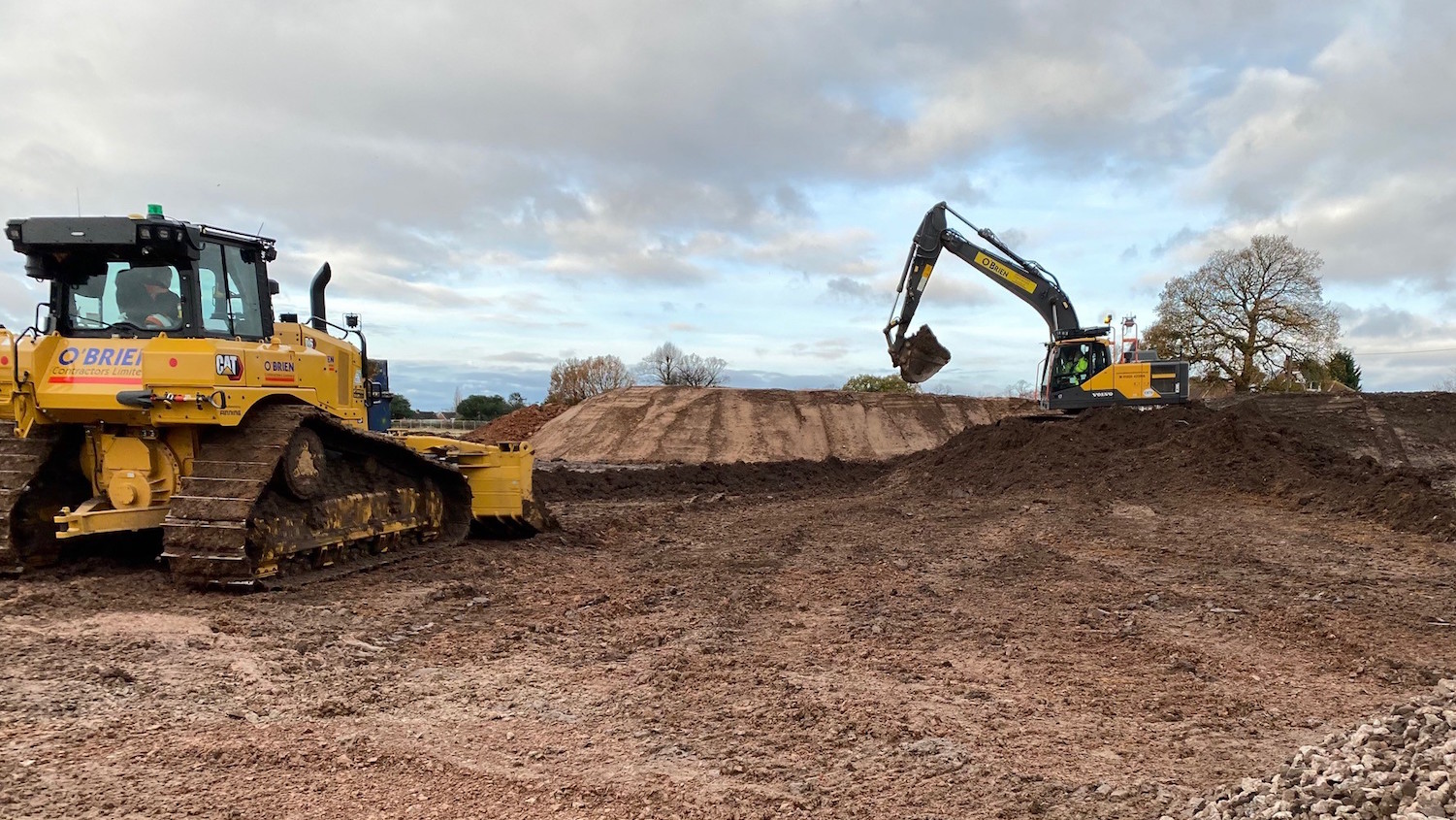
The construction industry can ill-afford to ignore the benefits of machine control and automation of plant. Topcon GB estimations suggest that the number of machines with Topcon technology currently fitted could reduce CO2 by about 600,000 tonnes a year if automation was used.
Topcon’s Andy Flood believes machine control and automation of plant are an essential part of the industry’s journey towards digitalisation.
As global focus on sustainability and net-zero targets continues to surge, the pressure is on for businesses to adapt and operate in a more digital and sustainable manner. Governments around the world are publicly committing to net-zero targets. Earlier this year, the UK Green Building Council called for the introduction of regulations to avoid missing these goals.
The key to sustainable success lies in precision and intelligence. Technologies such as Topcon’s offer an increased level of data that provides an accurate, real-time picture of what is happening on the ground. With this knowledge, site managers can strategically adjust workflows, minimising errors, reducing waste, and preventing unnecessary and costly rework.
Responsible businesses will naturally turn their attention to these more sustainable, digital practices. But with regulations tightening, this will no longer be a business choice. Implementation of sustainable processes will soon become mandatory. And the first adopter firms will benefit the most.
Tackling the skills crisis
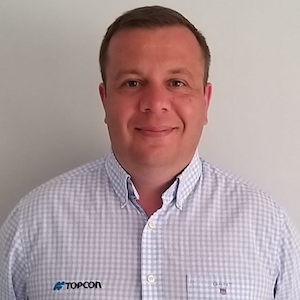
“We must reframe our thinking, no longer considering the skills gap a problem, but rather an opportunity to upskill the existing workforce.”
In addition to the pressure that climate change exerts on the industry, the UK is in the midst of a skills crisis. The dwindling numbers of construction workers will have serious implications for the country’s future. If left unchecked, it will result in the stalling of crucial infrastructure projects.
The adoption of software that enables full workflow machine control, including monitoring and data analysis, allows smaller, less experienced teams of operators to successfully complete jobs to the same or better standards as higher-qualified teams. And as the employee demographic shifts to include more of the Gen Z workforce, it’s the technological advances that will attract and excite these digital natives.
As an industry, we must reframe our thinking, no longer considering the skills gap a problem, but rather an opportunity to upskill the existing workforce, teaching them to embrace data, technology, and automation, and the advancements these can bring to the sector.
The future of construction
Looking ahead to the near future, automated technology will play a key role in meeting sustainability targets and underpins the long-term goal of low-carbon operations. A fully automated machine control workflow increases precision and ensures minimum material wastage and maximum efficiency. Reduced human error removes the need for costly reworks: mistakes can be detected and rectified much earlier, preventing project delays. From a sustainability perspective, reducing the number of errors and wastage helps to decrease carbon emissions, with less need for heavy machinery to return to site for corrective rework.
The latest machine control technologies are also an opportunity to manage construction processes remotely. Project managers have the ability to review progress and make any necessary changes from anywhere in the world. Thus reducing commuting emissions and minimising the health and safety risks associated with onsite work.
With a better understanding of construction data, project managers can more accurately estimate the time and materials needed for each part of a job. This insight allows businesses to efficiently allocate both their equipment and personnel resources, allowing them to break ground on new projects sooner than would previously have been possible.
Low-carbon operation goals
“Reducing the number of errors helps to decrease carbon emissions, with less need for machinery to return to site for rework.”
As well as driving short-term sustainability improvements, the adoption of automated technology will lay the foundation for construction businesses to work towards low-carbon operation goals. Longer-term implementation of automation and AI will increase project efficiency and profitability, ensuring that the majority of onsite work is right first time and reducing the amount of supervision required to complete projects. Solutions like Topcon’s MC-X machine control and Sitelink 3D software are already bringing these ideas to life. We are better equipped to meet the industry’s future sustainability targets by learning from the in-depth data that these systems provide.
Across the construction industry, modernisation is paving the way for a more sustainable future. When combined with the advances in electric heavy machinery, automation technology innovations will support the significant reduction of carbon emissions across projects. And from a business standpoint, these changes increase productivity and profitability, protecting business trading futures, as well as the future of our planet.
Andy Flood is UK business manager at Topcon GB.
Don’t miss out on BIM and digital construction news: sign up to receive the BIMplus newsletter.