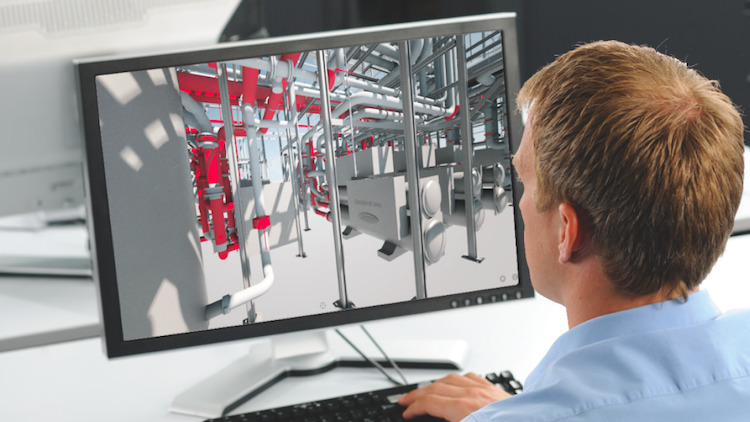
Construction tool manufacturer Hilti wants mechanical, electrical and plumbing (MEP) work to feature in BIM designs to avoid wastage, speed up work on site, reduce rework and improve the health and safety of workers.
Hilti notes that while BIM is often used to plan pipes, ducts and cables, many systems have yet to integrate MEP trades into the model.
To address this missed opportunity, Hilti is promoting its BIM Service, which runs from the design phase, through pre-fabrication, BIM-to-field modelling and the BIM-powered Jaibot to field-to-BIM for as-built documentation.
Following a virtual tour of Hilti’s BIM Experience Centre in Rotterdam, BIMplus grabbed 20 minutes to talk to Karl Johnson, technical marketing manager – BIM and MEP, for Hilti Region Northern Europe.
Why do you think MEP trades aren’t being considered enough in BIM?
It’s a legacy issue. In MEP, once you get down from the management contractor, you then have the sub-trades, and sub-sub-trades – and there are a lot of SMEs in that marketplace as well. Nobody’s ever really taken full responsibility for the full coordination.
On a lot of projects, you look up at the bracketry for the services, and quite often you’re faced with a forest of steel, because everyone’s looking after their own little package.
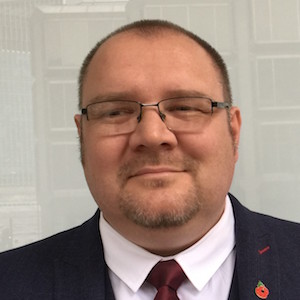
“You look up at the bracketry for the services, and quite often you’re faced with a forest of steel, because everyone’s looking after their own little package.”
If the main contractor takes responsibility for coordination, not only will you get a much smoother installation timeline, but you also see massive leaps in productivity because there’s less steelwork going up.
You also save on materials because the volume of steelwork required is reduced. We estimate savings of between 45% and 65% can be made on materials if you get everything onto common bracket arrangements.
It’s about main and management contractors taking ownership of that package of work.
Bracketry typically isn’t modelled, so [MEP subcontractors] are engineering on the fly. It also means the bracketry isn’t there when the model is handed over to the client for their asset management.
Also, when you control everything through the model, you can maintain and be strict on specifications, for instance that bracketry either side of the fire seal is at the appropriate distance.
This sounds like Hilti repositioning itself: is that proving a challenge for your customers?
There’s a bit of surprise at first with the shift of mindset from viewing us as manufacturer to being a design partner. We can help them start taking into consideration design of MEP bracketry, automating drilling for fastenings, fire stop design and planning. And there are additional tools we can offer, such as the validation of fire shields, documenting that through the construction process so they can be added to O&M manuals and such like.
How will Hilti spread its BIM message?
A top-down and bottom-up approach. Where we’ve already worked with a customer on BIM, we’re now being invited back onto projects at a much earlier stage, because they’ve seen the benefit of what we’re doing.
Proper planning of bracketry means less rework, and avoiding the considerable over-engineering of bracketry.
We can start reducing profile sizes, steel thickness, the number of supports, the amount of steel, etc. And if we pre-assemble the bracketry offsite, then there is no wastage, because what’s delivered is exactly what’s needed.
It’s all about early engagement and the planning.
From BIM to bot
A year ago Hilti North America launched an overhead drilling robot, named Jaibot, and it is now being promoted in the UK. It is cordless and can work for up to eight hours between charges and has a built-in dust removal system. The maximum height it can reach is 5 metres.
Jaibot takes its instructions straight from data that is uploaded to the Hilti cloud from Autocad or Revit and then marks and drills holes within its range autonomously – the location, hole depth and diameter are defined by the drilling plan, culminating in fewer errors, greater accuracy and cleaner holes, Hilti claims.
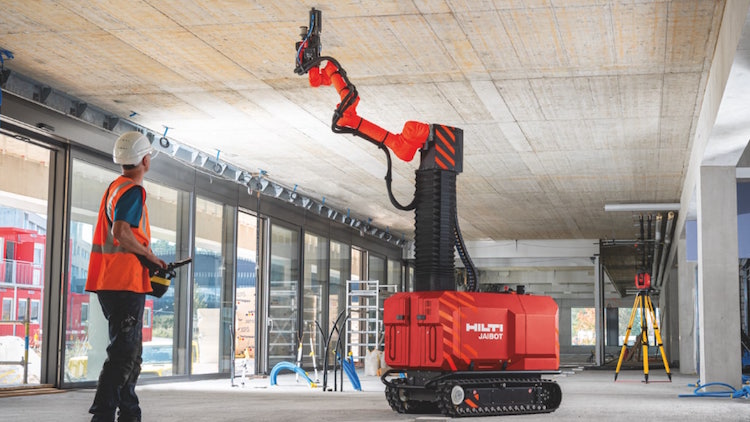
It takes four to six hours to recharge the robot.
A Jaibot is being used on a site in Denmark and it has achieved higher productivity than Hilti had hoped, drilling in the range of 650 holes in a day, Johnson says. It is estimated that a worker can drill 150 holes in a day.
The Jaibot has arrived in the UK. What can you tell us about that?
We’ve got our first one in our training centre in Manchester. Customers will be able to add a Jaibot to their fleet or lease from us.
We need to make sure we educate customers correctly first. The Jaibot not only has to be right for the customer, but also right for the job: it lends itself to some projects more than others.
Six staff will be trained on the Jaibot: three measuring specialists and three BIM project managers.
What will happen when a customer shows an interest in the Jaibot?
When a customer wants a demo of the Jaibot, we’ll invite them to Manchester, where it will be set up to demonstrate a couple of key applications.
Once a customer decides they want to use it on site, we would scope the job out, making sure the floor is clear, that there’s 4G signal, etc. We will need to establish the start and finish positions from the model into the bot’s software, plus the point cloud information for the fixing positions. And one of our measuring specialists would train the operator and stay in close contact all the way through.
What are your expectations for the Jaibot?
I hope we end up with lots of Jaibots in service, not only from the commercial point of view, but because of the added benefits: the fact that we can leave skilled people on construction sites to do skilled jobs; we can remove the risks of dust, Hand Arm Vibration Syndrome, working at height, etc; and get those skilled workers concentrating on the more clever technical aspects that require a bit more dexterity and opposable thumbs!