The Digital Construction Awards attracted 165 entries this year, 84 of which have been shortlisted. Here, we detail the shortlisted entries for the Digital Contractor of the Year award, sponsored by Procore.
This category recognises the contractor – main contractor or specialist – that has demonstrated excellence and transformed their business through the adoption of digital methodologies and technologies. Six contractors made the shortlist.
BAM
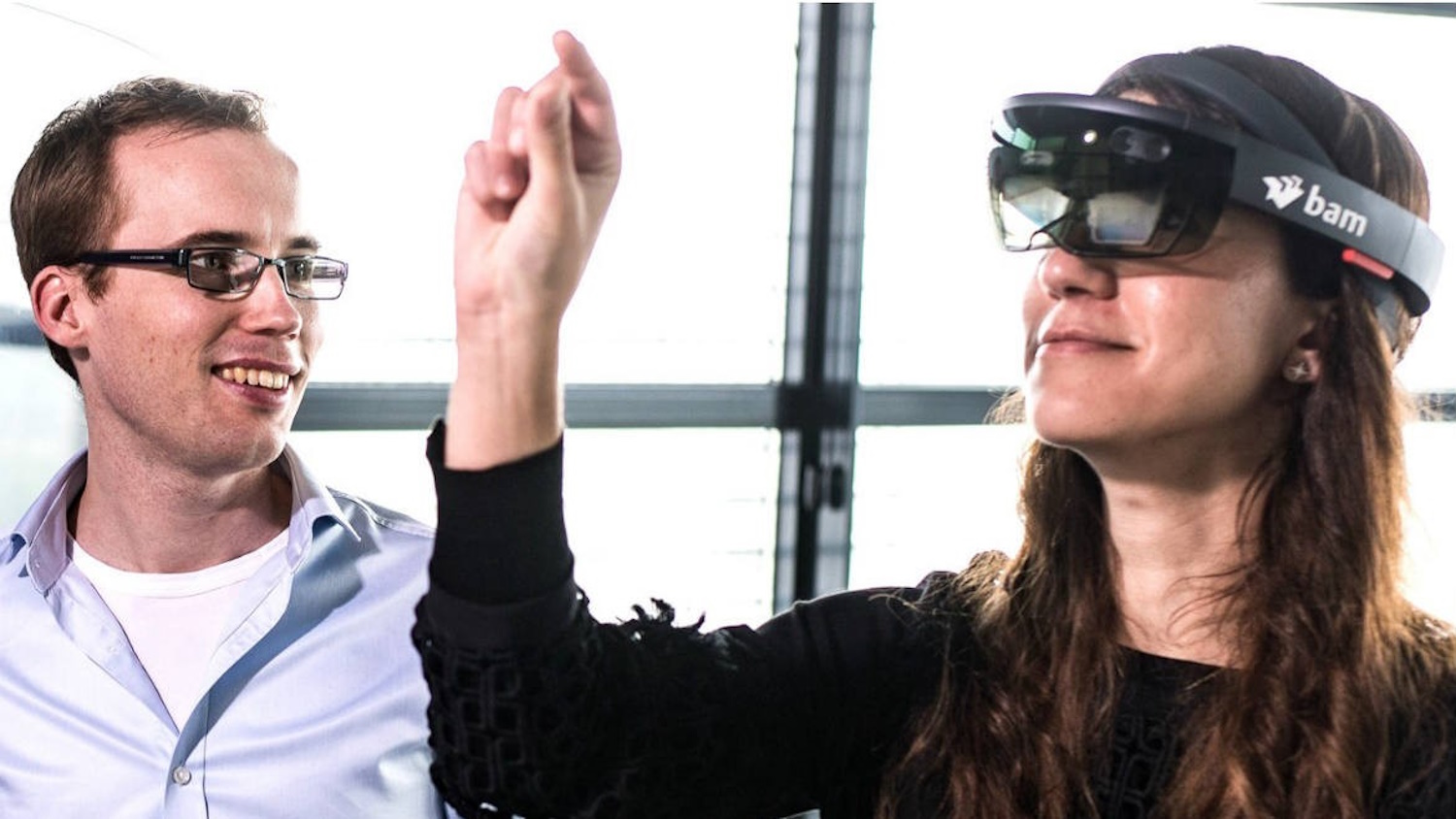
BAM recently brought together all its UK & Ireland businesses under a single operating model, a strategy called ‘Unleashing Potential’, with core enabling services delivered centrally. One of these services is digital, which the company recognised was critical to the success of its reorganisation, leading to the setting up of its Digital Project Solutions (DPS) team.
DPS aims to provide a holistic digital offering that harnesses the collective digital expertise of the entire BAM business. Digital was previously delivered by regional businesses, in isolation from each other with little or no collaboration.
DPS has created digital centres of excellence in four core areas:
- Information management and data analytics. Achievements include rolling out a business-wide common data environment capable of integrating SharePoint with Autodesk Construction Cloud.
- Project delivery and digital engineering. Provides high-end visualisation for BAM’s tendering team and live projects, with detailed simulations including VR to help project teams plan complex site activities, manage costs, logistics and engage with stakeholders.
- Advancing technology and innovation. Optimises existing technology and identifies new tools to help the business. BAM has secured Innovate UK funding in two separate AI initiatives worth more than £2m: one is developing a governance framework for responsible AI adoption; and the other uses AI to analyse site images against the planned programme of activities.
- Digital business partnering. Shares innovation across BAM’s business segments, delivering value to projects while also responding to their challenges.
To drive further value into the business, DPS has created digital competence centres to offer development opportunities and targeted training to around 100 people across BAM.
McLaren
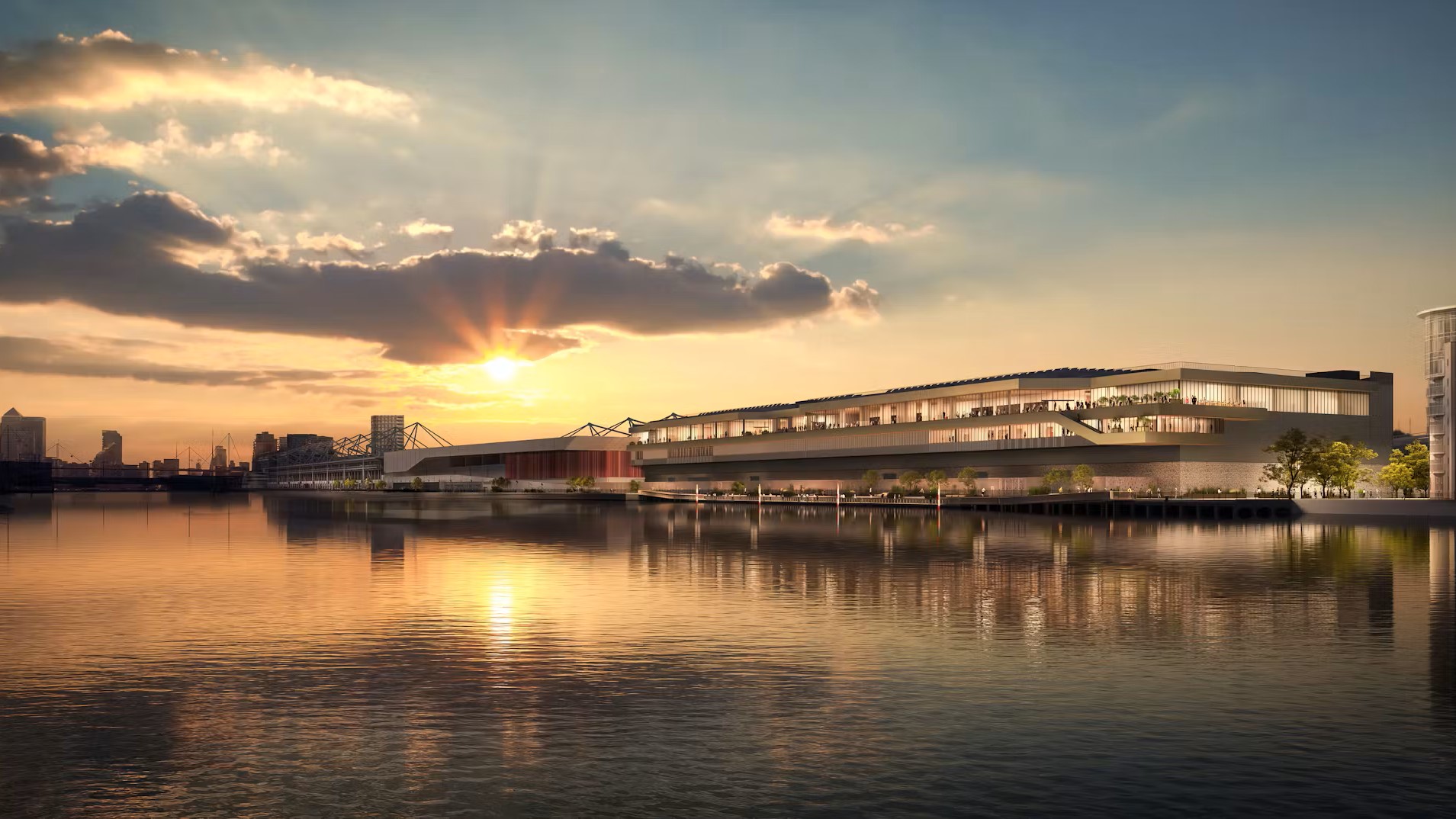
McLaren is forecasting to reach a £1bn turnover in 2024 and the firm has decided it must invest in digital functions comparable to established tier 1 contractors, while also meeting the challenges of building safety and sustainability.
The company is in the second year of a three-year digital transformation strategy, with a £4m budget. McLaren had previously relied on external consultants to support digital construction activities, but has created an in-house digital information management function to avoid siloing and promote a cultural shift.
The company has rationalised its software stack from around 10 applications to ensure a consistent approach, also saving £400,000 per year. Software currently used includes:
- Dalux, for field management;
- Solibri, for design coordination;
- after an independent review, McLaren reduced the Asite project templates in use (10-plus) to a single file now deployed across all projects and
- a bespoke sustainability dashboard combines data from SmartWaste, Biosite, One Click LCA and Social Value Portal.
One of McLaren’s exemplar digital projects is the £220m ExCel London expansion. Platforms used include Dalux, BIMcollab for issue management, Synchro for construction sequencing and Oculo for progress capture.
McLaren has developed its own approach to collating golden thread information on its projects. It has created a bespoke exchange information requirements (EIR) framework that sets out the evidence required to show Building Safety Act compliance. This is built into supply chain contracts.
McLaren’s digital capability is accredited to ISO 19650 and it believes its strategy will ensure compliance with the ISO 99001 standard for Built Environment Quality Management. McLaren’s sustainability performance score, assessed by Planet Mark, is up from 15/20 (2022) to 18/20 (2023).
McLaughlin & Harvey
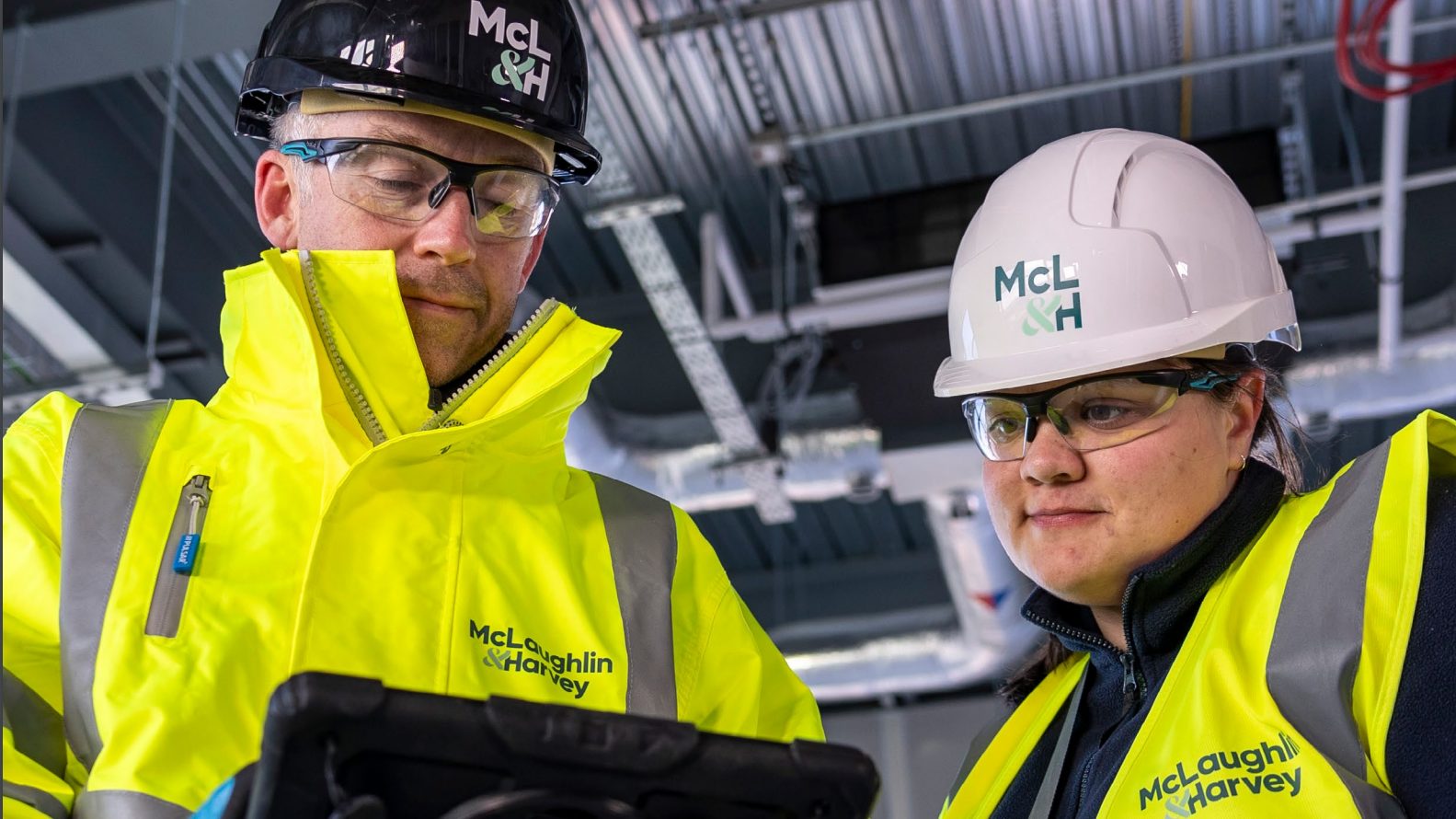
Belfast-headquartered McLaughlin & Harvey (M&H) has met the digital construction challenge by focusing on people, processes, and technology.
The contractor, which has a workforce of more than 800 and operates across the UK, has shifted towards managing all its projects digitally and has built up its in-house expertise, growing its digital team from a single manager to a ten-strong department.
It has prioritised clear information management, following the ISO 19650 standards and the Industry Foundation Classes (IFC) schema. This has transformed previously disjointed processes into a coherent and well-structured system.
M&H has made several judicious software procurement decisions to support its digital strategy, including:
- Viewpoint For Projects, to host its CDE process, which M&H configured to be compliant with BS EN ISO 19650;
- Solibri, to check and validate the information layer on M&H projects using IFC-SPF files;
- Trimble Connect Model Viewer, supporting the contractor’s objective for a model-centric approach to design and build, which enables models to be viewed simultaneously via any device, promoting collaborative work; and
- OpenSpace, ensuring uniform adoption of software and standardised data capture processes across all sites. It provides a comprehensive 360-degree photographic record of each week’s build.
The development of this in-house expertise has enabled M&H to assist its clients in specifying their requirements, and subsequently delivering and verifying those requirements using ISO 19650 compliant processes and appropriate technology.
Prioritising information management has improved project delivery, communication, transparency, and efficiency, boosting client satisfaction and trust in M&H’s capability.
Zed Pods

Zed Pods is an offsite modular housing contractor specialising in delivering social-rented homes with zero operational carbon emissions.
In partnership with Ashford Borough Council, which is targeting carbon neutrality by 2030, the company has designed and is currently constructing Fortis House: 23 energy-efficient, modular homes built above a steel podium on a council-owned public car park. This zero-carbon MMC-led project, built in a Flood Zone 3A area, is the council’s first scheme embracing digital construction.
Zed Pods has followed ISO 19650 to ensure consistency and accuracy throughout the design process, facilitate analysis of energy efficiency and ensure the golden thread of building information is maintained across all development phases.
Stand-out features of Zed Pods’ work includes:
- implementing a CDE using SharePoint and Autodesk Construction Cloud.
- unique IDs for information containers within the CDE based on an agreed convention that helps to identify and track specific information throughout the project;
- creation of a federated 3D BIM model through IFC using Revit, Revit-generated MEP models and Tekla Structures; and
- integrated with fabrication technologies such as computer numerical control machines in the factory to streamline the production of modular components.
The contractor is overcoming insufficient BIM knowledge among clients and subcontractors through continuous training and upskilling. It has developed a BIM execution plan template document as part of the EIR for Ashford Borough Council and is generating COBie schedules for the project.
Zed Pods says the scheme demonstrates how to unlock brownfield sites in flood zones for zero-carbon homes using digital construction methods. The project has secured grant funding of £1.8m from Homes England thanks to its environmental, offsite construction and socio-economic credentials.
PCE
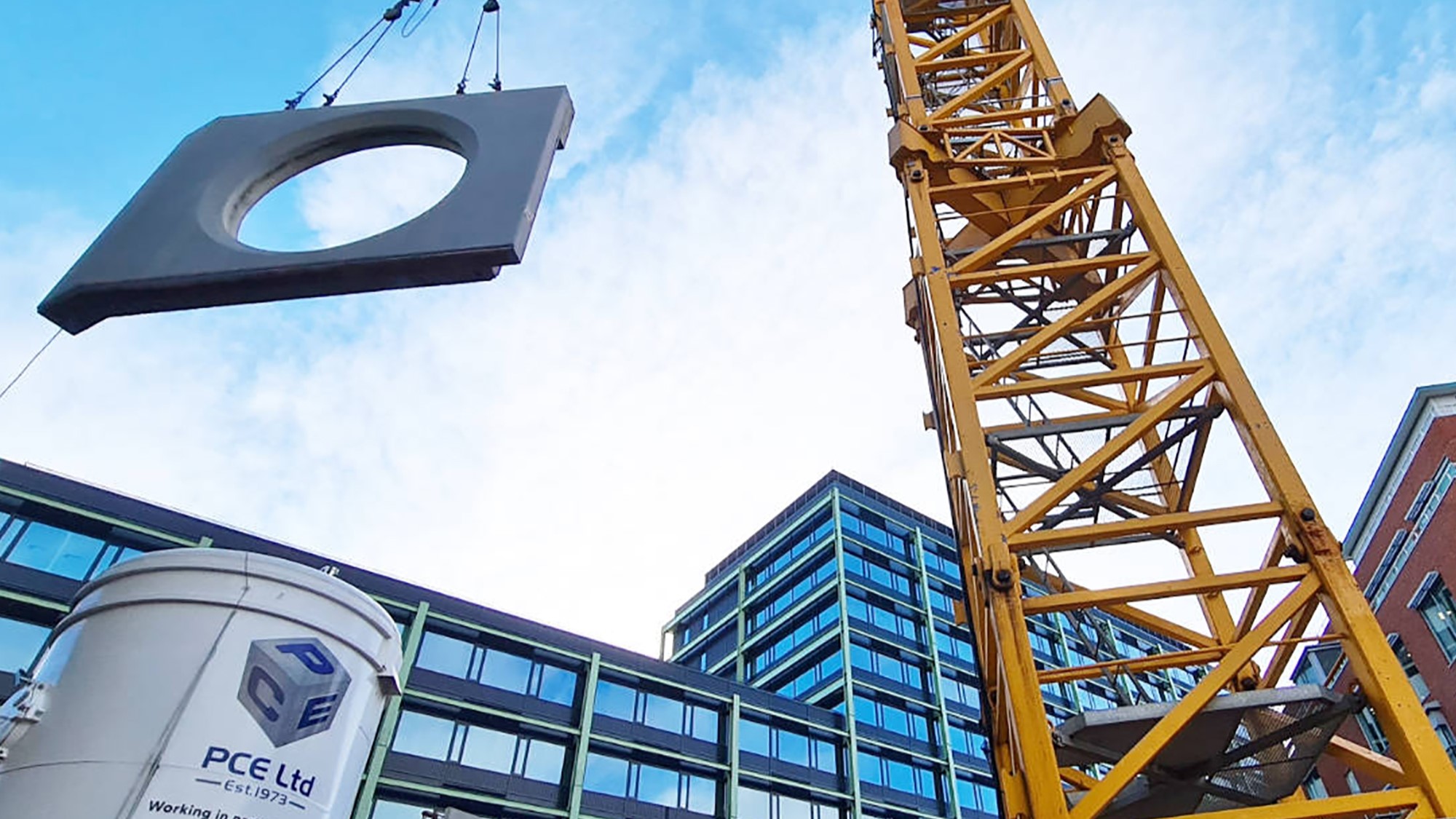
Specialist concrete contractor PCE uses digitally-driven design for manufacture and assembly (DfMA) to increase the speed and efficiency of its construction processes. The company’s HybriDfMA employs a systemised approach to offsite superstructure and façade design and construction, using standardised and repeatable kit of parts components.
PCE has recently sought to enhance its data capture, collation and analysis. With a CDE already established, the contractor sought to identify field-based data capture tools and tracking mechanisms capable of providing detailed visibility and golden thread compliance for every component.
PCE ultimately selected Ynomia following a trial project. Ynomia’s technology stack includes a web platform, a 3D digital twin, a mobile app, low-energy Bluetooth tracking tags, and gateways for automated, real-time tracking. The two companies have co-developed a real-time tracking and traceability system for PCE. With this system in place, PCE now boasts a comprehensive digital twin that visualises its entire design, manufacturing and assembly process in real-time.
Over the past year, PCE’s digital systems have successfully been implemented on projects totalling more than £700m in value, with more than 30,000 components tracked from more than 11 supply chain specialists across Europe. Its improved data function has ensured smooth logistical operation, early-error detection and resolution, quicker and more informed decision making, and continuous improvement for both PCE and its supply chain.
PCE is also exploring how it can use AI and machine learning for greater insight, for example, to monitor and observe concrete strength data to detect potential issues at the earliest stage.
SER Contractor
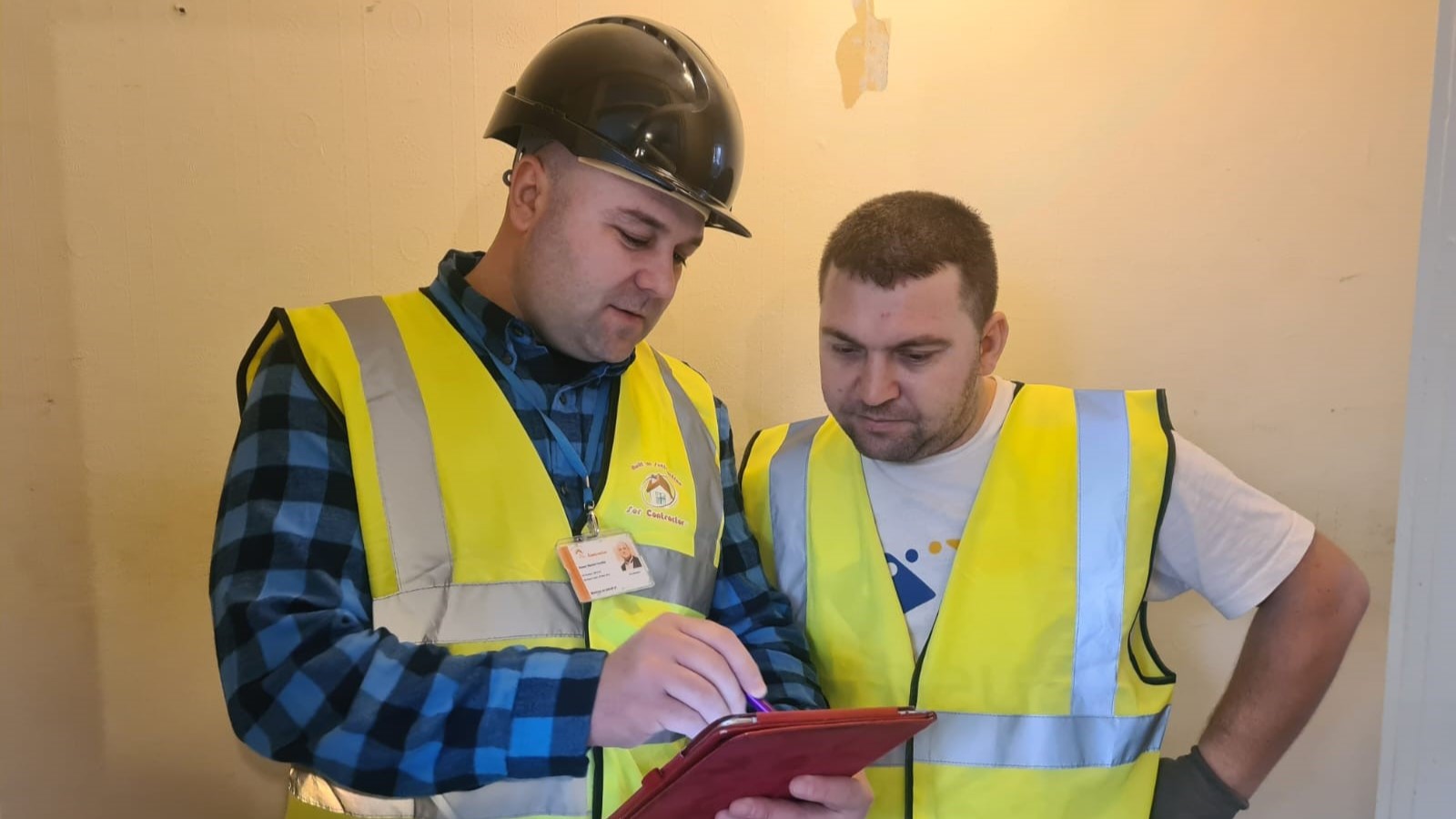
SER Contractor is a privately owned London-based SME contractor operating chiefly in the social housing sector. Its projects range from planned maintenance to high-rise schemes.
The company has enjoyed considerable growth recently, but struggled to find suitable software products for the different parts of the business, as none could cover all departments. Instead, the directors decided to build their own software product, working with external developers.
SER’s initial plan was to create a new communication tool. This evolved into the Abilo software, a cloud-based mobile application, which enabled real-time sharing of reports and photos across the company, eliminating the need for face-to-face meetings and reducing costs.
Additional operational and commercial functions were added, saving time, travel expenses, meeting facilities costs, overall expenses, and reducing the carbon footprint. Senior management site visits were reduced, along with in-person quality checks and audits, while productivity improved. Its integration with SER’s systems has resulted in a 20% reduction in overhead costs.
Abilo is now a comprehensive ERP solution, managing all construction operations within a single application.
SER says that while many software programmes in the market were IT-oriented, its app was developed based on the experience of a construction business, looking for IT solutions tailored to its own needs and those of its operatives, site managers, head office departments, clients, and other stakeholders.
The company’s transition from a £100,000-turnover subcontractor to a £28m turnover main contractor demonstrates the significant impact Abilo has had on the business.
Celebrate with the best
The winners of the Digital Contractor of the Year category, alongside the victors of the other 12 categories, will be revealed at the awards dinner on 2 July at the Brewery in London. You can join them by booking your places at the awards.
The Digital Construction Awards celebrate best practice and reward innovation in the application of information management and digital technology in the built environment sector.
The awards are run by Digital Construction Week, the Chartered Institute of Building (CIOB), and Construction Management and BIMplus. Awards sponsors include Bluebeam, Procore, Revizto and the CIOB.
Don’t miss out on BIM and digital construction news: sign up to receive the BIMplus newsletter.