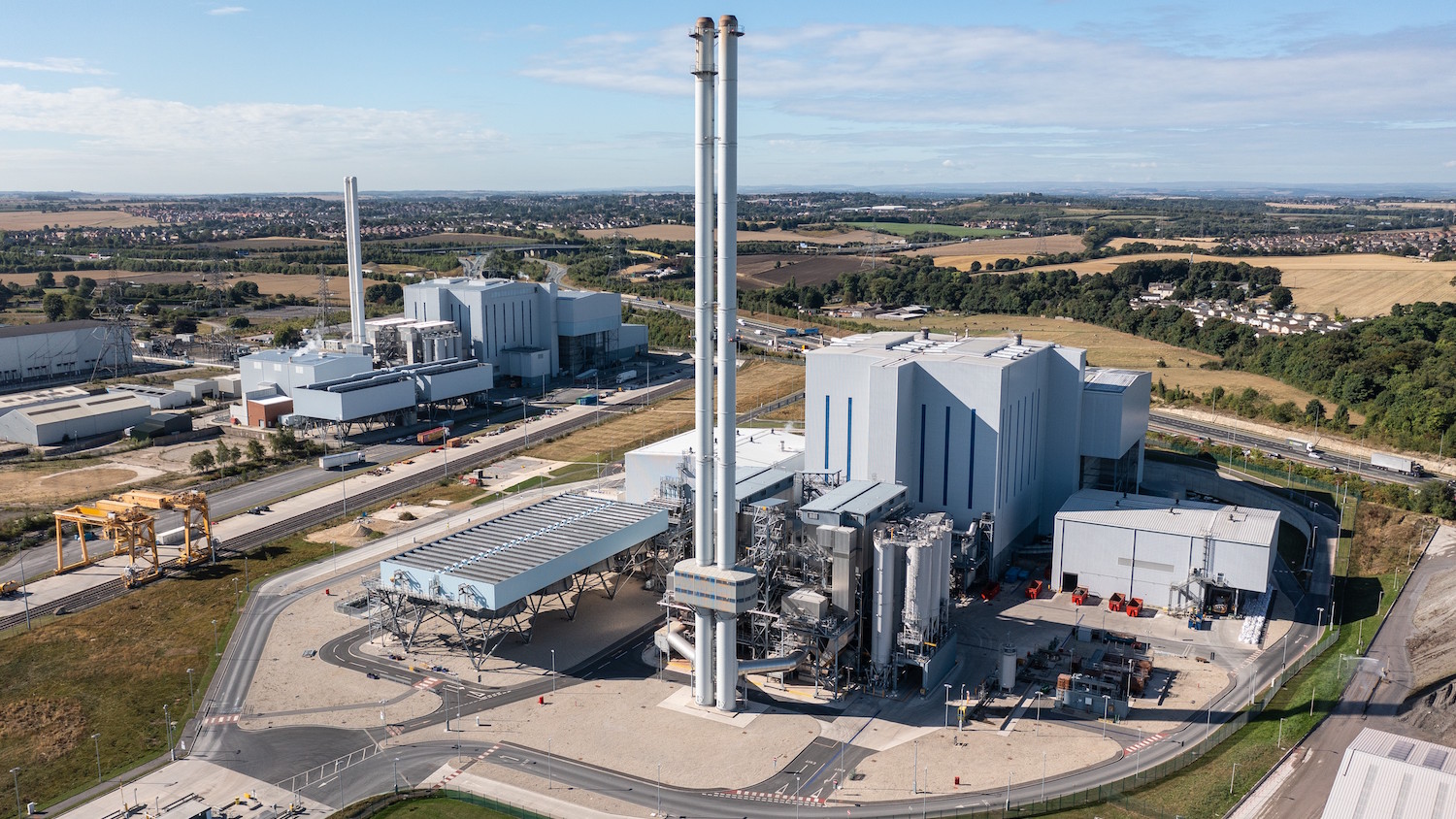
Energy-from-waste operator Enfinium has created digital twins of its facilities with the help of France-based 3D manufacturing visualisation specialist, Vertex Industrie.
Enfinium engineers now have access to interactive 3D information that is enhancing productivity, reducing unplanned downtime, and reducing costs. As an example of the latter, Enfinium claims the technology has achieved a 90% time-saving for typical maintenance checks compared with manual processes.
Initially covering the boiler, refractory and combustion grate elements of Enfinium’s generating units, the digital twins will be applied to cover other critical equipment at each of the firm’s four (soon to be six) UK facilities. The existing facilities are in Sittingbourne in Kent, Leeds and Knottingley in West Yorkshire, and Sandwell, West Midlands.
Using VR headsets, the experience is immersive, placing the wearer ‘inside’ Enfinium’s huge boilers. This helps the engineers to better understand their state and repair and maintenance needs.
Enhanced performance at Enfinium facilities is critical for ensuring it can provide reliable home-grown energy to 500,000 homes.
Transforming maintenance
Enfinium chief operating officer Jane Atkinson said: “There are immense opportunities for the energy-from-waste sector to deploy the very latest techniques in digitisation to improve reliability and enhance productivity. Taking the immense amounts of data that we have regarding our plants and creating a virtual, immersive digital twins have transformed the way we think about and plan maintenance.’’
Abder Rarmaoui, managing director at Vertex Industrie, added: “The predictive features of the Vertex platform allow efficient preparation of future maintenance. We are confident this will drive operational improvements as well as spur further innovation.”
Don’t miss out on BIM and digital construction news: sign up to receive the BIMplus newsletter.