The Digital Construction Awards attracted more than 140 entries, 62 of which have been shortlisted. Here we detail the shortlist for the Digital Construction Project of the Year.
This category, sponsored by Revizto, celebrates what can be achieved through the successful implementation and adoption of digital technologies and processes on a project.
Six entries made the shortlist, including submissions from Sir Robert McAlpine, Mott MacDonald and Wates.
The digital journey from construction through to facilities management | Symetri with Stepnell and the University of Worcester
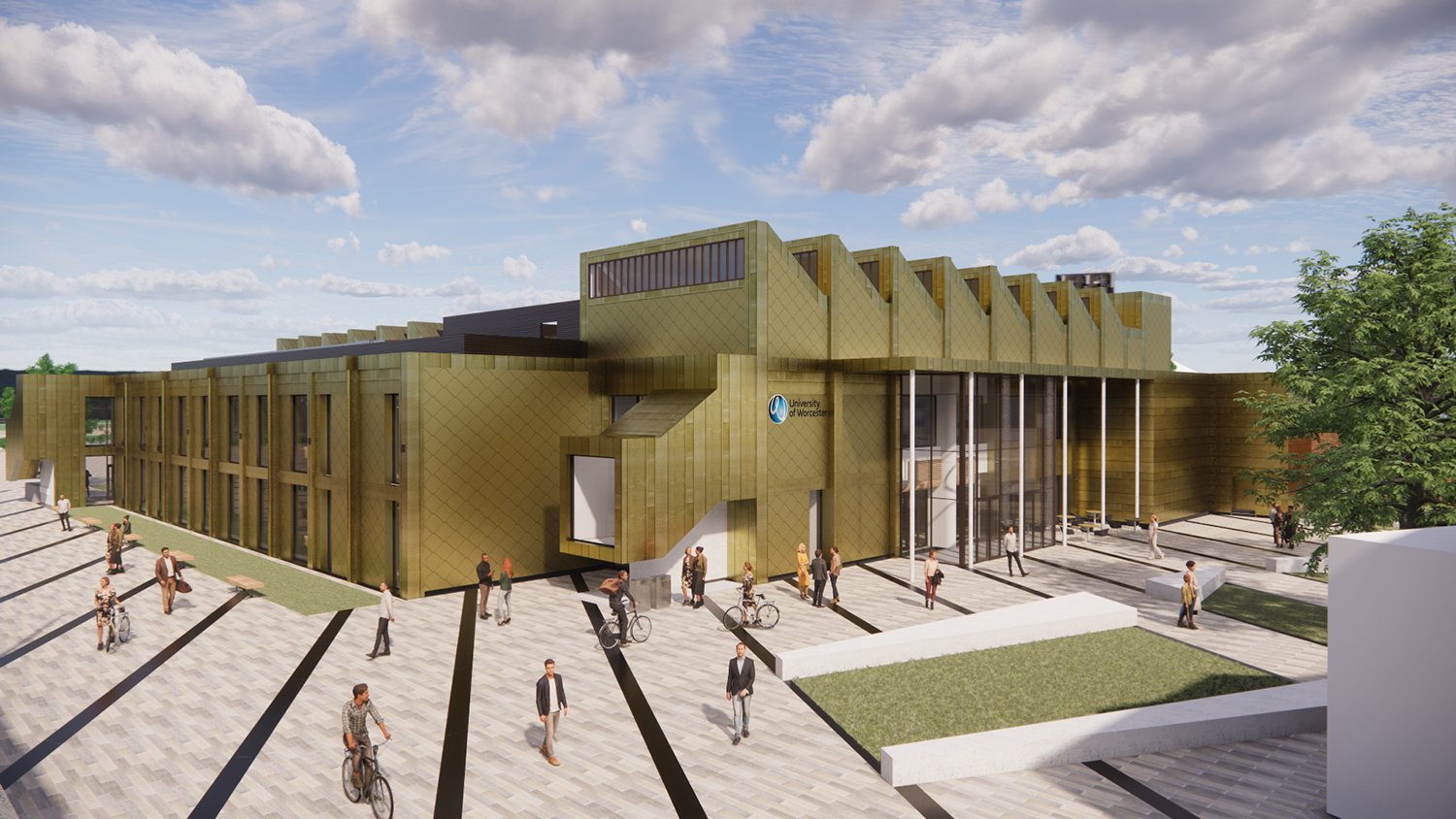
Stepnell worked with digital consultant Symetri on this visionary project which captured data during the build for the FM team’s asset management database.
The old Worcester News office is a 1965 building with an iconic sawtooth roof which the local university acquired with a plan to transform it into a centre for the education of healthcare professionals. The project involved stripping the two- and three-storey building back to shell and core.
The University of Worcester had a clear vision for BIM on the project. They were intent on using Revit 3D collaborative models and ensuring that all data relevant to FM could pass from the Revit model through to the soon-to-be-installed CAFM system, Archibus.
Stepnell and Symetri guided the University team through each of the essential BIM requirements, protocols and associated project planning, and created key documents such as the BIM Execution Plan. They also demonstrated how workflows would be integrated between the construction phase and FM.
During the refurbishment phase, Stepnell appointed 1st Horizons to laser scan the frame after the strip and brought the point cloud data together with the 3D model.
The format of the data – and compatibility with Archibus – was an important consideration, particularly for information such as the building code, warranty details, classification codes, and serial numbers. COBie is commonly used for these purposes, but because of the CAFM requirement, Symetri chose a bespoke structure for the data, using Solbri to ensure reliability and correct assignment of the data.
Conservation of Elizabeth Tower | Sir Robert McAlpine with UK Parliament Strategic Estates and Purcell Architects

Sir Robert McAlpine’s conservation work on the famous Elizabeth Tower has been one of London’s most high-profile construction projects of recent years – and it was underpinned by an incredibly complex and rigorous BIM strategy.
The five-year programme of work was the largest in the tower’s history and included repairing and redecorating the cast iron roof, clock faces and high-level metalwork, repairing stonework and a comprehensive systems overhaul.
The BIM strategy had two key objectives: creation of a reliable digital asset register with both new and existing building fabric elements, plus creation of an asset information model for FM purposes on completion.
Using drones and a point cloud survey, McAlpine’s team was able to build a detailed model of the tower and capture information about individual assets in the façade and roof.
There are 3,433 components in the roof, all unique, and due to their condition, it became clear that each one would have to be removed and taken off-site for restoration. McAlpine picked software provider Zutec to create a digital register to track assets as they moved through the construction process: removal, restoration off-site, then reinstallation. A dashboard collecting live data allowed the team to understand the works as they progressed.
The project required a complicated temporary works structure, with the whole tower cocooned in a 98m scaffold that took six months to erect. This was designed in 3D prior to its assembly using McAlpine’s in-house design team and their scaffolding supplier PHD Access.
On completion, McAlpine handed over the asset information models with COBie data, which cover the existing fabric and new maintainable assets. This will contribute to the eventual digital twin of the Palace of Westminster estate.
Park East | Buildots with Wates and Orbit Homes South
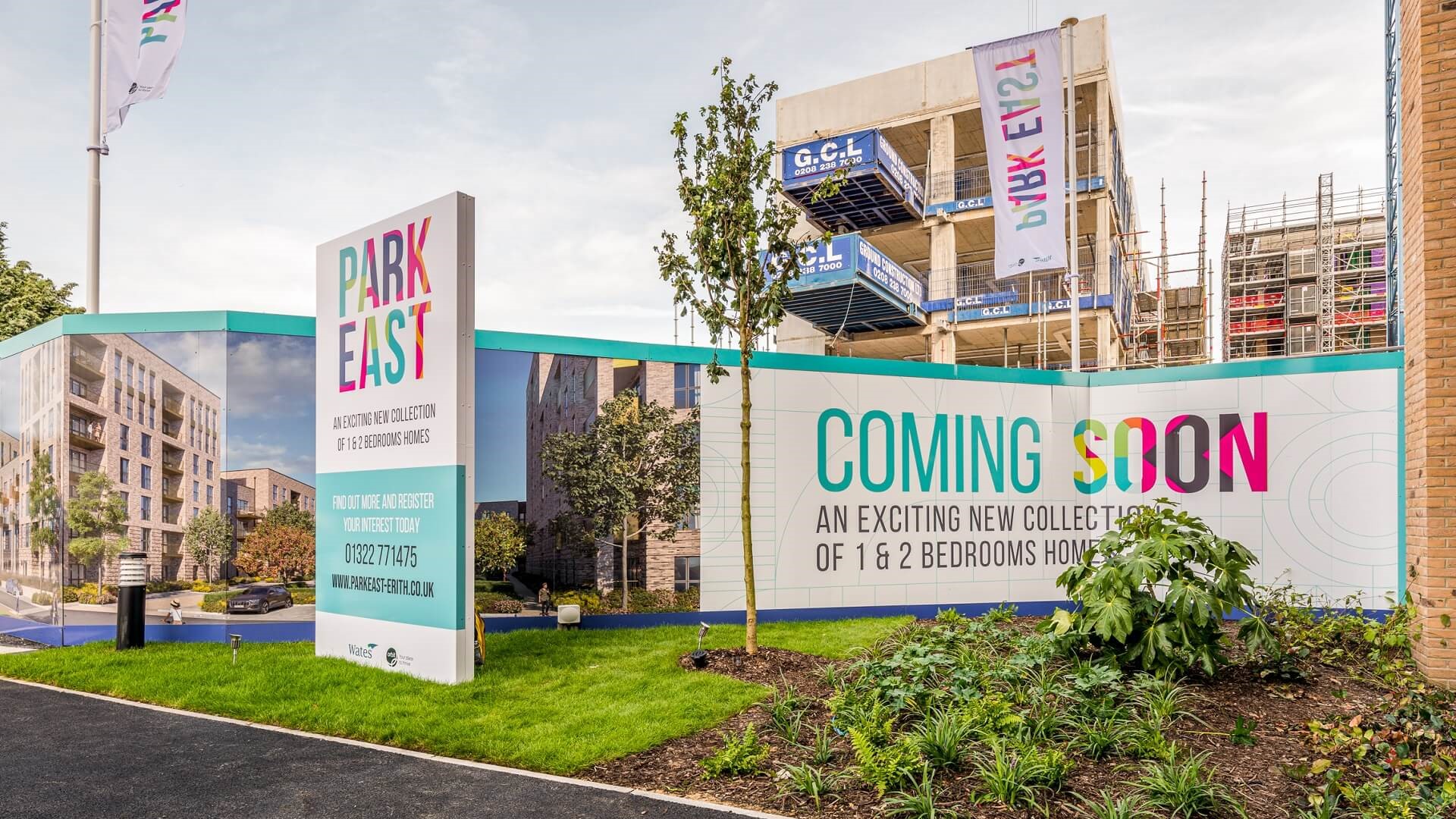
AI technology from Buildots helped Wates deliver this 320-unit residential scheme in south-east London, with considerable time and money savings across the project.
Wates wanted to avoid its project teams having to spend several hours a week walking the site and manually reviewing work completed, and then having to collate this information into reports. Buildots’ AI algorithms automatically validated images captured by hardhat-mounted 360° cameras, detecting any gaps between the original design, scheduling and the reality on site. The platform interprets the data it collects, allowing Wates to make informed decisions or take corrective actions.
Buildots also saved Wates considerable money in the fit-out. One of the contractor’s main pain points out is managing payments to subcontractors based on verified, completed work, which is often a subjective judgement. With the automated Buildots system, Wates could approve payments for works completed based on objective proof, as well as easily identify discrepancies between work quoted and completed. The contractor used Buildots’ stored captures to contest a claim from a subcontractor, using historic imagery to show the claim was worth less than 20% of their initial quote.
During the project, Buildots’ solution allowed Wates to automatically analyse the performance of 14 separate trades and track the progress of 154,000 elements across 17 buildings and 82 floors.
Chris Martin, head of planning at Wates Residential, said: “With the incoming Building Safety Act and ‘golden thread’ requirements, when you see what Buildots can do, this begs the question – can we afford not to use it?”
The IMA digital pods | IMA Architects
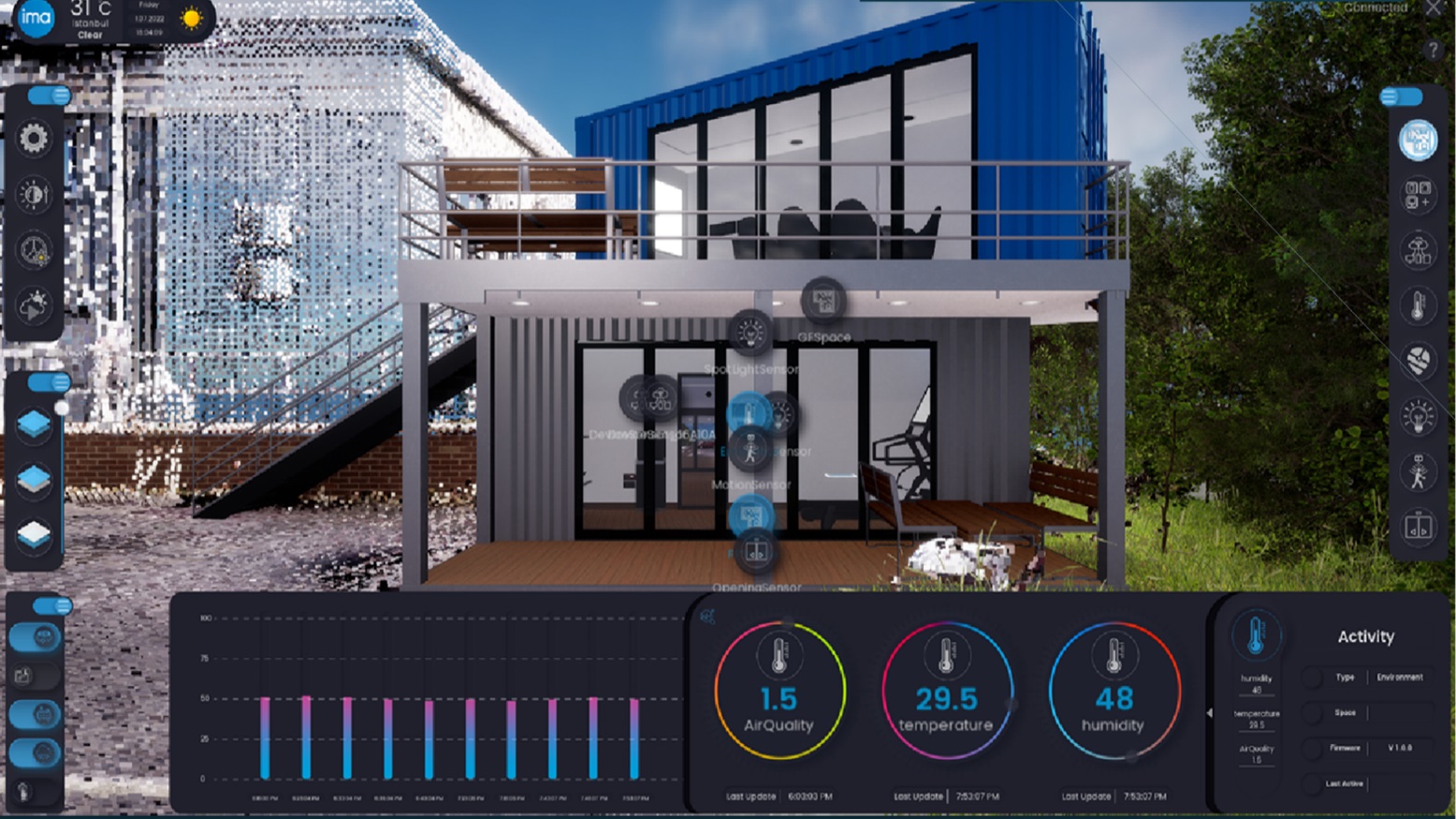
IMA Architects has created what it describes as “a UK first”: a working ‘digital twin’ prototype.
The team used its BIM expertise to develop the IMA Digital Pods, two former shipping containers which it transformed into a staff gym and coffee area within the grounds of IMA’s Leicestershire head office.
The pods have been equipped with a wide range of sensors in the physical building to create the digital twin. These include sensors which monitor environmental performance, light, power, motion, GPS, USB use and door closure. Internet of Things technology collects real-time data and feeds it back through a cloud platform into a 3D model, which has accurate information about the pods’ structure and assets installed within.
This data is then stored and analysed virtually within the model. The building owner or manager can access real-time data to show how even the slightest change could impact performance in the real world. IMA wanted the technology to be more user-friendly than traditional building management systems, so the user interface presents information in easy-to-understand graphics.
The practice reported a few challenges in the development of the software and in the physical construction of the building. Notably, due to the wiring requirements of the sensors, it had to interview several electrical contractors before finding one with the necessary skills required to complete the project.
Ultimately, IMA believes its technology will reduce the time and costs taken to build and manage buildings, potentially lowering construction costs by 33%, increasing delivery speed by 50% and cutting emissions by 50%.
Water for Life Hampshire | Mott MacDonald with Southern Water, Stantec, AECOM, WSP and Arcadis
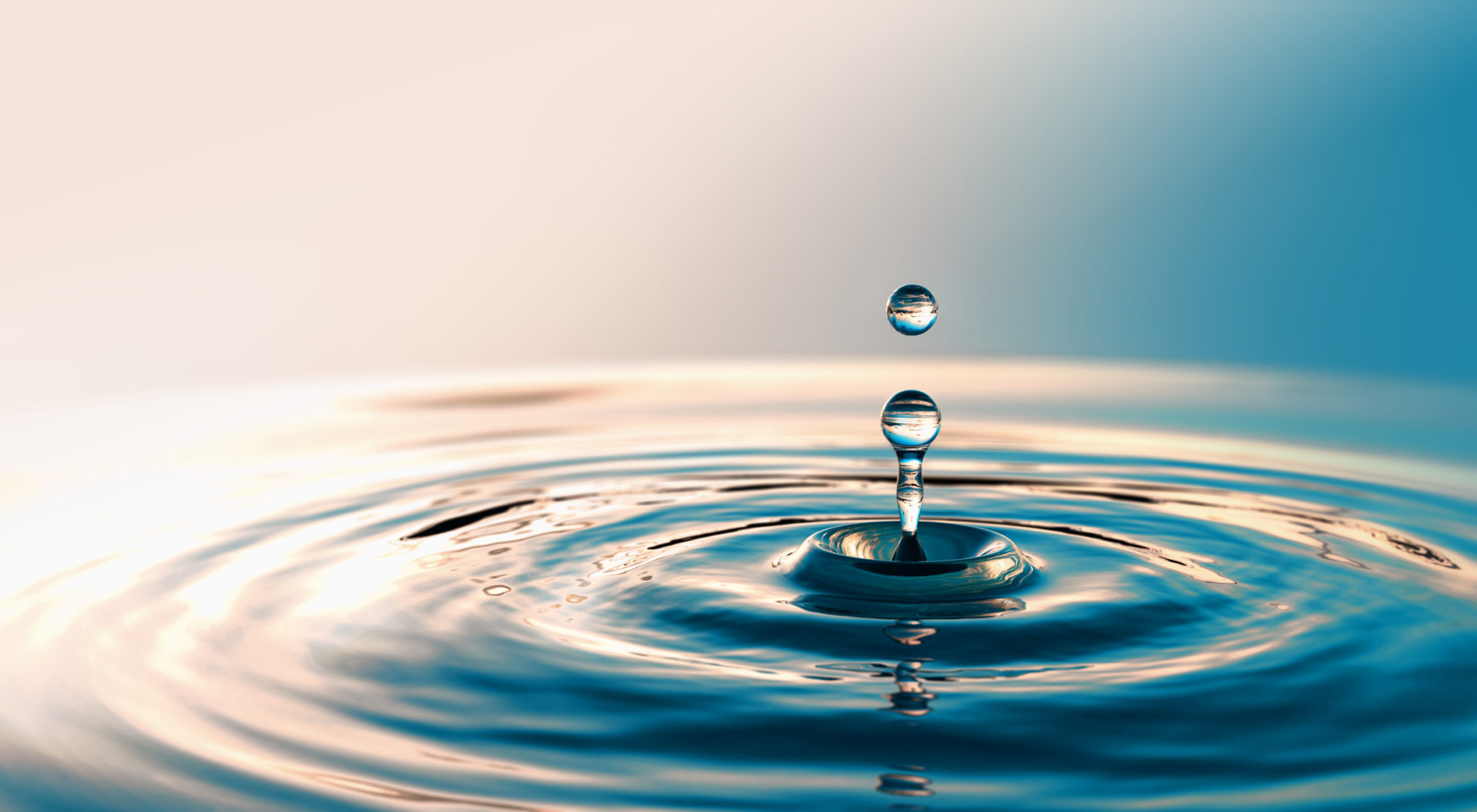
The Water for Life Hampshire programme is tasked with finding ways to increase water security in the Hampshire area, whilst protecting the environment.
Digital challenges included how to share licensed data and information about landowners, keep communications records and report on health and safety issues. Engineers and environmental assessment managers were struggling to share their scheme designs, environmental constraints and mitigation developments in real time due to incompatible software.
Mott MacDonald’s digital strategy for the project focused on deploying its Moata Geospatial and Moata Land Management tech solutions. Moata Geospatial provides a single source of truth for location-based data using its GIS mapping and reporting capabilities. This is complemented by a centralised system to manage field survey work and landowner communications through Moata Land Management.
The Moata solutions’ interconnectivity facilitates a seamless data flow and rapid access to trusted information at every stage of delivery, on the Water for Life project allowing 66 different teams to access all project information in a single space.
The survey management component recorded 7,604 survey visits, with 5,385 logged communications with 2,700 parties along the route, saving Southern Water over £250,000. Moata Geospatial tools were used 3,578 times by 458 users, spending only 48 minutes a day on average, saving 18,890 minutes.
With the GIS mapping software, environmental assessment teams were able to develop and share latest design schemes with engineers instantly. Surveyors were able to view the latest updates to the scheme design and schedule their surveys without delays.
As one user from Southern Water put it, “having a single source of truth on Water for Life has saved us dancing around 5-6 versions of design across multiple organisations”.
40 Leadenhall Street | Glider with Mace, Arcadis, Make Architects, M&G Real Estate, Nuveen
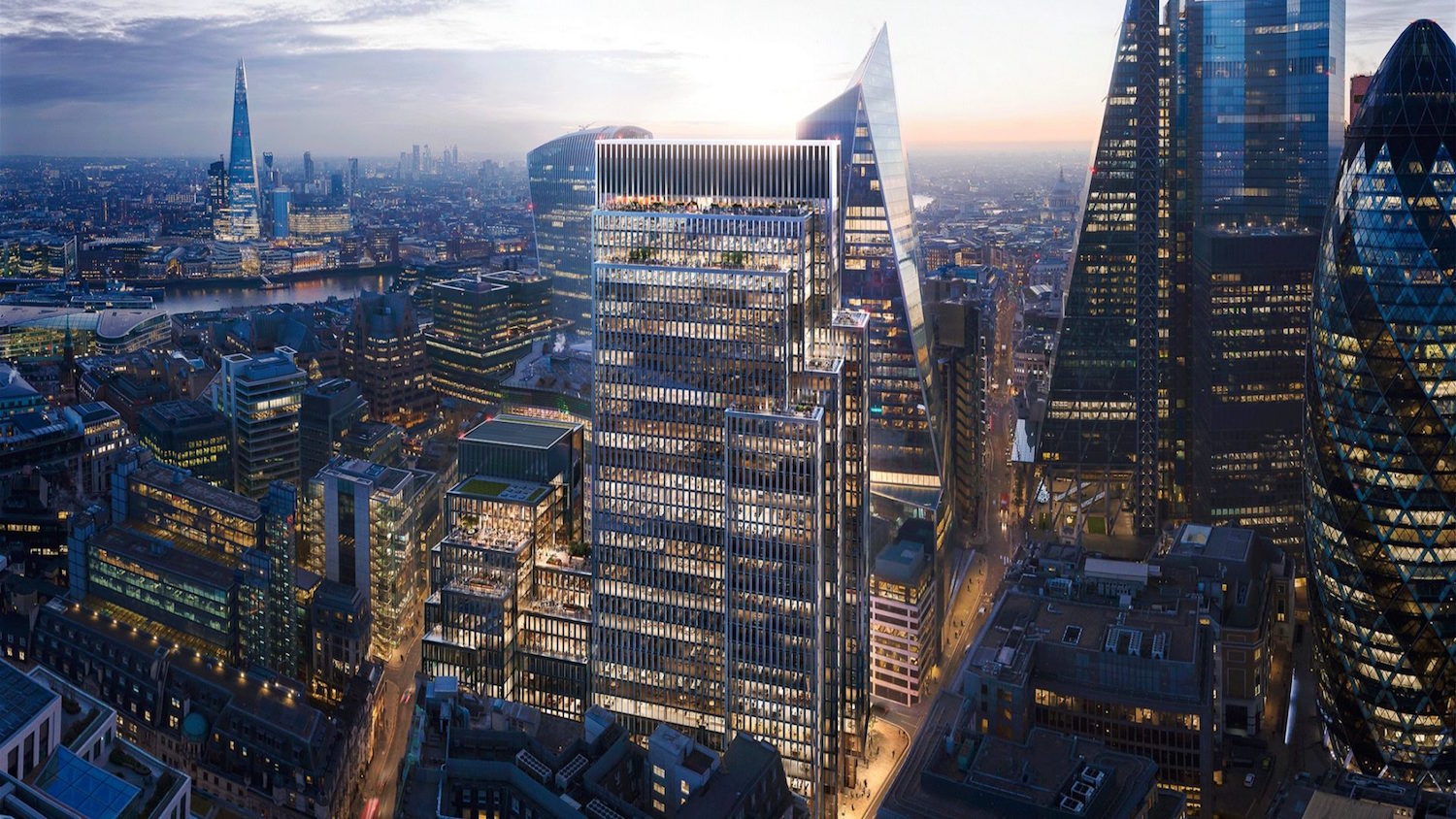
40 Leadenhall Street in the City of London is a vast and complex construction project, featuring two stepped towers, one 34 storeys and the other 14 storeys, which will create more than 87,000 sq m of office, retail and amenity space.
Main contractor Mace, which has employed prefabrication widely on the scheme, was keen to develop digital workflows to manage project data more effectively. With buy-in from the client, and to create a consistent and current database, Mace required all designers and trades to work with a federated model, using the Navisworks, IFC and Revit file formats. This meant a huge quantity of BIM information on Leadenhall, with some 60 trades on the project contributing to the models.
Due to covid-19’s operational impacts, Mace turned to BIM360 to maintain collaborative working across the project team, creating a digital ecosystem using additional programmes such as Disperse and Trimble Connect.
With an eye on the handover and operational phase, Mace appointed Glider as its asset information management and handover consultant. Although focused on asset management data, Glider connected its gliderbim® platform to Mace’s snagging detection and management in BIM360. Glider also worked alongside Arcadis as the smart building consultant.
The use of BIM on the 40 Leadenhall project has provided wide-ranging benefits and the CDE allowed for enhanced collaboration between construction teams, subcontractors and suppliers. The level of data handover should ensure a soft landing for operations teams responsible for running the building, as well as quicker onboarding for the FM team.
Celebrate with the best
The winners of the Digital Construction Project of the Year category, alongside the victors of the other 11 categories, will be revealed at the awards dinner on 4 July at the Brewery in London.
You can join them by booking your places at the awards.
The Digital Construction Awards celebrate best practice and reward innovation in the application of BIM and digital technology in the built environment sector.
The awards are run by Digital Construction Week, the Chartered Institute of Building, and Construction Management and BIMplus.
Awards sponsors include the Association for Project Safety, BIMcollab, Bluebeam, Everwarm, Graitec, nima, Procore, Revizto and Sir Robert McAlpine.
The post Digital Construction Awards 2023 shortlist: Project of the Year appeared first on Construction Management.