The Digital Construction Awards attracted more than 140 entries this year, 62 of which have been shortlisted. Here, we detail the shortlisted entries for Digital Collaboration of the Year, sponsored by Bluebeam.
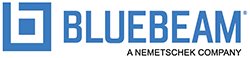
This category recognises the best use of digitalisation/digital methodologies and/or technologies to enhance collaboration between two or more organisations on a project, at any level of the supply chain.
Six entries made the shortlist, including those from Graham, Kier, Skanska and Laing O’Rourke.
Baird Family Hospital and ANCHOR Centre Aberdeen | Graham Construction with NHS Grampian

Graham Construction wanted to overcome the common challenge found in construction of siloed work among stakeholders collaborating on its project at the Aberdeen Baird Family Hospital and ANCHOR Centre. The £224m job is the largest combined project to be procured through the Health Facilities Scotland Framework.
Graham’s client, NHS Grampian, led the ambition for a more collaborative approach and set its goal to capture handover information in a clear and effective way where all stakeholders could get real-time updates on the project’s progress.
Graham adopted enhanced collaboration techniques during the early design phases, including common data environment training for NHS Grampian, visualisations of logistics planning, 3D walkthroughs and virtual reality to support engagement sessions. This ensured the building design was influenced by the end-users.
The teams at Graham also used Synchro 4D to link the BIM model with Asta to coordinate sequencing for key packages. They provided 4D simulations, visualising excavations, concrete pours and other construction activities before going on site, which offered tangible time savings. The 4D simulation was also linked to the Evercam system to track actual against planned progress.
Operational teams used BIM 360 Field to capture and manage quality information in real-time. The supply chain was given software training and equipped with technology. Insights were visualised through the PowerBI reporting system, allowing the hierarchy to track performance through Graham’s live reporting portal. This allowed the team to make quick, accurate decisions and ensure procedures were followed to deliver a quality asset that exceeded stakeholder standards.
Component tracking in complex supply chains: HMP Millsike | Kier with PCE, Ministry of Justice and Ynomia
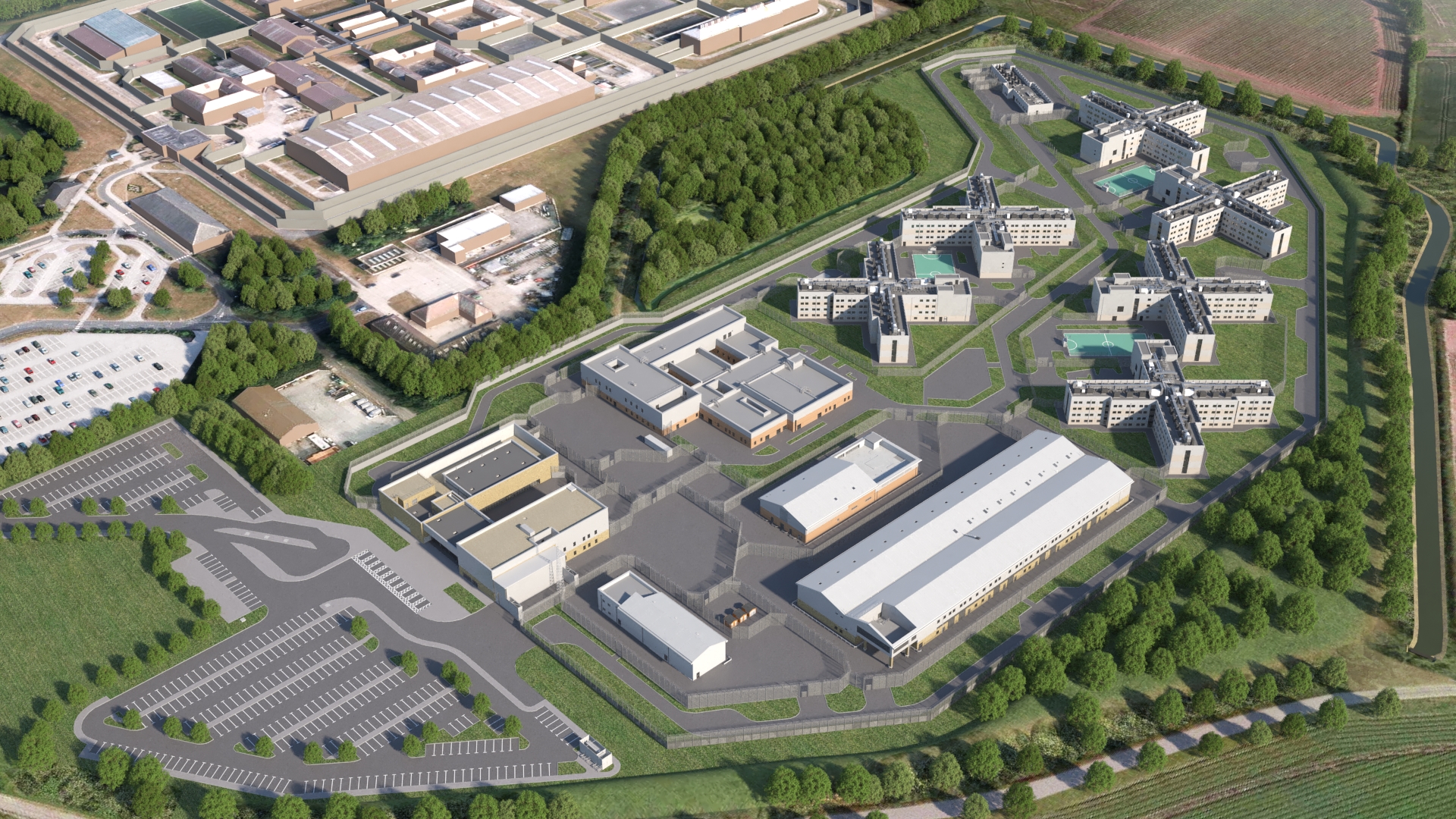
Kier was appointed as main contractor to build HMP Millsike, a £400m prison being constructed as part of the New Prisons Programme (NPP) for the Ministry of Justice (MoJ).
The new prison in East Yorkshire will feature 14,550 precast concrete units and around 90,000 subcomponents, which are being manufactured in nine factories across the UK and Ireland. The scale of this task meant that new technology was required for fast and accurate component tracking across the project, as well as to drive collaboration between the Kier, the MoJ and the supply chain.
The technology also needed to align with the NPP’s key drivers of quality, cost and programme, to help the MoJ meet increased demand for category C prison places.
Kier collaborated with the MoJ, its specialist subcontractor PCE and software company Ynomia to develop a bespoke solution to meet its collaboration goals.
The digital product developed, the Ynomia workflow for HMP Millsike, uses Bluetooth low-energy (BLE) tags on components moving past beacons to trigger milestones. It also makes direct links to data sources that Kier already uses, making it easy to integrate with the company’s existing systems. For example, Ynomia automatically monitors ViewPoint for design progression of components.
Combining these elements provides Kier and its partners with a 360-degree, ‘live’ perspective of each component’s journey: from design through to manufacture and installation on site, all visualised through a digital twin. Combining BLE and Kier’s existing software to track components in real-time, is allowing decisions to be made quickly and efficiently, creating time and cost savings.
Kidsgrove Station – managing risks from legacy mining | Arcadis and Esri UK with Galliford Try and Network Rail
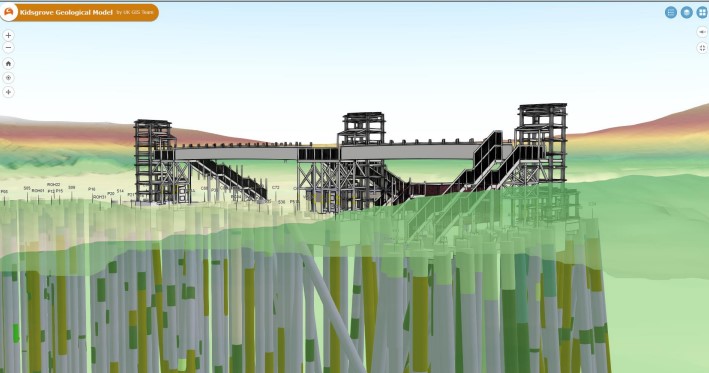
The Kidsgrove Station project for Network Rail created a completely new digital method of understanding and managing risks from substantial mining legacies coupled with project efficiency savings of around £1m, claims Arcadis.
The new methodology led to a digital twin, or 3D Mine Model, created using Esri UK’s GIS technology, which enabled the construction of a footbridge and lifts at the station, improving platform access for Arcadis’s clients, Network Rail and Galliford Try, while minimising disruption to Britain’s busiest mainline railway.
Network Rail identified the solution as an improved method and one to be used on future projects, supporting its proactive approach to mining legacy and avoidance of any operational impact.
Traditional methods of managing 3D data of this nature were not suitable for a project of this complexity. Arcadis brought the project’s digital twin to life by transforming data from OpenGround Cloud to Esri’s ArcGIS Pro using FME (workflow automation) and combining it with historic data, ground investigation data, grouting records, the BIM design, structural and sonar laser scanning survey data and other contextual data using automated workflows.
The resulting 3D Mine Model, shared via an Esri GIS web application, provided the project team with a data-rich environment that significantly boosted quality assurance, customer service, decision making and stakeholder engagement.
M42 Junction 6 improvement scheme | Skanska
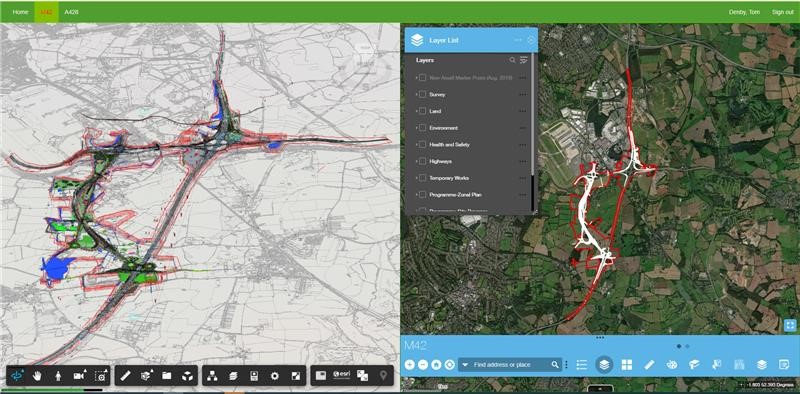
Skanska used a digital rehearsal process during its works at the M42 Junction 6 improvement scheme.
This involved deploying technologies such as Synchro, CostOS, OpenSpace, Esri GIS, Office 365 and BIM 360, among others, to provide an hour-by-hour visualisation to help deliver the installation of numerous bridges and road closures, including the weekend installation of new bridges, over the motorway.
Digital rehearsals eliminate traditional planning media, such as Gantt charts, that can be confusing or interpreted differently by different teams. This improvement in communication and understanding has reduced the likelihood of time errors occurring on site. The collaborative and interactive way of working has led to more diverse input, leading to tangible improvements, said Skanska.
Skanska’s planning team uses the 4D model direct from Synchro in collaboration with the engineers, supply chain and stakeholders to communicate, refine and validate the construction methodologies. Due to the project’s common data environment being fully integrated with Synchro Control, Skanska has been able to manage the Synchro file to ensure that the latest design information is fed into the 4D model.
Ultimately, the enhanced collaboration enabled by the 4D rehearsals generated 9.2 days of efficiency gain.
The approach also brought sustainability improvements. At the start of the detailed design phase, the scheme had surplus of earthworks of approximately 1,000,000m3. Through digital rehearsal it was found that the vertical limit of the new link road could be raised by 0.5m along the 2km length without having an impact on Birmingham Airport, one of the project stakeholders. This will retain 40,000 tonnes on site, rather than disposal, saving 95t of CO2e. The rehearsal also identified 20 areas outside the current footprint where the remainder of the surplus soils could be placed.
The People’s Project – New Everton Football Stadium | Laing O’Rourke with BDP and Solibri
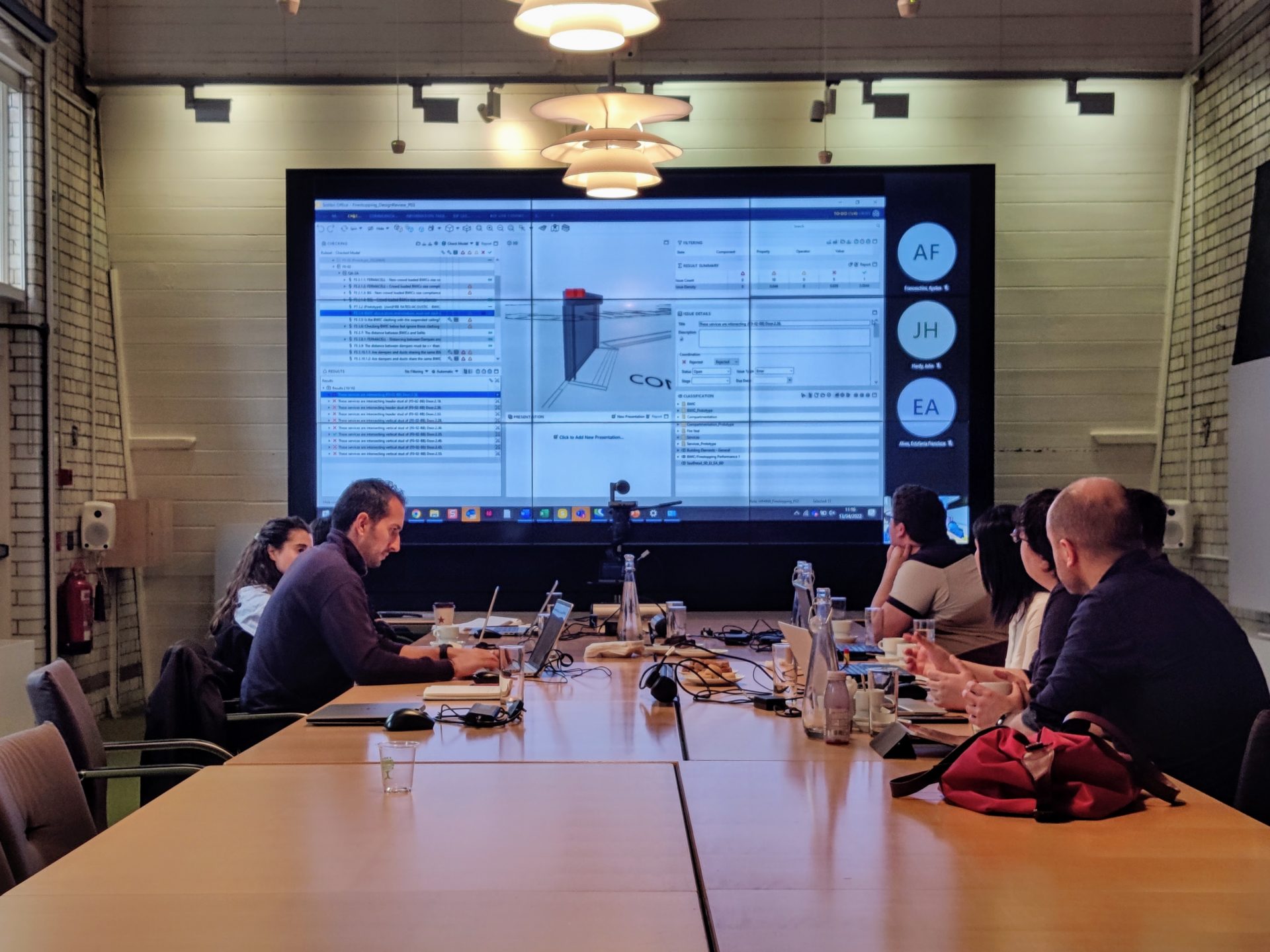
Everton FC’s new stadium has provided Laing O’Rourke and BDP with the opportunity to work with software provider Solibri to create an extension to existing technology (Solibri Office) that enhances fire safety. The three companies developed and implemented a digital solution that has brought together previously fragmented parties.
The application, Fire Stopping of Service Penetration Checks, has enhanced collaboration threefold:
- it unifies responsible parties (e.g., fire engineers, designers and installers) by requiring the latter to adhere to manufacturer specifications;
- it encourages ownership by reducing the level of resources required to implement a robust fire safety process; and
- it continually provides end-users with safety information that is 100% validated to help safely operate the building.
The new Everton FC stadium project team has used Solibri’s digital solution to capture outcomes from early collaboration in the design process and translate them into installation instructions that subcontractors must adhere to.
Laing O’Rourke, BDP and Solibri are now exploring whether they can continue developing the technology and its application to create a free, industry-wide database that contains system information, such as product capabilities and constraints. The companies believe that sharing this information has the potential to join the industry in working together with the common goal of making buildings safer.
Water for Life Hampshire | Mott MacDonald with Southern Water, Stantec, Aecom, WSP and Arcadis
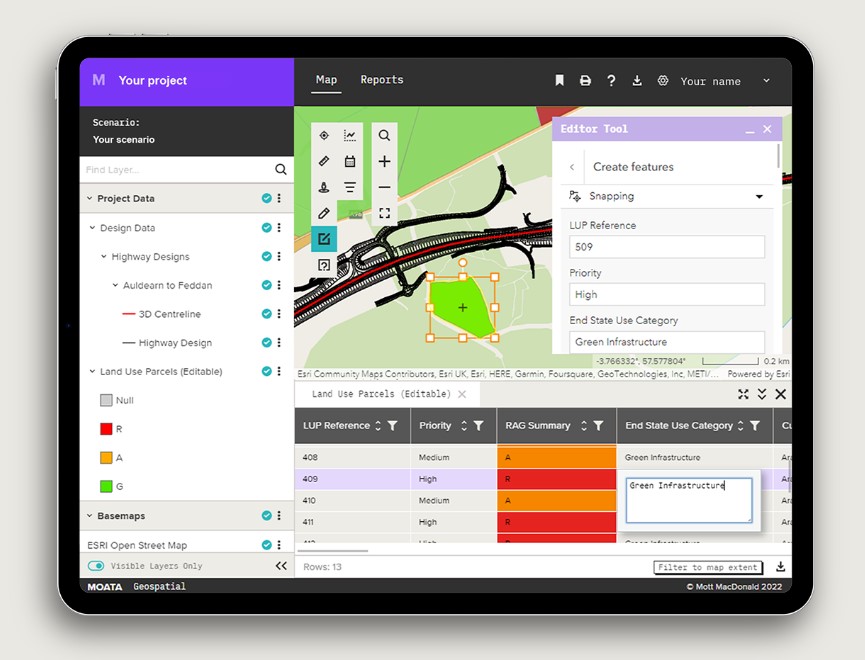
The Water for Life Hampshire programme is an ambitious project led by Southern Water, involving 66 partners from various fields. It requires a collaborative approach with a common data environment to share information in real-time to avoid possible delays and miscommunication.
One of the main challenges in the project was how to share all the licensed data and information about landowners with survey scheduling providers, keep records of communications between stakeholders across various teams and report on health and safety issues. Engineers and environmental assessment teams were also struggling to share their scheme design, environmental constraints and mitigation developments in real-time, as incompatible software is typically used between the disciplines.
Mott MacDonald brought together the domain and digital expertise of the company’s digital ventures and environmental services GIS teams to deliver a powerful solution for centralised collaboration throughout the whole project lifecycle.
The digital strategy for the project is focused on deploying MottMac’s Moata Geospatial and Moata Land Management solutions into the core of the project. Moata Geospatial provides a single source of truth for location-based data using its GIS mapping and reporting capabilities. This was complemented by a centralised system to manage field survey work and landowner communications through Moata Land Management, improving efficiency and reducing imminent risk of delays throughout the project.
Using Moata has led to quicker, more cost-effective designs, enhanced client satisfaction and reduced the whole-life costs of new pipeline assets.
Celebrate with the best
The winners of the Digital Construction Project of the Year category, alongside the victors of the other 11 categories, will be revealed at the awards dinner on 4 July at the Brewery in London.
You can join them by booking your places at the awards. There is an early bird discount for those who book tables before 5pm on 19 May.
The Digital Construction Awards celebrate best practice and reward innovation in the application of BIM and digital technology in the built environment sector.
The awards are run by Digital Construction Week, the Chartered Institute of Building, and Construction Management and BIMplus.
Awards sponsors include the Association for Project Safety, BIMcollab, Bluebeam, Everwarm, Graitec, nima, Procore, Revizto and Sir Robert McAlpine.
The post Digital Construction Awards 2023 shortlist: Digital Collaboration of the Year appeared first on Construction Management.