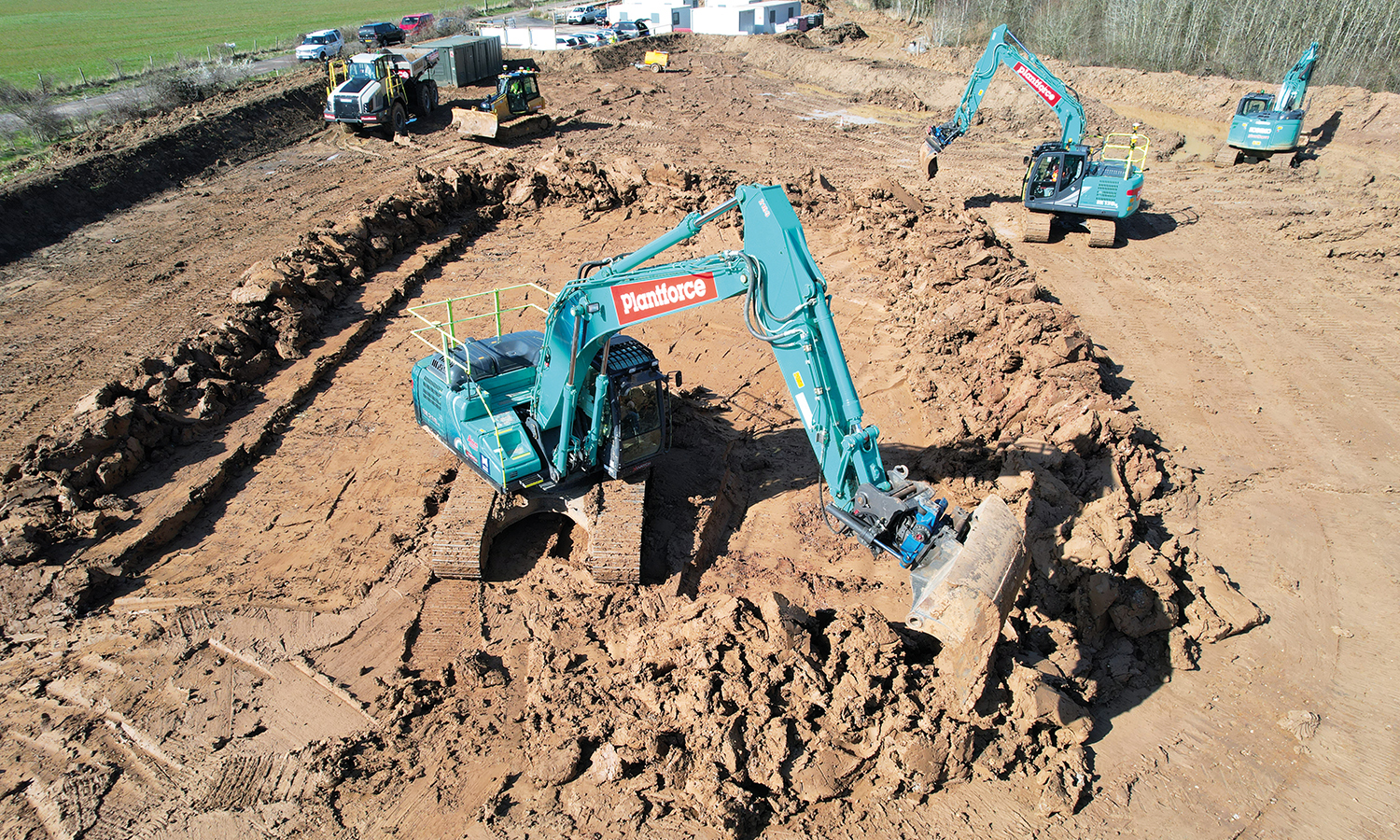
At Futureworx, Plantforce Rentals showed how it is remotely monitoring site work in real time.
Plantforce Rentals is one hirer demonstrating the potential for digital tech on heavy construction projects. At the Futureworx show in March, it set up a live ‘connected site’ demonstration, which linked all machines together on a single project dashboard. The hirer operated this from its training facility, run by LP Training near Stratford-upon-Avon, some 80 miles away from the event.
The company used a fleet including two Kobelco excavators, one with Leica Geosystems’ semi-automatic system, the other with Trimble 3D machine control, and a Trimble-enabled Cat dozer. They were linked together by telemetry specialist MachineMax’s equipment management platform.
Plantforce COO Sam Mercer says: “The MachineMax solves one of the biggest industry problems, collating information from different machine types into one dashboard. This allows us to take data and turn it into useful information, which is in turn fed to the people managing the operation.”
“This solves one of the biggest industry problems, collating information from different machine types into one dashboard.”
Plantforce connected each machine to the platform using a magnetised telemetry box that picks up the equipment manufacturer’s API. This is a data feed available from the machine, which allows real-time activity to be measured, whether in operation or idling.
“In this case, our team were monitoring activities like digging, grading and hauling, picking up on productive and idling times, fuel burn and CO2 emissions,” explains Mercer. “Idling is when the machine is being unproductive yet using fuel, so this is a key focus for us. We can alert site managers to excessive idling by setting alerts and best practice benchmarks.
By looking at data in real time, he says, a site management team can work out how much fuel is used for specific tasks. They can pick up productivity issues – such as a traffic jam of articulated dump trucks due to poor weather conditions impacting cycle times – and act immediately.
“Plus, there is the benefit of theft prevention and knowing where every asset is at any time, which was how telemetry first made a big impact in the industry,” he adds.