- Client: Brown University
- Lead Contractor: Shawmut Design and Construction
- BIM Tools: Autodesk BIM 360, Navisworks, Trimble SysQue
Brown University’s engineering department was elevated to the School of Engineering in 2010 and with several disparate facilities around the Providence, Rhode Island campus, it was decided to build a new Engineering Research Center to create a unified home.
Completed in 2018, this 81,330 sq ft facility features cutting-edge research labs, clean rooms, an imaging suite, and flexible work spaces. It is thought to be the first institutional lab in the US to be delivered using the innovative integrated project delivery (IPD) model, under which the owner, architect and contractor are mutually responsible for design development, stakeholder engagement and keeping construction on time and on budget.
Key to meeting IPD’s unique focus on project team integration, communication and collaboration was the use of advanced BIM tools during design and construction.
Paul McGilly, an associate principal and digital design manager at BuroHappold Engineering, which provided structural and MEP engineering, facade consulting and lighting design services, told BIM+: “Traditional design-bid-build, or design-build projects, involve a series of handoffs between the consultants and the construction team, however with IPD everyone engages with each other starting at concept. This early engagement is key to developing a workflow that can be agreed upon and developed by all partners for early project implementation.”
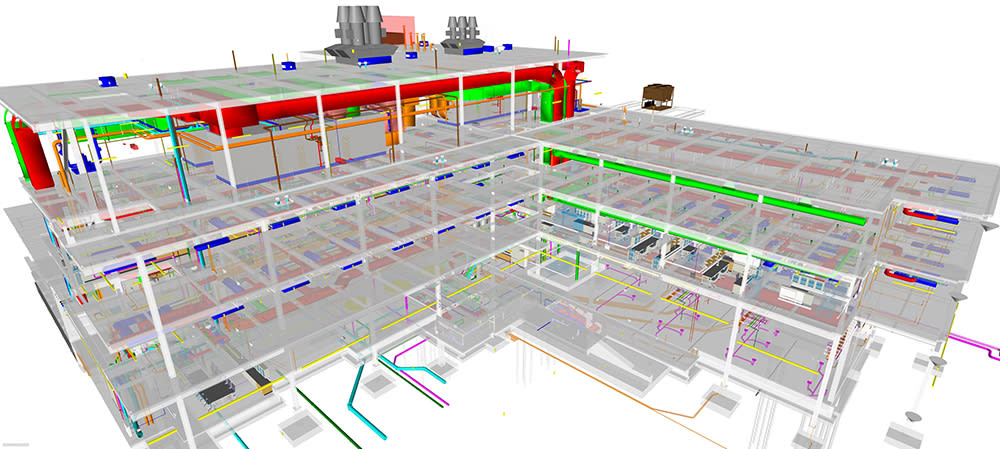
The cloud-based construction management software Autodesk BIM 360 was adopted to enable the synchronisation and sharing of BIM models between the design and trade partners, located across various cities in the US. The browser-based platform allowed seamless interaction and flow of BIM data. This was considered a more streamlined approach than the more traditional alternative of VPN access to a server, involving firewalls, IT teams, networks and security.
“BIM 360 is essentially plug and play, with a license purchased for each user, and a scalable network able to cope with the transfer of information,” says McGilly, who was a driving force behind many technological solutions deployed on the project.
The team utilised the full spectrum of tools available on BIM 360, including BIM 360 Glue for real-time clash investigation and resolution. On a regular basis, designers and trade partners would collaborate in a colocation space on site at Brown University with coordination sessions focused on resolving any issues in the BIM model and any updates uploaded immediately to the cloud. Ultimately, close collaboration among all teams resulted in a project that went to site with zero RFIs.
To stay within budget the team used model-based cost estimating. Costs were tracked and reported weekly from dynamic schedules and take-offs generated from the models. These regular cost reports empowered designers and trade partners to make design decisions based on project budget.
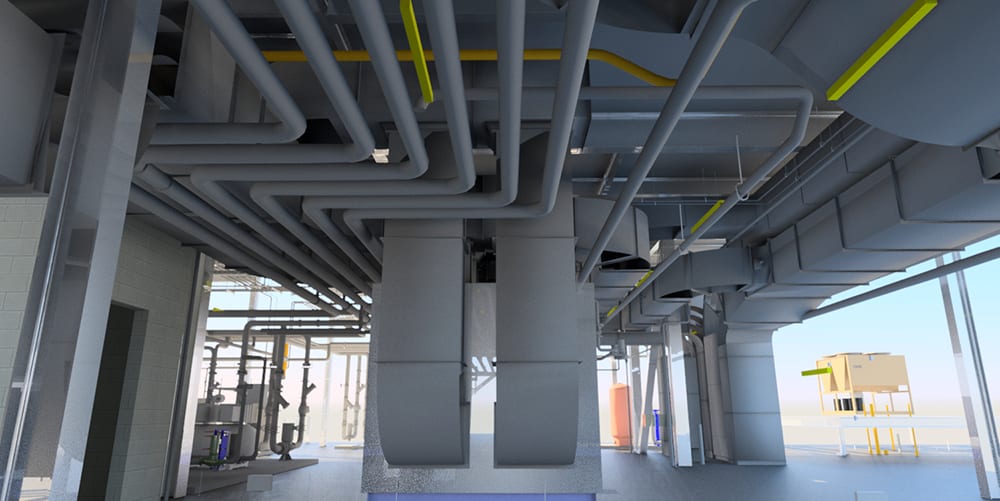
Projects can suffer from a lack of continuity in the design to construction process in a more traditional workflow, with the design model often archived and the construction model developed from scratch.
IPD’s focus on collaboration and lean construction helped remove that duplication of information and wasted effort. Revit and BIM360 tools were used to develop the design model to a detailed construction model with LOD 500 needed by manufacturers to prefabricate various elements.
The third party Revit plug-in Trimble SysQue enabled this process by converting Revit system elements into a format compatible for fabrication. Sysque’s library of three million Revit families also helped in the development of the construction model.
Brown University’s facilities management team has inherited the project BIM models, which include asset data for electrical, mechanical, plumbing and fire protection equipment and fixtures, for use in commissioning, ongoing repair and maintenance work and future research lab fit-outs.
“Ultimately, we want the data in the BIM model to be interoperable with the building management system, using our own in-house developed solution, as part of an ongoing partnership with the client over the lifecycle of the building,” says McGilly. “We see that as the next step for this technology on future projects. Collaboration is about continued engagement to ensure that data stored in BIM, during design and construction, can be exploited by the client throughout the building lifecycle,” he concludes.
The Engineering Research Center was handed over in November 2017, three months ahead of schedule.
Comments
Comments are closed.
Dear Sir/Madam,
Thanks for the IPD & BIM collaboration. Which BIM protocols did you applied to this project? Was it a Level 1 Bim or Level 2/3?