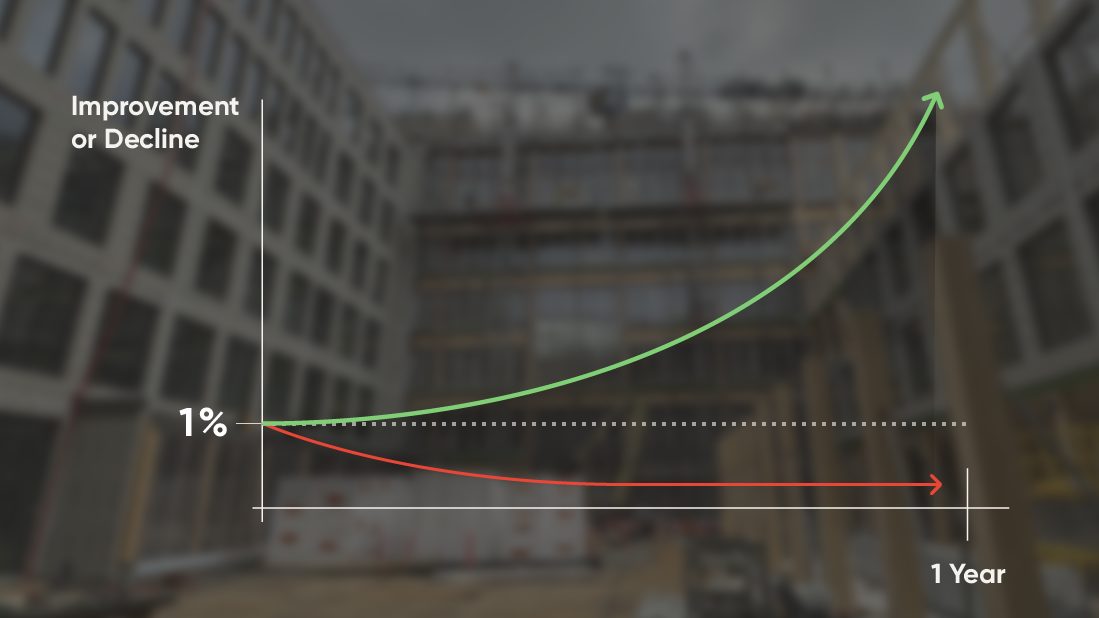
What can construction learn from the British cycling team that has dominated recent Olympics? That by adopting a marginal gains approach to work, huge efficiencies can be gained.
When he became the British cycling team’s performance director in 2003, Sir Dave Brailsford took a surprising approach. Convinced that every single element of racing – no matter how seemingly insignificant – affected overall performance, he began searching for teeny-tiny margins of improvement. “If I break down everything I can think of that goes into riding a bike, and then improve it by 1%, I should get a significant increase when I put them all together,” he said.
Brailsford was soon proved right. Together, his tiny improvements – such as using heated shorts to keep the muscles warm, or rubbing alcohol on the tires for better grip – won the team its first of a string of Olympic gold medals.
Just five years after Brailsford took over, the Brits ruled the Olympic Games in Beijing, winning 60% of all gold medals in their discipline and setting seven world records four years later. This legacy has continued to the Paris Olympics.
Now one of the guiding principles of sports coaching, Brailsford’s ‘marginal gains approach’ demonstrates how breaking down complex problems into smaller, measurable tasks can lead to a remarkable efficiency boost.
It’s a philosophy that also offers valuable lessons for the construction industry. When dissecting and individually analysing each component of a building project, project managers and site teams can find many diverse opportunities to enhance work processes. For instance, regularly quantifying the completion rates of planned tasks against actual progress can reveal deep insights into the efficiency of both scheduling and execution, enabling targeted and proactive strategies for improvement.
Let’s look at this more closely.
The practice of assessing each trade’s progress against milestones is part of a framework known as Performance Driven Construction Management (PDCM). The methodology centres on setting key metrics and equipping teams with data-driven techniques to ensure actions are aligned with solid facts.
Reducing return visits is just one example of how adopting PDCM helps project teams adopt a proactive stance and make Brailsford-style incremental improvements. Currently, over 10% of activities on construction sites are not completed during the first visit. That’s because trades often say they’ve finished a task, and without data to prove or disprove their claims, project managers have to take them at their word.
As such, return visits are extremely common, regardless of project type or size. Even projects completed with very little schedule delay (less than 10%) see an average of three return visits per area.
If teams can track every trade’s progress against their assigned tasks down to the percentage point, they can flag the incomplete two, three, or even 10% of tasks before trades move on, proactively preventing many return visits.
If we want to elevate project performance this way, we need to be able to efficiently capture and process accurate data. But the diverse activities, stakeholders and complexities involved in each building project can make this a daunting task. Traditional methods, based on manual data collection, are not just time-consuming and error-prone, but cannot provide the appropriate depth and granularity.
This is where technology comes in. It can capture far more data than the human eye, unlocking a level of granular evaluation that allows project teams to monitor progress down to every last light fixture, plug socket, and door frame. Used together, technologies like BIM, IoT, AI, sophisticated project management software and lean methodologies enable Performance Driven Construction Management (PDCM).
Key performance indicators (KPIs) such as area utilisation, percent plan complete (PPC), and delay forecast become invaluable for project managers. These metrics not only facilitate more accurate project tracking and forecasting, they also enable early identification and mitigation of potential delays, thereby enhancing overall project efficiency.
Explore Buildots’ detailed whitepaper and learn how leading contractors worldwide are embracing PDCM to become more proactive, efficient and successful.