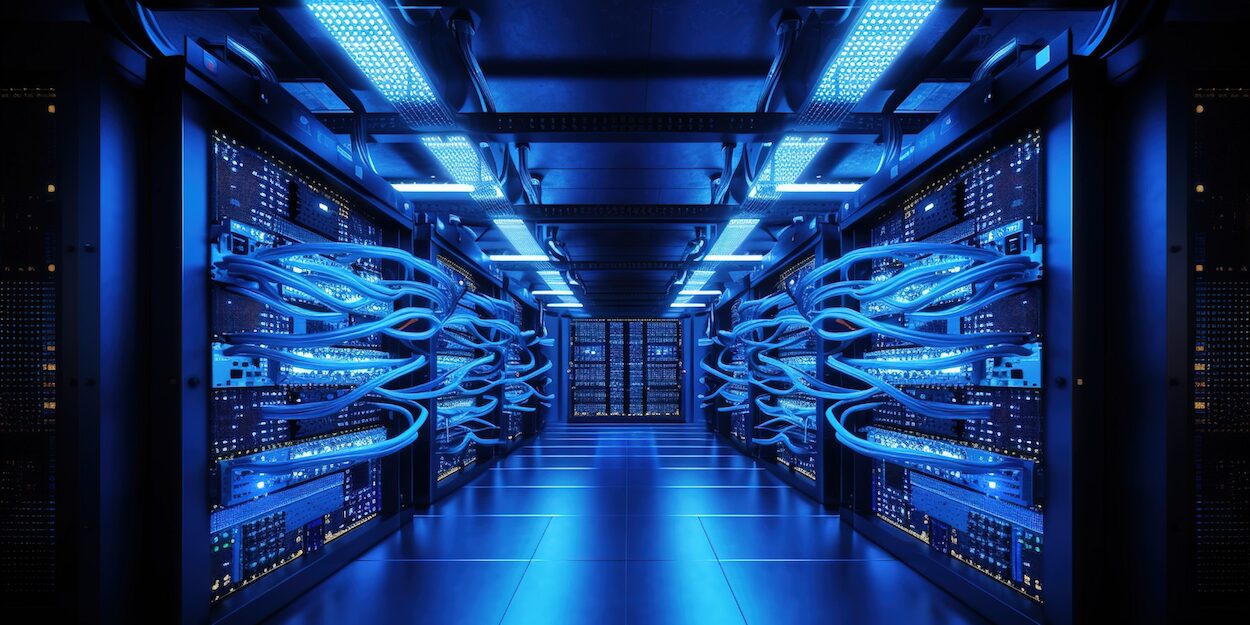
Data centre owners and contractors must focus on data-driven planning of their new builds and retrofits for the UK and Europe to meet the demands of big data.
Rider Levett Bucknall’s (RLB) Annual Data Centre Report surveyed 535 executives from data centre operators and contractors across the UK and Europe. The report reveals that operators commissioned 33MW of data centre capacity in 2024. That figure is more than twice the average in last year’s report (16MW) and substantially more than last year’s respondents had expected to commission (26MW). This growth is set to continue: operators expect to commission 47MW, on average, this year.
Operators are not just planning new sites: 66% plan to retrofit at least a quarter of their data centre estate in the next five years, with 20% expecting to retrofit more than half.
Almost needless to say, processing power for AI is driving the current surge. RLB noted that conventional workloads are not being replaced by AI, rather it is adding demand to an already growing sector.
This has put the data centre construction supply chain under increasing strain: 70% of respondents believe it is struggling to meet demand. Indeed, 53% said that supply chain constraints will prevent Europe’s data centre industry from building enough capacity. And 54% believe Europe will fall behind on AI unless these constraints are resolved.
Digitalise to de-risk
RLB suggests that data centre construction supply chains must digitalise to help de-risk the sector, particularly focusing on the availability of construction and electrical fit-out materials. “Every developer stands to benefit from data-driven production planning. Tracking equipment throughout the supply chain means delivery delays can be anticipated. And if one project in their portfolio suffers an unforeseen delay, assets can be redirected to alternative sites. Also, asset tracking beyond delivery into the operation phase can reveal the true lifecycle cost of equipment.
“The level of digitisation in supply chain monitoring varies greatly across the industry, however. Hyperscalers [the very largest data centre operators such as Amazon Web Services and Microsoft Azure] may have direct access to their suppliers’ inventory data. But for smaller developers, the next step might simply be to move supply chain data from Excel into dedicated applications.”
Michelle Zompi, head of RLB Digital, highlighted the need for visibility. “Digital technology provides far greater visibility into the supply chain risks than has ever been possible,” she said. “To mitigate these risks, [data centre operators and contractors should] integrate digital platforms and dashboards throughout the project lifecycle and use real-time data analytics to identify potential disruptions before they happen.”
Rob Jackson, head of information management services at RLB Digital, added: “A successful data centre construction project depends on effective information management, to ensure data is fit for purpose and available when and where it’s needed. Building a centralised document management system, for example, can improve project transparency and communication, minimising the chance of delays and disruptions.”
Don’t miss out on BIM, information management and digital construction news: sign up to receive the BIMplus newsletter.