Wessex Water and Aecom used Igloo Vision’s Shared VR technology to improve teamwork and save £300,000 in costs on the reconstruction of the Durleigh Water Treatment Centre near Bridgwater in Somerset.
As its flagship scheme (and an important part of its current asset management plan), Wessex Water had planned a £50m upgrade of the Durleigh Water Treatment Centre.
The upgrade would enable Wessex to consistently and safely deliver 30 million litres of water a day while addressing concerns over deteriorating raw water quality and the presence of pesticides and manganese.
The plan entailed demolishing all the existing structures at the north end of the site. This would remove an admin building, a dissolved air flotation (DAF) plant and sand filters. This would be replaced with a new main treatment building with processes for DAF and rapid gravity filters, manganese filters and a new low-lift pumping station.
Wessex Water appointed Aecom as one of the six Tier 1 Design Capital Delivery partners to undertake the detailed design of the civil engineering and mechanical and industrial engineering (M&IE) works. This would be together with integrating the design elements undertaken by others.
Wessex Water’s project to reconstruct Durleigh was its first scheme to be delivered to BIM Level 2. That meant the use of collaborative 3D models with embedded digital versions of all project and asset information, documentation and data. This was necessary due to the complexity of the site, where there were numerous existing underground services to be modelled. Furthermore, with the plant providing drinking water for 40,000 people in Somerset, it was crucial for it to be of the highest quality possible.
The solution
Wessex Water worked with Aecom to introduce a digital strategy to bring a range of technologies and innovations to form a comprehensive digital engineering approach to the scheme and wider business. These included:
- Creating a single source of information. A Common Data Environment stored all design information in the cloud, instead of a local server. This enabled high levels of collaboration across the supply chain, from project management to engineering, procurement to operations.
- A digital model that fully integrates all civil, mechanical, electrical and process design. Ground penetrating data, laser scan data and drone surveys were used to create a highly accurate model of the new plant design. The use of drones also eliminated hazards associated with working on a fragile roof.
- Digital design reviews. Visualising the scheme in 3D allowed the delivery team to quickly understand the look and function of the proposed construction works, which would enable prompt on-site decision making.
- Design for Manufacture and Assembly (DfMA). By maximising opportunities for offsite prefabrication of components, efficiency could be increased. This reduced risks and helped deliver the scheme to deadline targets.
As part of this strategy, Aecom saw the potential for the use of an immersive, collaborative environment and suggested an Igloo shared VR system. A 6.5-metre cylinder was purchased and would play a crucial role in the design of the refurbishment.
“We use the Igloo to go through design models with the operations team to make sure they’re happy with all access and maintenance for their bits of kit,” explains James Leverton, digital solutions lead at Aecom.
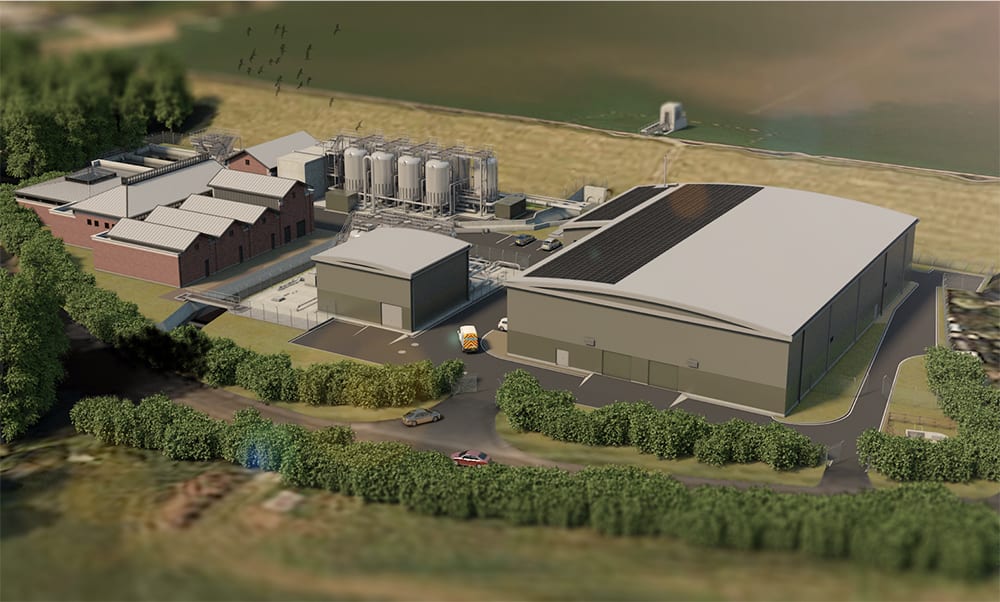
Durleigh Water Treatment Centre is Wessex Water’s flagship project
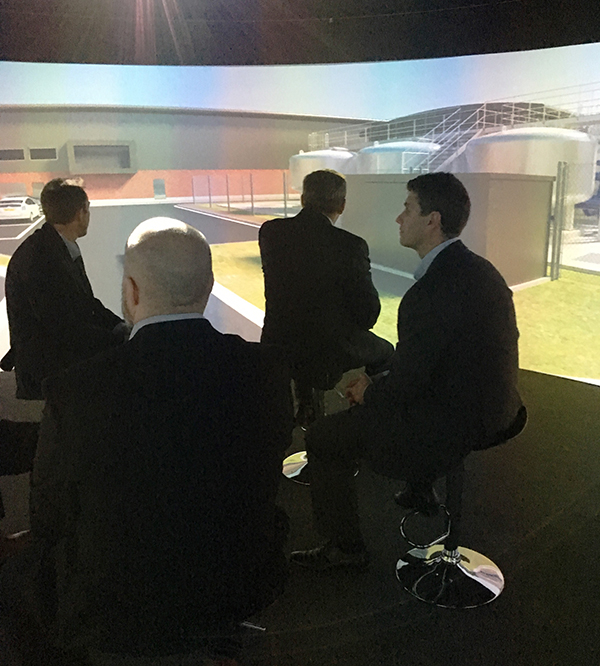
Up to 12 team members at any time could walk around the VR model of the site and carry out design reviews
Wessex Water had initially suggested implementing some form of AR or VR to aid design. Aecom trialled mixed-reality smart glasses, but struggled from a logistical perspective in visualising models. Wessex Water was also concerned that headsets would not be well received by stakeholders.
“We had early conversations with the client about using the HoloLens, but some of its delivery managers were not comfortable with wearing goggles that can restrict eye contact,” adds Leverton.
Wessex Water wanted the benefits of VR, such as being able to visualise a model instead of having to pore over detailed 2D drawings, while retaining the benefits of the team dynamic. With an Igloo Shared VR system, this allowed it to:
- Work collaboratively – everyone could see what everyone else was looking at;
- Brief team members – people could easily talk through what immersive content was being displayed;
- Communicate effectively – team members could gauge reactions by being able to make eye; contact, read facial expressions and body language;
- Facilitate group discussions and arrive at a consensus opinion;
- It also saw an opportunity to engage subcontractors.
In the past, the only way to share the plans for a new model was by looking over the complicated 2D drawings. With Shared VR, it was possible to showcase and visualise a 3D model in an immersive environment where people can even walk around the virtual model. This can also identify DfMA opportunities by providing equipment suppliers an immediate understanding of the project.
Aecom created a 3D BIM model with data from ground-penetrating radar, laser scans and drone surveys. This 3D model was then combined with Revizto software to create a VR model.
The Igloo Shared VR system (a 6.5-metre diameter cylinder) was assembled inside a disused building on the site. The size enabled up to 12 team members at any time to walk around the VR model of the site and carry out design reviews.
To make changes, laptops installed with Autodesk Revit and AutoCAD Plant 3D software would update the BIM models. Changes were pushed via the cloud to Revizto visual collaboration software. This could then be synced to the local Igloo server for viewing in a complete 360° immersive environment.
To navigate the VR environment, team members could use an Xbox controller.
The VR model also enabled the production of offsite components by providing information for equipment suppliers. 3D supplier fabrication details were inputted into the model. This would ensure the integration of the components into the site construction when delivered ready-made.
“We can all come into the Igloo space, and also join by Revizto’s camera share, and have an informed review session and ensure that the decisions that are being made are the right ones by the right people, and Igloo allows you to do that,” says Rhys Lewis, business development director at Revizto
Evaluating the impact
The initiatives had considerable success and impact. The cylinder was used for design coordination, including clash detection, and for testing and reviewing plant operability.
The Igloo Shared VR cylinder also helped identify opportunities for value engineering. This included rationalisation of the wastewater area, increasing efficiency. Having the cylinder located on site was also beneficial to design coordination. When designers spotted a problem, they could return to their desks, update the model and place it back into the cylinder.
The Igloo significantly boosted levels of engagement among both team members and stakeholders. Audiences were extremely enthusiastic. The Igloo worked well to facilitate team conversations and discussions.
“In the past, we have had real difficulties presenting operations teams with detailed 2D drawings that they couldn’t really understand. Inside the Igloo they got it straight away, it stimulated lots of good conversations,” says Simon Osborne, delivery manager at Wessex Water.
“We are seeing a number of benefits such as improved engagement and project buy in from our operations colleagues, and more efficient, effective design reviews with significant time and cost savings.”
Despite the cultural changes needed in the water industry, Aecom only needed to produce a single set of piping and instrumentation diagram (P&ID) drawings. All other reviews were from the BIM model.
Aecom has spoken to Wessex Water about the possibility of developing BIM for use post-handover. Shared VR has made a strong contribution to how Wessex Water works. It may now be crucial in meeting challenging efficiency targets from the regulator.