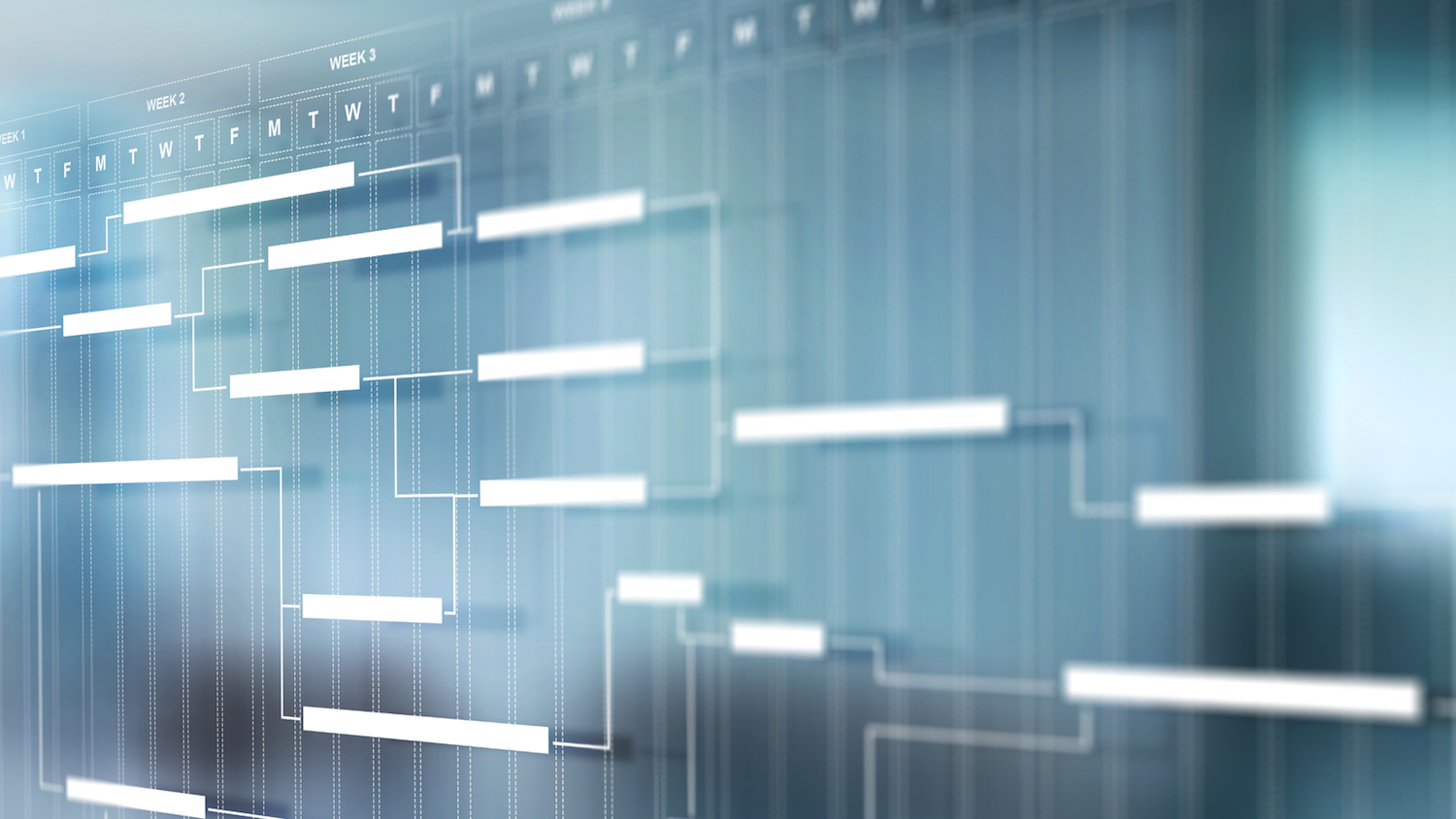
Can we connect RFID with BIM to further improve lean construction practices? Dr Mohammad Mayouf thinks so.
The construction sector has sought to integrate lean-based practices and processes through focusing on waste reduction, optimised flow and continuous improvement. Lean practices in construction, however, often fall short when it comes to real-time adaptability and precise tracking of resources. Traditional tools like the Last Planner System provide a framework, but lack the technological support for dynamic, data-driven adjustments as projects evolve.
Without fully integrated digital solutions, the sector struggles to align its lean aspirations with the complex, fast-paced realities of modern construction sites.
The key challenges in lean tracking are:
- Lack of real-time data for dynamic adjustments. Manual data entry and delayed updates mean project teams cannot promptly adapt to onsite changes, often resulting in misaligned workflows and lost productivity.
- Inventory and resource management inefficiencies. Without real-time tracking, projects face issues such as overordering or delayed deliveries, which can disrupt the flow of materials and labour. These inefficiencies lead to excess inventory or idle time, undermining lean objectives by creating additional waste and increasing costs.
- Limited integration with digital models. Lean metrics, such as resource usage and schedule adherence, rarely integrate smoothly with BIM models. This disconnect prevents teams from visualising lean activities in a synchronised, data-rich environment, limiting the potential for predictive insights and proactive adjustments.
Why data-driven approaches are transformative
In its broader context, lean practices often focus on reducing waste, but also aim to improve the scheduling process. Waste reduction is dependent on many variables, including site logistics, materials used and time efficiency, whereas scheduling can be impacted by the method of construction, resources used and accountability of risks. This reflects the complexity of holistic accountability of lean activities, but also rationalises the need for an effective ‘trackable mechanism’.
Technologically, integrating data-driven tools like RFID with BIM supports a pull-based system that provides real-time data on resources and activities, enhancing lean’s just-in-time delivery by tracking material location and condition, thus reducing excess onsite inventory.
Studies show that combining RFID with BIM improves schedule performance (Li et al, 2017) and streamlines material flow (Chen et al, 2020). Procore (2024) highlights similar findings, emphasising that while these tools enhance onsite tracking, a data-focused approach is essential to create synchronised data harmony across lean activities.
A data-driven lens: rethinking accountability for lean activities
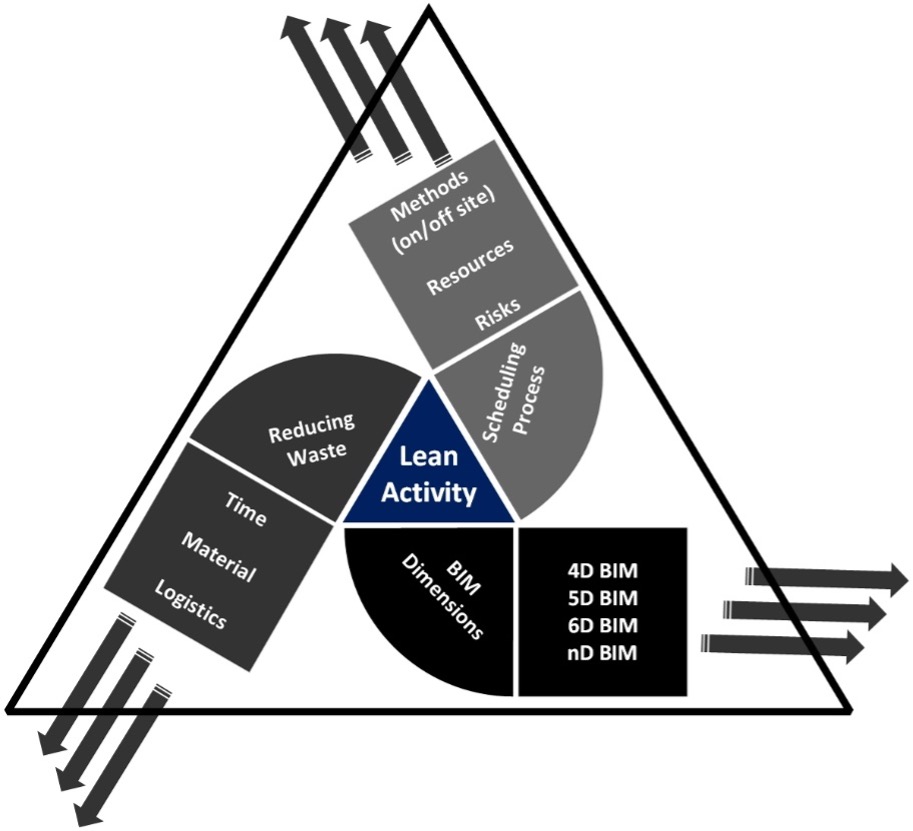
The above figure illustrates a 3D conceptual view of lean activities where the dimensions are: reducing waste, scheduling process and BIM dimensions. While all dimensions presented in the conceptual model are interconnected, this view provides a more focused insight into the parameters for each of the dimensions. To demystify this, the below table is provided.
Parameter | Textual Data | Numerical Data | Graphical Data |
Time | ✗ | ✓ | ✗ |
Material | ✓ | ✓ | ✗ |
Logistics | ✓ | ✓ | ✗ |
Methods (On/Off-Site) | ✓ | ✓ | ✓ |
Resources | ✓ | ✓ | ✗ |
Risks | ✓ | ✓ | ✗ |
4D, 5D, 6D, nD | ✓ | ✓ | ✓ |
The table complements the framework by linking specific parameters (e.g. time, material, logistics) to the types of data they rely on: textual, numerical and graphical. This breakdown supports a comprehensive approach to data integration:
- time and materials, critical for tracking real-time lean activities, are represented mostly by numerical data, with materials also having a textual component for detailed documentation;
- logistics and resources demand a blend of textual and numerical data to manage availability and scheduling effectively; and
- 4D, 5D, 6D BIM dimensions require a combination of all data types, allowing for multi-dimensional insights into lean activities that address everything from cost and time to sustainability impacts.
Is RFID a solution to track lean activities?
- Reducing waste: RFID tags affixed to materials, equipment and resources provide continuous location and status updates, which reduce the risk of overstocking or material shortages on site. By linking RFID data to the framework’s material and logistics parameters, teams can monitor inventory levels and prevent waste by delivering materials only when needed, supporting a just-in-time approach to construction.
- Scheduling process: the time and resources parameters in the table above benefit from RFID’s ability to provide live data on resource usage and workforce allocation. This data enables real-time adjustments to the project schedule, helping ensure that resources are available exactly when required. RFID can track equipment movement and usage, allowing teams to optimise resource allocation, minimise idle time, and reduce delays.
- BIM integration: by feeding RFID data into BIM models (particularly 4D and 5D BIM), construction teams gain a visual, time-linked representation of project progress and material flow. As noted in the framework, the integration of 4D, 5D, and nD BIM requires a combination of textual, numerical and graphical data. RFID provides the numerical and status data that, when integrated with BIM, enables a comprehensive digital twin, allowing stakeholders to visualise the project in real-time and anticipate potential bottlenecks or resource conflicts before they arise.
Don’t miss out on BIM and digital construction news: sign up to receive the BIMplus newsletter.