3D modelling, sensors, drones and automatic plant are becoming more common in the groundworks sector as consultants and contractors embrace new technology. Stephen Cousins reports.
Ground engineering projects may stand at the grimy front end of construction, but pioneering firms are showing how 21st century digital technologies can transform the way excavation and concrete foundation works are being designed, monitored and delivered.
Consultants and contractors are showing how advanced computational design can provide deeper insights into geotechnical conditions and the likely impact of new foundation structures.
Expanding use of 3D modelling and BIM is helping improve design coordination and the communication of complex programmes of work. Sensor technology is making monitoring structures simpler and more cost effective, increasingly becoming a requirement rather than an optional add-on.
Meanwhile, emerging techniques such as the use of drones for machinery inspections, auto-erecting plant and 360 vision cameras on vehicles promise to make operations more efficient and safer.
Uptake of BIM has grown significantly over the past couple of years, but the focus is typically on above-ground structures, with site geology and subsurface often left out of the equation.
Ground engineers and contractors are still often reliant on working with paper and pen, but forward-thinking teams are trying to push the boundaries and apply specialist digital databases and 3D software to simulate and solve groundworks issues and improve design collaboration and coordination.
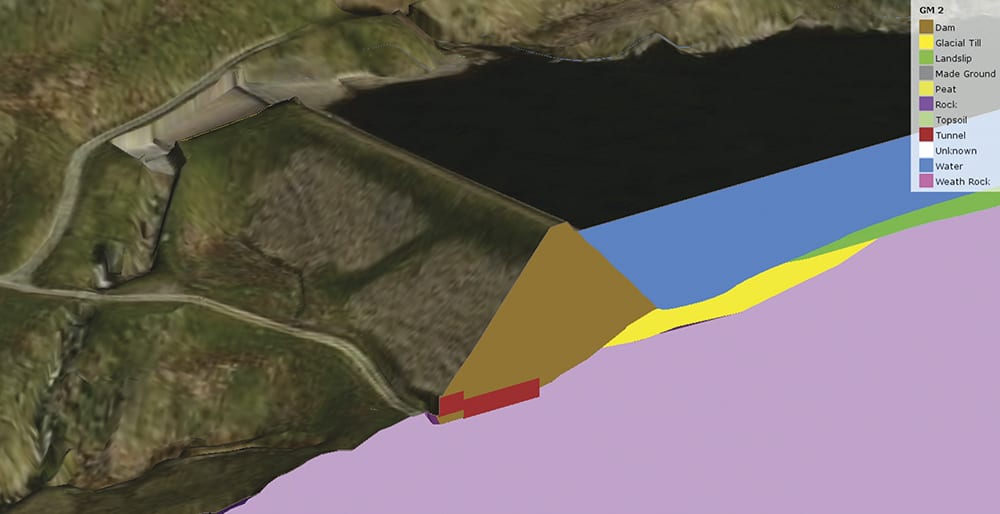
Mott MacDonald has teamed up with Software House to create an advanced 3D geological modelling tool, which was used to visualise and plan sensitive remedial works for an existing embankment dam in northern England
Owen Francis, divisional engineering manager at geotechnical company BAM Ritchies, tells CM: “Like most contractors, we don’t tend to receive digital models of projects from the scheme designers. Far from being put off by this, we have taken the opportunity to train staff to create models from a range of information sources.
Clash detection is one of the key processes we use, whether selecting the most appropriate item of plant or reviewing the risk of striking services or known obstructions prior to constructing foundations.”
Capturing data in the field
The use of data-rich 3D models enables BAM Ritchies to communicate complex information to site teams and capture site data digitally in the field, to monitor progress.
“As the works progress, as-built data is added to the model and our customers are becoming more used to receiving a digital model of the as-constructed assets at the end of the project,” adds Francis.
Mott MacDonald recently teamed up with software developer Software House to create an advanced 3D geological modelling tool able to more accurately communicate ground conditions and risks to project teams when planning work.
The process involves building a 3D model of existing ground conditions, based on data from borehole logs, geological mapping and trial pit data, then exporting it into BIM tool Autodesk Navisworks where construction planners superimpose details of excavation and foundation works to be carried out on site.
The approach has been applied on a range of multi-sector projects, including oil and gas and metro schemes. It was recently used to visualise and plan sensitive remedial works for an existing embankment dam in the north of England that was affected by landslip and surrounded by complex geology.
Anthony O’Brien, global practice lead for geotechnics at Mott MacDonald, says: “Having this 3D visual tool enables the whole team, whether specialists or not, to more readily understand the issues so everyone is talking the same language when planning work. We will be using it as our day-to-day tool to communicate the 3D geological environment and ground risks to project managers and clients and construction managers.”
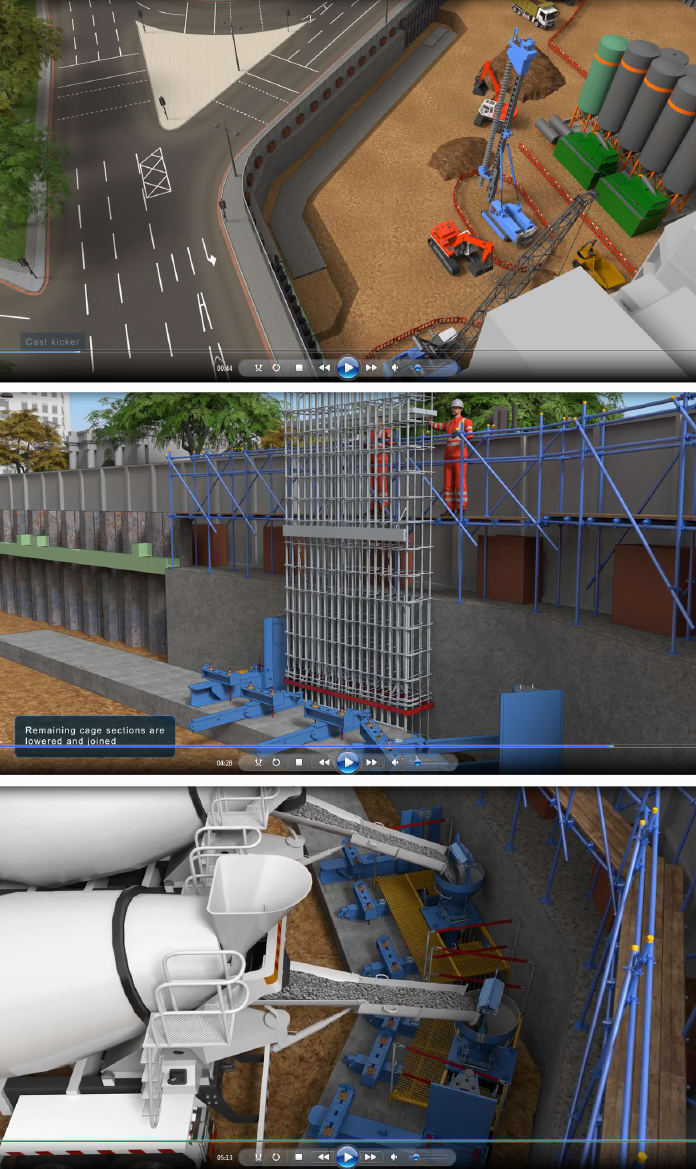
Balfour Beatty Ground Engineering uses 3D modelling to create detailed animations of work sequences on the most challenging foundation projects
Balfour Beatty Ground Engineering is expanding its 3D capabilities to create detailed animations of work sequences on the most challenging foundation projects. This enables teams to scrub back and forth in time through the programme of works, and proved critical when planning specialist temporary works for a 22m-deep basement at Marble Arch Place, a £400m mixed-use tower being built next to Hyde Park in London.
Diaphragm walls needed to support basement excavation are typically built between two “guide” walls positioned on either side. However, proximity to an existing structure meant a single guide wall could only be installed, so all the equipment needed to build the diaphragm – such as support works for the cage, tremies needed to gravity-feed concrete into the wall and supports for temporary access platforms for workers – had to be cantilevered from one side of the guide wall, instead of spanning between two guide walls.
Mark Pennington, technical director at Balfour Beatty Ground Engineering, says: “The animation enabled us to identify where issues or clashes might occur before the work commenced on site. Projects aren’t typically interested in animating groundworks construction because the structures are not easily visible, but this was a great communication tool for the guys doing the job and for the client.”
Cutting-edge sensors
As projects come out of the ground, cutting-edge sensor technologies are being deployed to monitor the integrity and strength of concrete foundations and other structures, with positive knock-on effects for the programme and the quality of the built asset.
Cementation Skanska has rolled out fibre optics for pile and wall integrity testing on a number of projects, with plans afoot to extend the method across its entire project portfolio.
CemOptics was developed in collaboration with the Cambridge Centre for Smart Infrastructure and Construction as a robust alternative to existing point sensing methods that require connection to numerous sensors.
Standard telecoms fibre optic cables are attached to the sides of reinforcement cages and temperature measurements obtained – based on recorded levels of backscattered light – at close spatial intervals along the cage. Measurements are taken at short time intervals to track the changing temperature during curing.
Cementation Skanska is deploying CemOptics during construction of stations and tunnels on the Northern Line extension in London. Over 50km of fibre optics was laid to build over 600m of deep basement diaphragm walls and 74 large-diameter bearing piles required for the new Battersea underground station.
The contractor is pushing the technology forward, using 3D printing to develop bespoke components to improve durability and simplify the installation process.
Andrew Bell, chief engineer for Cementation Skanska, says: “We see this technology as an essential part of our approach to improving safety and quality on our projects. Over the last 18 months, the system has delivered tangible safety, quality and technical benefits.”
An alternative foundation and pile integrity monitoring system, based on the use of wireless sensors embedded in concrete, is being trialled by Keltbray in collaboration with Arup and other partners. The firm claims that the technique is cheaper and easier to set up on site than fibre-optic technology and enables the follow-on trades to begin work more quickly.
The system is designed to accurately predict the in-situ curing strength of concrete after a period of just seven days, compared to around 28 days using conventional cube strength tests in a lab.
Stuart Norman, managing director of Keltbray Piling, explains: “There are challenges making the sensors and technology durable enough for the harsh conditions on site; they have to be able to withstand concrete in its liquid and solid forms, as well as the weight of 100-tonne piling rigs tracking over the top, you couldn’t have a more harsh environment. However, it’s rapidly developing and within three months I expect we will be there.”
Wireless monitoring data from sensors is also being exploited by projects to assess the impact of excavation sequences on ground conditions and structures and, based on that, modify the design as the work progresses.
“Technologies give us the ability to wirelessly collect data on things like movement in retaining structures, changes in groundwater pressure, heave at the base of excavations and propping loads – and bring it back into our software to validate design assumptions as work progresses,” says Paul Stewart, regional director at Aecom.
“The monitoring tech is always improving and giving us more data back, we can exploit it to help maintain the economy and safety of the design.”
Ongoing efforts to improve productivity and reduce downtime on ground engineering projects is driving advances in the design of new plant, machinery and related equipment.
The latest piling rigs, such as the Soilmec SR-75 hydraulic drilling rig, are able to engage an automatic mode to dismount from the low loader and quickly self-erect, including the mast, without human involvement.
Transmitting real-time data
The Bauer BG39 multipurpose drilling rig is able to function like a mobile wifi hotspot and transmit real-time data on aspects such as location, drilling conditions, or concrete production to service management systems.
Norman comments: “Some rigs enable us to see exactly what a driver sees and troubleshoot problems remotely from an office that may be hundreds of miles away. We are working on development of a client dashboard that would enable a client to view online, via a webcam in a cab, progress on site. It’s a more direct way to engage than having to wait for weekly progress meetings.”
Efforts to spearhead new approaches don’t end there. Balfour Beatty is assessing the viability of 360 vision cameras on vehicles that warn the driver when people or other vehicles come too close, to prevent accidents, and the use of augmented reality headsets to assess how to manage large pieces of plant inside constricted spaces like basement excavations.
Time will tell if these exciting emerging technologies become business as usual for groundworks projects of the future.

The drones captured high-resolution photos of the masts on piling rigs
Drone’s-eye view of piling progress
Balfour Beatty Ground Engineering is pioneering the use of drones for piling inspections.
Balfour Beatty Ground Engineering has successfully piloted the use of drones for plant inspections at the One Nine Elms project in Vauxhall, south London. The drones captured high-resolution photos of the masts on piling rigs and cranes as a quicker and safer alternative to manual inspections by human operatives.
Technical director Mark Pennington comments: “The existing method is to drop the mast and carry out a physical inspection, or get a cherry-picker to examine the machinery at height; it can take half to a full shift to complete, which costs us time. Our plant manager was initially sceptical about the use of drones, but as soon as he saw the images he was very impressed at the level of detail.”
The contractor is currently looking at how to embed the technology as part of its long-term preventative maintenance programme.
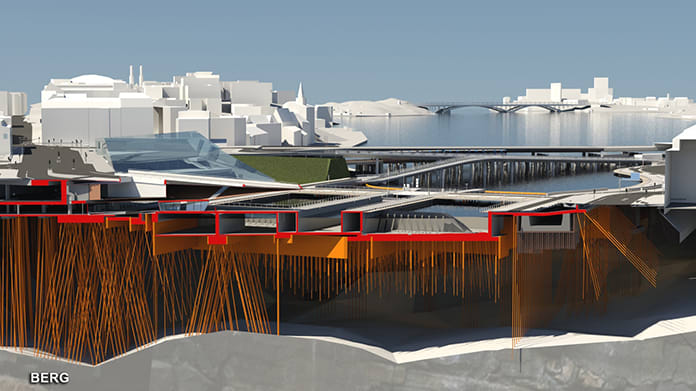
New Slussen’s foundations have been modelled in 3D BIM
Lock, Stockholm and one smoking BIM platform
An innovative cloud-based BIM platform is helping contractors plan and execute a massive piling operation to rebuild a lock complex in Stockholm.
The £1bn New Slussen project in Stockholm is one of the largest urban transformation projects in Europe. The existing locks, built in 1935 and now suffering from subsidence and damage, are being demolished and rebuilt to create a new civic quarter connecting the islands of Södermalm and Gamla Stan (the Old Town of Stockholm), with public areas, an accessible quayside, pedestrian and cycle routes.
The piling operation will consume around 20% of the overall construction budget and take until 2022 to complete. Some 3,600 steel piles, each unique in shape and costing around €20,000 each to produce, will be driven down 70m to reach solid bedrock on the seafloor.
The piles were modelled in the project’s 3D BIM environment with attached information on the specific pile number, location coordinates, orientation and length. This data was synced to the data management platform BIMeye, where the foundation contractor, Skanska, inputs extra piling information covering 80 separate parameters, needed by the design team, and 30 parameters for its own use.
Real-time access to information
As each batch of 50 piles is drilled and installed, Skanska feeds as-built data into the software on factors such as location, depth, the number of extra steel sections that had to be welded, and technical data on ground pressure.
The structural engineer on the project, ELU Konsult, checks against the data against the original design for any anomalies, and everything is synced back to the BIM models to give other users real-time access to the information.
Digital coordination of the foundations is an early success story in the project’s efforts to entirely eliminate the use of paper drawings. Johan Stribeck, BIM project manager for ELU, explains: “Having a single source of data in several locations, in BIMeye, in Revit models and in Navisworks, guarantees accuracy and removes the possibility of information gaps that can occur when information in paper drawings is sometimes not entered into spreadsheets.”