Skanska, working with a consortium of partners, has signed a collaboration agreement with Loughborough University to develop its lab-based concrete 3D printing technology to a commercially viable scale.
Skanska will be working with the team at Loughborough’s Innovative Manufacturing and Construction Research Centre (IMCRC), led by Dr Richard Buswell and Professor Simon Austin.
But to move the technology from lab to mainstream projects, it will also be working with precast specialist Buchan Concrete, ABB as an expert in robotics and control systems, Lafarge Tarmac and architect Foster + Partners to develop a 3D printing supply chain.
The IMCRC team has been working on 3D printing technology for construction since 2007, with a computer-controlled printer nozzle – which deposits a high-performance concrete by laying down successive layers – fitted to a gantry and a robotic arm.
The printer is now in its second generation and has produced two key prototypes: a bench, and a double-curved concrete cladding panel cast with voids and slots for post-tensioning.
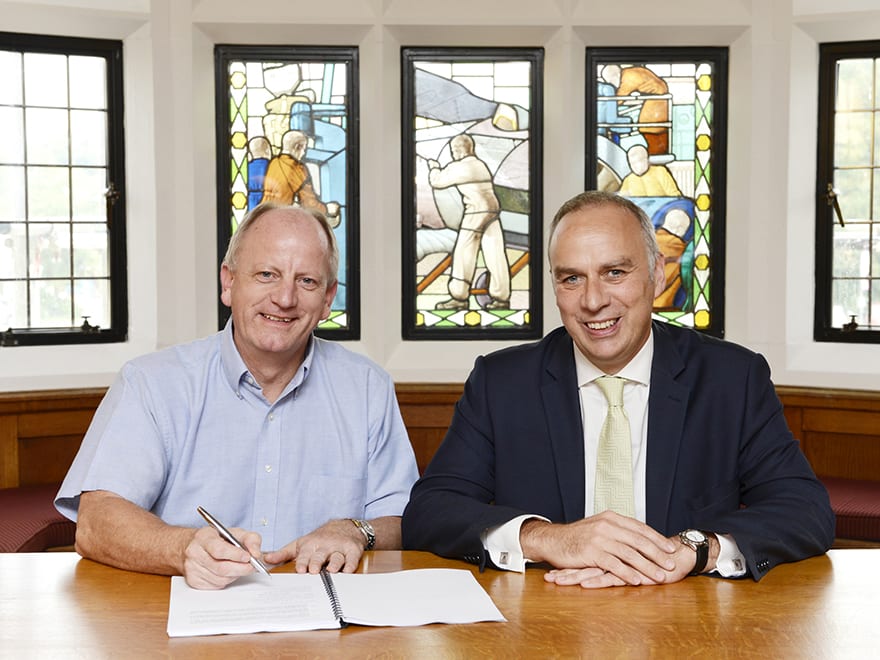
Skanska UK’s director of innovation and business improvement Rob Francis (left) signs the agreement with Loughborough University’s pro vice-chancellor (enterprise) Professor Steve Rothberg.
Dr Buswell told BIM+ that the IMCRC team had fielded multiple enquiries over the past five years from construction companies and designers about possible collaborations, but that Skanska had the best-developed vision for the new technology and the supply chain that would be needed.
“Construction is still craft-based and conservative, while this requires digital modelling, digital control and robotics – it does things differently and requires the design of the components to be different.
“So we don’t just need one partner, we need a whole bunch of skills, in materials and concrete batching, in robotics and component manufacturing.
“We have been constantly approached by people interested in what we were doing, some in fairly large organisations, but Skanska showed serious interest in the potential and took the approach of building a consortium of parties around the technology to develop a commercial version of our lab prototype.”
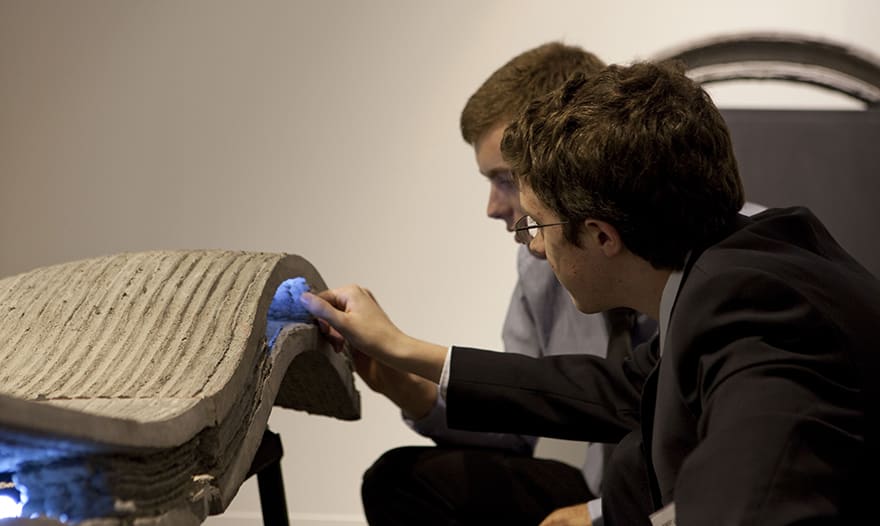
The printer has produced two key prototypes: a bench, and a double-curved concrete cladding panel cast with voids and slots for post-tensioning (above).
In a press release, Skanska said that the agreement put it in a good position to capitalise on an emerging technology with the potential to revolutionise the construction process.
Rob Francis, Skanska’s director of innovation and business improvement, said: “3D concrete printing, when combined with a type of mobile prefabrication centre, has the potential to reduce the time needed to create complex elements of buildings from weeks to hours. We expect to achieve a level of quality and efficiency which has never been seen before in construction.”
Dr Buswell told BIM+ that a concrete component produced using the team’s 3D printing technology could be utilised on a live project in as little as 12 to 18 months, but that a fully capable off-site, near-site on even on-site 3D printing system would take longer to develop.
“Cladding the next Gherkin is clearly some way down the line, but on smaller-scale exploratory stuff, like an architectural feature, we could run as fast as the industry wants to take it – perhaps a year.
“We’ll be exploring specific applications with the [Skanska] group – we’ve taken it as far as it can as an academic project, now we need that guidance from industry.”
Dr Buswell and Sam Stacey, head of innovation at Skanska, will be speaking at a conference on 3D printing and additive manufacturing on November 25-26
Cladding the next Gherkin is clearly some way down the line, but on smaller-scale exploratory stuff, like an architectural feature, we could run as fast as the industry wants to take it – perhaps a year.– Dr Richard Buswell, Loughborough University
Comments
Comments are closed.
Is there any reinforcement mixed with or woven into the concrete? Or post-tensioning is the only reinforcement?
I assume the team have considered printing glass fibre reinforcement from a separate jet into it. If you can get some tensile strength into it it must have a future as a cladding material, if not for structural uses.
Commercial use?
Not the first. The Chinese are already using 3D concrete printing in commercial use.