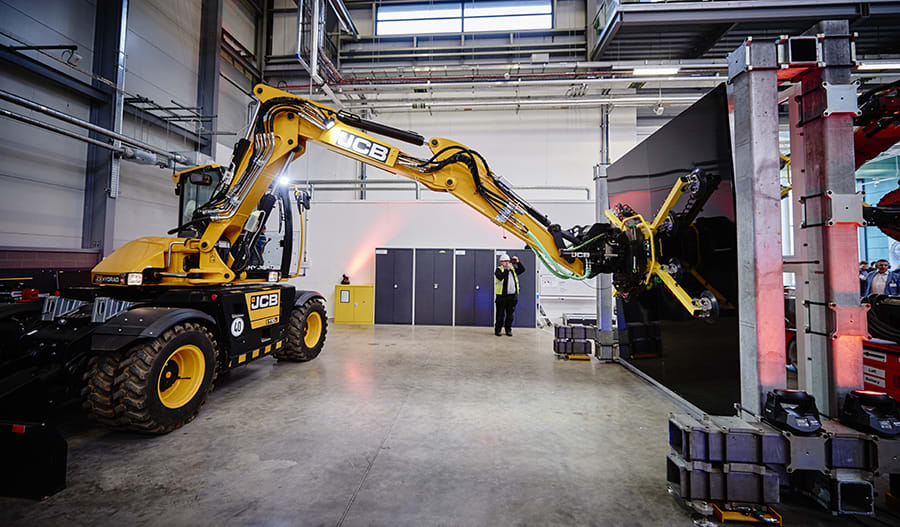
The facility will function as a live demonstrator
The 2019 Design Challenge, launched by the Construction Innovation Hub and architect George Clark’s charity MOBIE (Ministry of Building Innovation and Education), asked children at schools across the country to design a 21st Century home can be expanded as a family’s needs and circumstances change.
The winning design will be developed by architects at MOBIE LAB and professionally structurally engineered to enable the robotic manufacture and assembly of modules at MTC.
Neil Rawlinson, strategic development director at MTC, told BIM+: “When the competition winner is chosen [on 21 June] we will be looking for the industry to come forward and help us build some of the modules. The ultimate aim is to publicly showcase how these types of components and manufacturing systems can be used to build both homes and schools.”
The competition asked entrants to design a modular steel structure comprising a series of cube-shaped pods fabricated from 150mm box section steel. A maximum of 16 pods are permitted which, allowing for wall thickness, will provide an internal space of 96 sq m suitable for five people.
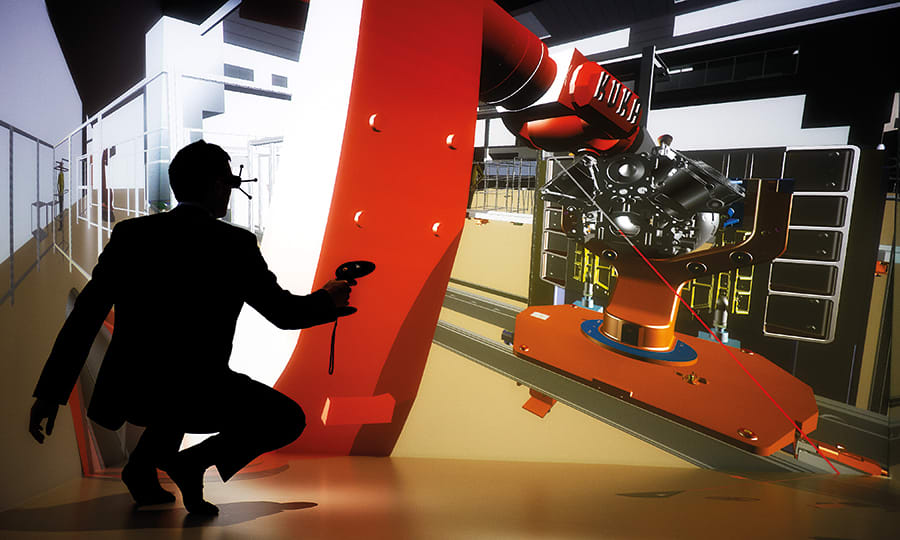
The scheme will be “plug and play” with all modules designed for manufacture and assembly and all internal services and finishes installed before delivery to site. The maximum length of units assembled in the factory will be 12m (four pods back to back) for ease of transportation.
MTC received a share of £72m government funding at the end of last year to push manufacturing techniques into construction. Partner contractors include Skanska, Kier and Willmott Dixon and academic partners include the University of Birmingham, University of Nottingham and Loughborough University.
MTC set up the Seismic Consortium, comprising construction consultant Blacc, design practice Bryden Wood and the offsite construction firms Elliott and The McAvoy Group, to transform the design and delivery of primary schools.
Seismic is developing a standardised set of components and assemblies that can be produced by multiple offsite specialists to improve economies and efficiencies of scale. Bryden Wood has developed a design tool that can be used by teachers to configure schools based on standard components.