Technology has added new dimensions to asset information modelling for Hamilton City Council’s wastewater treatment plant, where it is using drones to capture site-wide geometry, laser scanners for building and asset geometry, and mobile devices linking virtual objects to barcoded assets.
While buildings conceived and built in the pre-digital age, when designers used pens and tracing paper, occasionally possess magical qualities, they are often a headache to manage, because important asset information lays buried in legacy systems or under stacks of paper.
A typical example can be found on New Zealand’s North Island with Hamilton City Council’s Pukete wastewater treatment plant, which was built in 1975, with a $28m upgrade in 2002 providing secondary and tertiary treatment.
Parvati Patel, an asset engineer in the City Waters team, was tasked with modernising the facility’s asset information. However, a lack of as-built information, uncertain accuracy of existing data, and time-consuming location of asset information for new works and maintenance made her job harder.
The council’s decision to adopt more advanced asset management practices turned the spotlight on processes for collecting and centralising data, with a view to dynamic information modelling. The move addressed immediate concerns relating to the risk of contractors digging up services, health and safety, and potentially expensive design rework when assets were located in places that no one expected to find them.
“We need to know what we have, how to maintain it, and what it will cost to keep it running,” says Patel. “We must have good information.” With an eye to the future, Patel and engineering consultant Beca scoped out a BIM framework to develop a data model that would ultimately integrate with the council’s asset management system.
The process
Pushing aside 2D drawings, the project team deployed a drone to scan the entire plant site to produce a photo-realistic 3D point cloud of hard surfaces, including building shells and ground features.
Next came process areas inside buildings. Here, the survey team used Lidar (light detection and ranging) laser scanning to generate a 3D point cloud of building interiors and assets. Combining point clouds with modelling software led to the creation of a detailed model of the aeration blower, RAS, and MCC rooms, including plant and equipment, and building shell architecture.
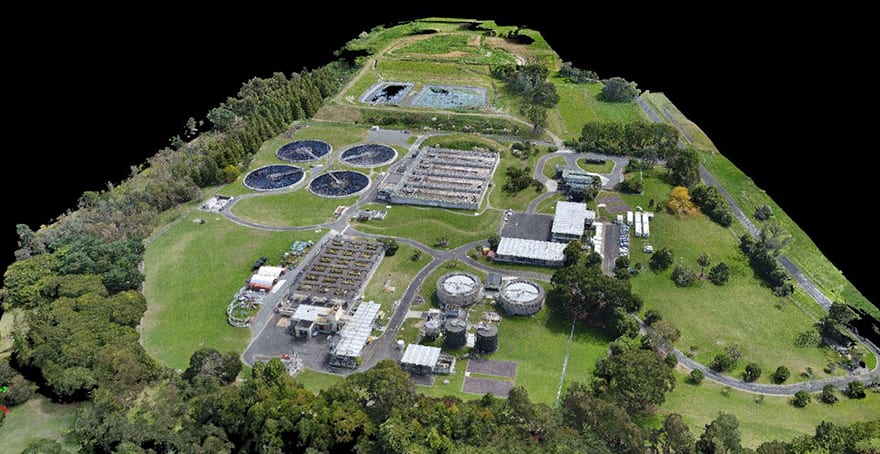
Consultants undertaking design work benefit from a clearer picture of related elements, working with detailed information about ground slope, surface areas, and the position of connecting assets
Migrating the model to EcoDomus, a cloud-based building lifecycle management platform, set the scene for the addition of data, with key asset data fields attributed to elements within the model. Operation and maintenance information, including process and instrumentation diagrams, process flow diagrams, operations manuals and warranties, were attached to the model, centralising asset information to create a “single source of truth” for operation and maintenance activities.
In a move to bridge reality with virtual worlds of 3D modelling, BIM technicians linked existing barcodes on plantroom equipment to profiles embedded in the model. Now, contractors onsite have the opportunity to use a barcode scanning app on their tablets to confirm they’re working on the correct piece of equipment.
Challenges and constraints
Information about a “living” asset constantly evolves. For example, the make, model, and serial number of a pump will be known and uploaded to the model, but developments such as recent repairs or maintenance can be overlooked. As council buildings and assets age, asset managers must maintain a watching brief to keep the model up-to-date.
Ultimately, the model will integrate with the council’s asset management database and financial systems, with the cloud-based lifecycle BIM platform automating the flow of information between the model and supporting applications.
Results and benefits
At the broadest level, the council’s BIM model is a platform for digital asset management, providing functions to visualise and interrogate more detailed information about its assets. Managing contractors will soon be recast as an exact science, with the 3D model confirming the identity of equipment, its location, and important asset data – before works start. The model also serves as a tool to run contractor safety inductions.
These assets, with these attributes, and all the information is linked to the correct asset on site, is great – it removes confusion. Aggregating this kind of information in a visual format makes it easy to access and cross reference – and much simpler for people to find what they need.– Parvati Patel, Hamilton City Council
Consultants undertaking design work benefit from a clearer picture of related elements, working with detailed information about ground slope, surface areas, and the position of connecting assets. Whereas 2D models put designers in the ballpark, 3D models show everything in 360-degree glory, identifying clashes with other assets or, for example, if a pipe will fit into a wall space.
“To say that we’ve got these assets, with these attributes, and all the information is linked to the correct asset on site, is great – it removes confusion,” says Patel. “Aggregating this kind of information in a visual format makes it easy to access and cross reference – and much simpler for people to find what they need.”
Along the way the council has also notched up a few unexpected wins. When rain washed away spray-paint marks indicating ground penetration work, a quick review of imaging captured by the drone put everyone back in the picture. And when a contractor removed a mound of earth dug from a trench, imaging put an exact figure on the volume of earth, helping verify removal costs.
The pace of work has also picked up, now that everyone is working with reliable information – and the days of collecting new survey data at the beginning of each new project are over.
Cost considerations
Patel says the case for developing a BIM model focused on non-financial benefits, including a better way to manage assets, with more informed maintenance and less design rework.
Nevertheless, the model was developed with costs in mind, which helped put boundaries to the scope of its development. “Costs associated with developing the model should be proportionate to client needs,” explains Glenn Jowett, senior associate and BIM delivery lead at Beca. “You’ve got to understand why you’re developing something and what it will be used for. Why document every nut and bolt in steelwork when all you need to know is what’s there and its position?”
He adds that despite misconceptions about BIM’s applicability to existing assets, the project demonstrated the value of digitising and centralising asset information using BIM. “BIM is often discussed for new builds and assets, but in reality the majority of asset owners own many more assets than they build each year. If you can leverage BIM technologies to operate and maintain existing assets you will capture far more value in the long run.”