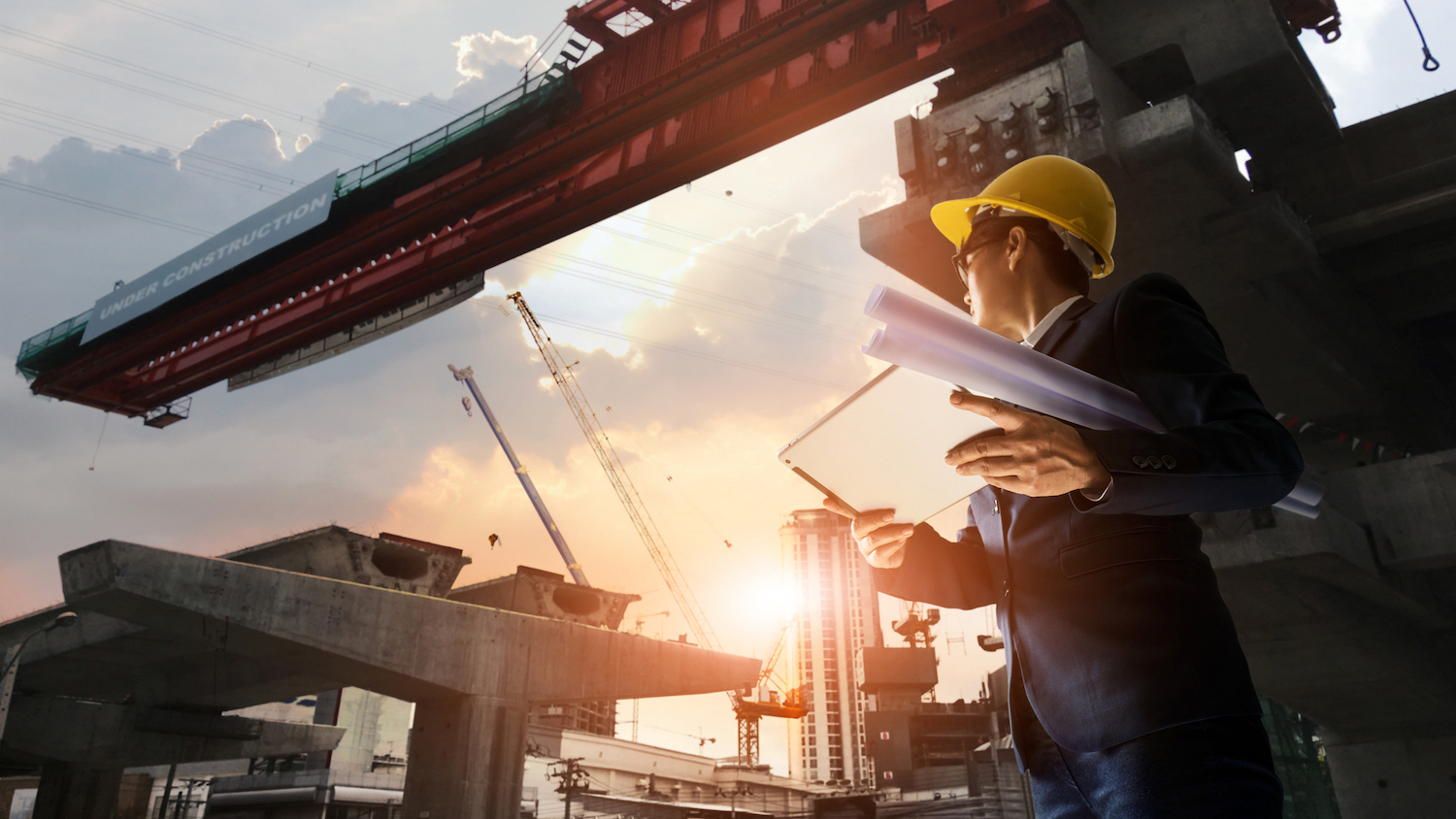
If you turn data into information, you can use that information to exert greater control over a construction project. That was one of the key messages from Buildots at a recent Global Construction Summit webinar that focused on performance-driven construction management.
Paul Bamforth, head of global strategic accounts at Buildots, kick-started the webinar by detailing what performance-driven construction management is and its benefits.
“It’s clear that data can be turned into information, [and information] can be turned into control,” he said. “Performance-driven construction management is really about making a shift from the reactive way, which has been perhaps the only way of reacting to projects falling behind schedule, to being a bit more proactive.
“[We can] be a bit more proactive in terms of management to identify delays early on, because what might be a problem today could be an even bigger problem tomorrow.”
He added: “Let’s measure regularly, let’s use the information that we might have from progress information, and start identifying and analysing what the consequences are, or what the issues are or could be. Let’s analyse that, then optimise. Do we need to put more people on? Do we need to look at the sequences that we have and the work that we’ve got in place to maximise utilisation of the site? It’s about being proactive.”
Leading not lagging
Andy Steele, strategic adviser and former chief executive of Osborne, illustrated the difference between traditional construction management and performance-driven construction management. “The human eye is incapable of determining whether something is 47% complete or 51% complete,” he said. “[The difference between a trade being 51% complete and 47% complete] is two and a half weeks behind [schedule] – that’s the lagging indicator. The leading indicator? It’s six months behind at that production rate.”
He highlighted the issue of trades returning to site. “What is causing that return visit? Is it a design issue? Is it a performance issue? [We need to] understand those returns, understand why we’re going back to make good certain areas, and learning from those. We see regularly that we can design out some of those return visits. A simple example, ductwork: rather than having to manufacture the last section, which is an on-site measure, design in a flexible final fitting. It costs more, but speeds up production. So think about performance.”
The horse has bolted
Paul Drayton, head of digital – Europe, at Laing O’Rourke, drew on his experience outside construction to illustrate the difference in mindset. “I’ve seen in construction, and in defence, aerospace and nuclear: we focus on the lagging measures, which report performance, they report output. The challenge is, if our performance has fallen short, we’ve missed the opportunity to do anything about it – the horse has bolted.
“Then, because we haven’t got the metrics that underpin that, we start reacting to opinions rather than dealing with facts and data and evidence to make informed decisions. By the time we start to see performance being impacted, it’s probably the last link in a chain of a whole sequence of complicated activities – it was probably born weeks, maybe even months, upstream where a design error was introduced or a material wasn’t ordered on time.
“So it’s important to measure the output performance to understand how you’re getting on, but actually, I think we need to understand what the key drivers of lost performance are, and we need to actively manage those. That’s the leading measure for me.”
Single source of truth
Gareth Handley, director of operations at Wates Group, outlined what Wates wants from information. “What we’re looking for, and what I’m principally focused upon, is really a single source of truth: having something that allows us to really measure our projects and understand exactly what’s happening. We want to be able to see where our projects are going. We want to be able to see that at a very global scale, and have really clear and defined information, but we also want our teams to be able to use that information.
“We’re looking for information that allows us to save time, particularly with the way that we plan our works and record where we are on our projects, because it can be very time-consuming, particularly on larger projects. We also want clear and concise information: information that can be used at a high level to understand where the project is and where it’s going and, more importantly, see those trends. We want [information] that the teams on the ground can utilise and share with their supply chain partners in collaboration meetings.”
He offered this plea to technology providers: “Please don’t make anything complicated, ever. As builders, we’re not concerned with how it works. I’m interested in it being accurate.”
The webinar was part of the Global Construction Summit, organised by the Chartered Institute of Building and Global Construction Review, and was sponsored by Buildots.
Don’t miss out on BIM and digital construction news: sign up to receive the BIMplus newsletter.