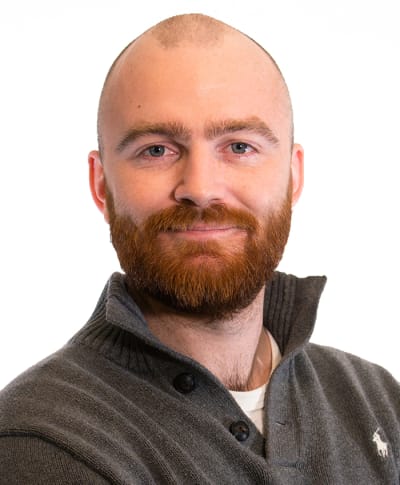
‘How can we overcome the complexities of vertical construction and deliver on-budget, on-time, sustainably-built buildings that are fit for the future?’ Chris Emery, Topcon Positioning
Chris Emery, senior manager for vertical construction at Topcon Positioning, discusses the new age of technology increasing productivity and reducing conflicts and mistakes for tall building projects, improving delivery times and bottom lines while capturing a true digital twin.
A growing population continues to put pressure on buildings and infrastructure across the world. As our numbers grow, an increasing amount of us are moving to cities – 70% of the world’s population is expected to live in cities by 2050. With so little space and so many people to accommodate, construction firms are looking up for the solution.
But the industry is notoriously behind the curve when it comes to modernisation, meaning the delivery of vertical projects is often slow and difficult when using traditional construction workflows. Professionals alongside government bodies are urging more project delivery teams to adopt new digital methods to avoid any additional time and cost needed for reworks.
The idea of the sky being the limit has never been truer for the construction industry. But if you think of sky scrapers, you don’t necessarily think of the UK. While the number of tall buildings in England – outside of cathedrals and industrial chimneys – has increased significantly in recent decades, we’re still playing catch up to meet demand, with more people wanting to live and work in our major cities like London, Manchester, Birmingham and Leeds.
At the same time, we’re facing the challenges of innovating new and better ways of building taller, we still have to adhere to requirements set by timelines and budgets, with the ever-increasing need to reduce material waste, bring down carbon emissions and provide meaningful data. How can we overcome the complexities of vertical construction and deliver on-budget, on-time, sustainably-built buildings that are fit for the future?
Part of the answer lies in technology, and this technology already exists and delivers benefits for forward-thinking construction firms across the UK.
Time is money
Building upwards requires a significant investment of time in design and planning to ensure the structure, while being built and once complete, is stable and safe. To make sure project delivery teams are sticking to that meticulously crafted design, regular verification of the as-built form is critical.
Without this, misplacements and deviations are easily missed, which can have a knock-on impact on progress ahead of the next scheduled scan and check, where the scale and eventual cost of the issue escalates. Verification technology also allows us to account for and adapt to unanticipated design variations almost instantly.
Verification technology has been available for years, but it has been a lengthy and expensive process. Many construction firms have needed to outsource the equipment and expertise to third-party scanning teams, meaning there would often be months between scans due to budget constraints not permitting frequent data collection. The reality is that without constant validation and verification onsite for every part of the build, mistakes or variations that are not tracked will inevitably lead to waste, delays and overspend.
With industry reports suggesting that 5-12% of construction budgets are being used in fixes and rework, this is a clear area where improvements can be made so budgets are not exceeded. A new workflow specifically for vertical construction projects has been introduced to the market just this year.
A high-quality scanner combined with a robotic total station provides one device that is quick, easy to use for site engineers and feeds into powerful software that can provide reports on items out of tolerance in near real-time. The GTL-1000, alongside Topcon’s MAGNET and ClearEdge Verity software, enables this verification at any and every stage, while compiling a digital picture of the as-built structure. With this, reworks can become a thing of the past.
Responsible resource use
If we look at reducing reworks through regular validation, we can instantly expect a reduction in material waste from issue areas being removed and reconstructed. Couple this with reduced time using plant and equipment for reworks, and the project could also expect to see resource savings, not only in workforce time, but also in energy usage.
As reworks have such a significant impact on budgets and timescales, there’s opportunity to readjust the flow of finances into improvements on site and for the final structure. Funds can be funnelled into better-quality materials that are more sustainable, more easily maintained or are even self-regulating or healing to reduce maintenance costs for the future.
With the workforce remaining focused on optimal tasks, rather than reworks, timescales are less likely to spiral, keeping team members focused and working appropriate hours, rather than fatigued and working around the clock. This will keep site safety at the top of the agenda and allows for a happier, more productive team.
Time savings on mistakes also give the project more flexibility and breathing space to adjust to late design changes.
Multi-stakeholder collaboration
There’s a perception in the industry among many, but not all, that there’s too much risk involved in sharing intellectual property. That a company’s data should remain the sole property of that company, and releasing that information could mean some sort of financial loss.
However, a report, PlanGrid, Construction Disconnected,compiled by PlanGrid, an Autodesk company, providing productivity software to the industry, says: “Globally, an average of 52% of rework was caused by poor project data and communication, representing a worldwide cost of US$280bn in 2018.” There’s a clear cause and effect presented here that not sharing data results in financial loss, rather than the other way around.
Furthermore, if it were possible to calculate the emissions caused by these reworks across the globe, imagine the impact we could have on global carbon reduction targets if we were able to better manage projects to avoid reworks. But we can. Software exists that shares designs, design updates and scan data all in real time with teams in offices and on site, no matter where they are in the world.
This ensures everyone is essentially singing from the same hymn sheet to avoid any crossovers of old and the latest data sets. And technology exists to ensure all of the machinery being used is working from the same data, too – Topcon’s MAGNET suite is just one example of full project delivery team connectivity.
After construction
Once built, ongoing maintenance of tall buildings is key. With these structures always surrounded by other buildings in heavily populated areas – to make the most of the sky space for residents and businesses – any decay or failure could be catastrophic.
Appropriate data captured during the construction of the building and once finished can be shared with building facilitators to ensure appropriate maintenance of the building throughout its lifecycle. This data can be the whole history of the structure, including the exact dimensions of steel beams, any items marginally out of tolerance that were approved, and provides a full digital twin for future planning for extensions, adjustments or demolition.
We know there is technology available to better improve the construction process of tall buildings, but take-up of this technology is slow. The construction industry has been berating itself over the critical comments in the Farmer Review of 2016, and are talking about modernisation and the adoption of technology. But, as Topcon’s own research with the Institution of Civil Engineers, Breaking Barriers in Infrastructure in 2018 found, current corporate culture is one of the biggest barriers to the adoption of new technology and working processes, second only to financial implications.
As more businesses realise the opportunities and possibilities of technology and step away from old processes to lead the way, I hope and expect that we will see more consultants, contractors and full project delivery teams backing the technology that can help us reach new heights.