In a breakthrough development, Foster + Partners has designed and manufactured a steel building truss at scale using 3D printing, delivering an industry first.
The project was a vital proof of concept for the Large-scale Additive Subtractive Integrated Modular Machine (LASIMM), a massive hybrid-manufacturing machine with metal additive and subtractive capabilities for parts up to 5m long.
In 2016, as part of a consortium of corporations, universities and research and technology organisations, Foster + Partners was awarded an EU grant to develop, build and test a LASIMM – a world-first for 3D printing in metal. Foster + Partners’ role within the consortium was to demonstrate the potential of the technology within the design and construction sector – alongside BAE Systems in the aerospace industry and Vestas in the energy sector.
In addition to the development and production of the machine itself, the practice was tasked with designing and producing a prototypical structural element that would benefit from – and be enhanced by – this new method of fabrication.
LASIMM is a step in the evolution of additive manufacturing in construction with steel. Additive manufacturing (3D printing) has been present in the manufacturing process for some time, but has yet to feature as a structural steel element in a building despite the extensive use of fabricated steel in construction. LASIMM incorporates digital design technology with the fabrication potential of 3D printing at a much greater scale and complexity, which could bring real gains to the manufacturing and construction industry.
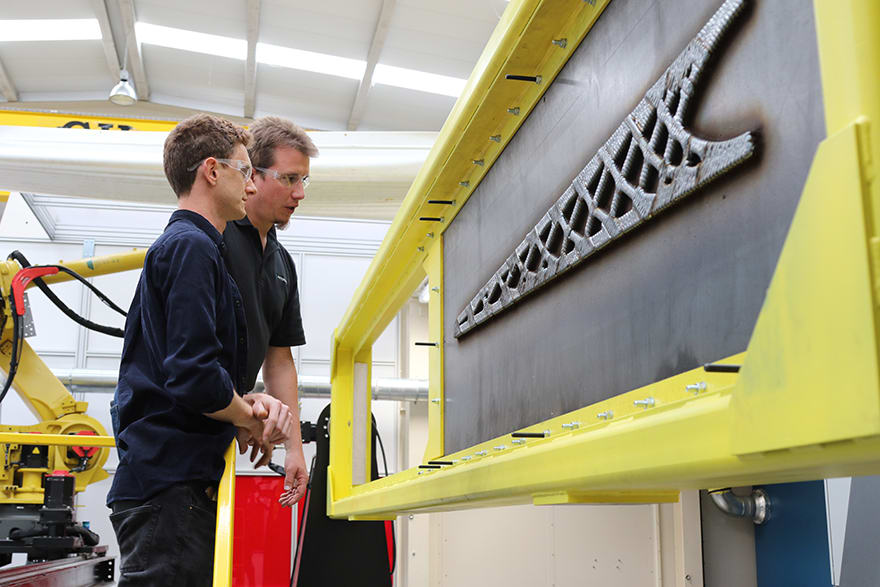
A major part of the collaborative project was the development of a novel composite machine
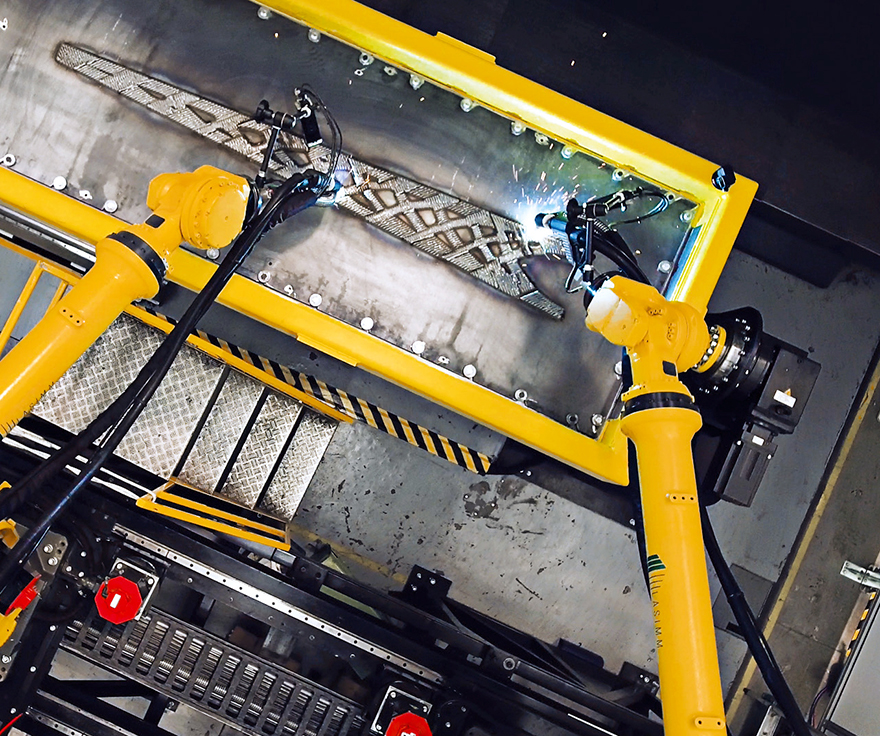
LASIMM is a step in the evolution of additive manufacturing in construction with steel
A major part of the collaborative project was the development of a novel composite machine, which was located in Pamplona, Spain, during the project. The machine is capable of rapidly depositing steel or aluminium into a rough approximation of the part (known as near-net pre-form shape) and then mill back the metal to the exact desired shape.
All of these processes take part in one hybrid machine, without movement of the printed element. The software to prepare the digital designs for manufacture, and to drive all the different aspects of the complex machine, was developed by Autodesk.
Foster + Partners’ objective was to produce a steel cantilevered beam that would showcase the potential of the technology for integration into a hypothetical future building. The team tested different beam sizes (from 2m-5m and options in between), which showed potential uses for different building scales.
The beam was a successful proof-of-concept, bringing into focus the challenges and opportunities for the construction sector. The medium-term objective is to apply LASIMM to a commercial project. Harnessing new technologies across industry is essential in the search for optimal structures – those that facilitate the building of meaningful, functional and sustainable architecture.
The LASIMM project is vital proof that 3D printing components on an architectural scale is possible and uncovered significant insights into the future direction and possible applications of the technology.