- Client: St George South London
- Lead Contractor: Brookfield Multiplex
- BIM Tools: Grasshopper, Rhino, Bentley AECOSim
New BIM-enabled parametric capabilities and tools not normally associated with BIM were required to design the sleek form of the One Blackfriars 50-storey tower on London’s South Bank.
Rising to 170 metres high, One Blackfriars will become one of the tallest residential buildings in Europe when it is completed in 2018, providing 274 luxury apartments. The multi-use development will also feature a boutique-style five-storey hotel, a two-storey mixed-use building with spa facilities and retail units and a new public plaza.
Architect SimpsonHaugh and Partners took on overall responsibility for the project’s BIM implementation, which was used for design coordination and development by a consultant team comprising the architect, structural engineer WSP, facade engineer Arup Façade, and building services engineer Hoare Lea.
“Design partners produced data rich 3D models in a range of different BIM authoring tools,” explains Dave Moyes, information management partner at SimpsonHaugh.
During the early design stages, SimpsonHaugh used a combination of Bentley AECOsim Building Designer and Generative Components to define the building’s complex shoulder-shaped form.
“We started out using the parametric tools inside Generative Components to describe the form of the building and respond to the site constraints. We knew we were going to move on to use AECOsim to generate document and area schedules etc, but there was no long-term vision to continue the development of a parametric model within a BIM workflow,” says Moyes.
However, that changed when SimpsonHaugh realised it would be working with Arup to explore alternative design options for the facade with an established and common toolkit to both. The team therefore switched to using Grasshopper, a graphical algorithm editor tightly integrated with Rhino’s 3D modeling tools, in combination with some clever and highly innovative custom scripting, developed in-house, to progress the design.
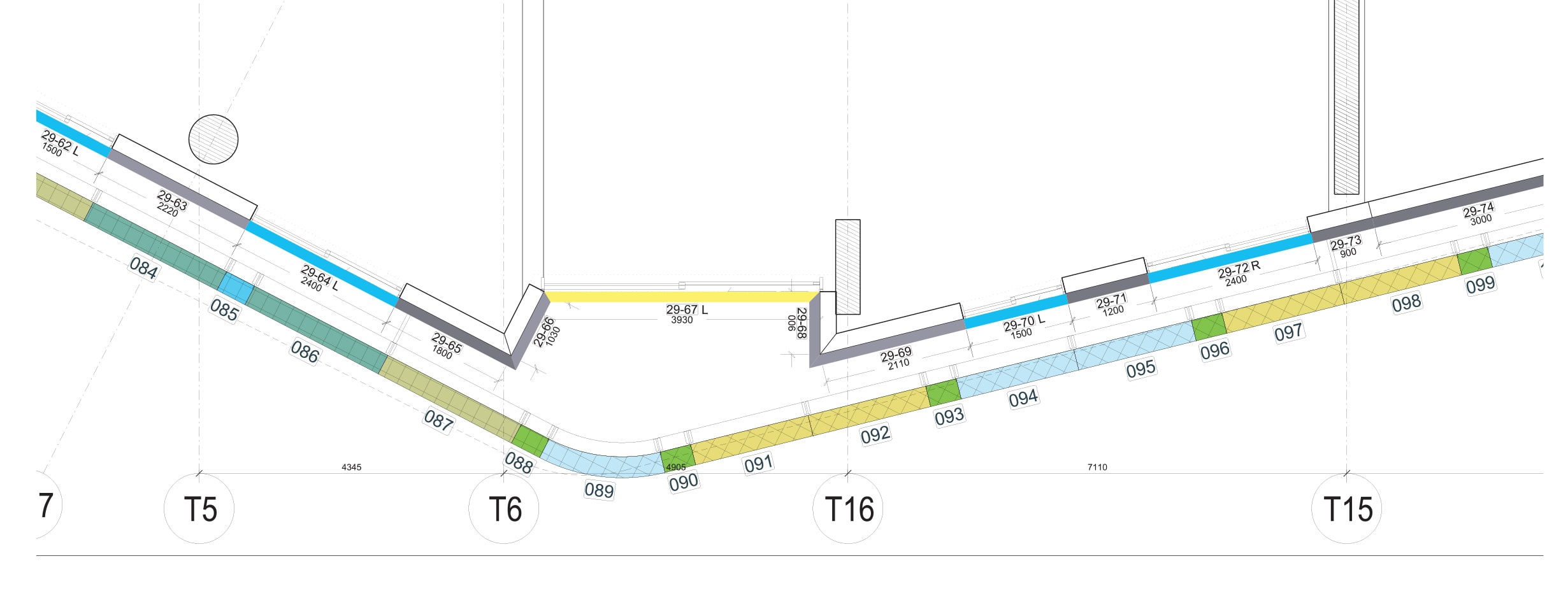
Zoom view of panel types
“This process gradually evolved until we were able to pull all the modelled information together in a central, federated parametric BIM model in Grasshopper,” says Moyes. “Grasshopper isn’t normally associated with BIM, partly because tagging elements inside Rhino to make them BIM intelligent is quite a long-winded process, but it is a really good tool to enable the BIM process with other tools such as AECOSim.”
The federated model was used to generate dimensioned and annotated drawings for the floor plates, other components, and design schedules. Federating the information was a complex process due to the use of a number of different software packages and file formats: WSP was using a combination of Autodesk Revit and Bentley Structural, and Hoare Lea was using a combination CAD Duct for AutoCAD and Revit.
“There was a lot of discussion, together with trial-and-error data exchanges between consultants to make sure we were inserting information in the right places and that only the correct model elements were being issued,” says Moyes.
Combining the packages proved highly useful in terms of design optimisation, for example, complex meshes designed in Rhino could be transformed in Grasshopper, in combination with custom scripting, into consistently sized and dimensioned elements ready for scheduling.
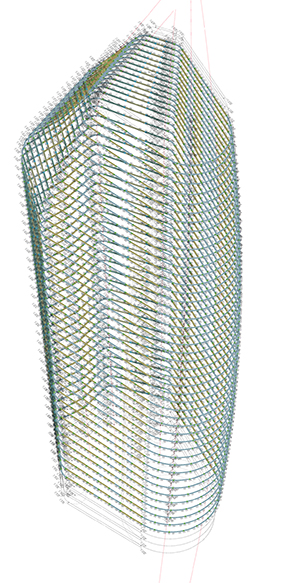
View of 3D model showing set out and types of outer & inner facade panels
“We were able to carry out a lot of design optimisation in Grasshopper that would normally have been more difficult, which resulted in a much better design solution,” explains Moyes. “The software enabled us to quickly see the impact of any changes on the design, for example, the building has smaller footplate than at the shoulder, the columns rake at different angles, which, when tweaked, affect room areas, the location of facade elements, rises and so on.”
He adds: “Using a BIM-enabled workflow made the whole design process much more tightly integrated. We also used the software to issue drawings when tendering the facade package to give suppliers a much better idea of what was required in terms of tolerances for glazing and structure.”
Arriving at an innovative solution was a challenge. SimpsonHaugh had just two team members running the parametric model and a larger team working in Bentley AECOsim. A continuous training programme was required to support their development during the project.
“We were very pragmatic in the way we approached it. If, for example, someone needed to complete door schedules in Bentley, we covered the base principles of using the software and what they needed to do to deliver that task. It wasn’t about being distracted by all the bells and whistles, but focusing on what needed to be delivered at specific times,” says Moyes.
Although BIM has not been taken forward beyond the design phase, it is still being applied in “unusual” ways, such as calculating and displaying the widest possible viewing angles in each apartment, to aid with sales and marketing to potential purchasers, a task that took a few days to complete within the parametric model and which may normally have taken weeks, if possible at all, in the conventional toolset.
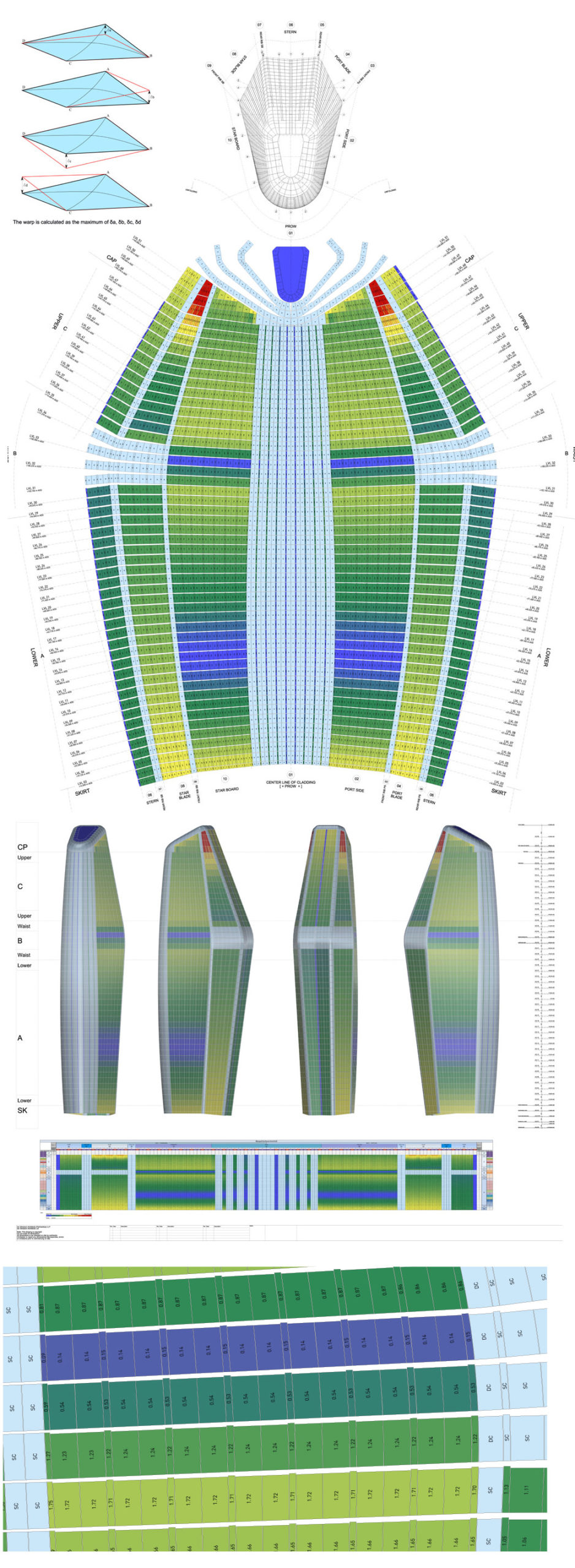
Model showing warped Surfaces
Grasshopper isn’t normally associated with BIM, partly because tagging elements inside Rhino to make them BIM intelligent is quite a long-winded process, but it is a really good tool to enable the BIM process with other tools such as AECOSim.– David Moyes, SimpsonHaugh
Comments
Comments are closed.
I am not entirely convinced they know exactly what BIM is.