- Client: Coventry University
- Lead Contractor: Willmott Dixon
- BIM Tools: Solibri Model Checker, Tekla Structures, Matterport
The next generation of cleaner electric, hybrid and petrol/diesel engines will be developed at the cutting-edge automotive testing and research facility located on Coventry University’s Technology Park.
The £15.5m development forms part of a long-term collaboration between the university and powertrain and vehicle systems developer FEV, the tenant that will operate the facility.
Procured through the Scape National Major Works framework, the building features five state-of-the-art powertrain test cells, offices, a workshop, a car parking and soft landscaping.
Willmott Dixon acted as BIM information manager and set up the project to meet the requirements of Level 2 BIM, having committed to deliver BIM on all projects, where practicable, at the start of 2019.
It was the client’s first foray into BIM and initial employer’s information requirements were generic and not based on actual asset management needs. During design and construction, Coventry University’s estates team got up to speed and clearly defined their asset management information data requirements. Willmott Dixon delivered the change request for the asset data for no additional cost.
Chris Johnston, digital manager at Willmott Dixon, told BIM+: “It’s a very complex building with lots of associated maintenance. We assisted with various ‘hand holding’ sessions, as a contractor we try to leave customers with a better legacy going forward and part of that is giving them the information they need to better manage a facility.”
The COBie data set was adapted to make it suitable to import into the customer’s facilities management software Planon.
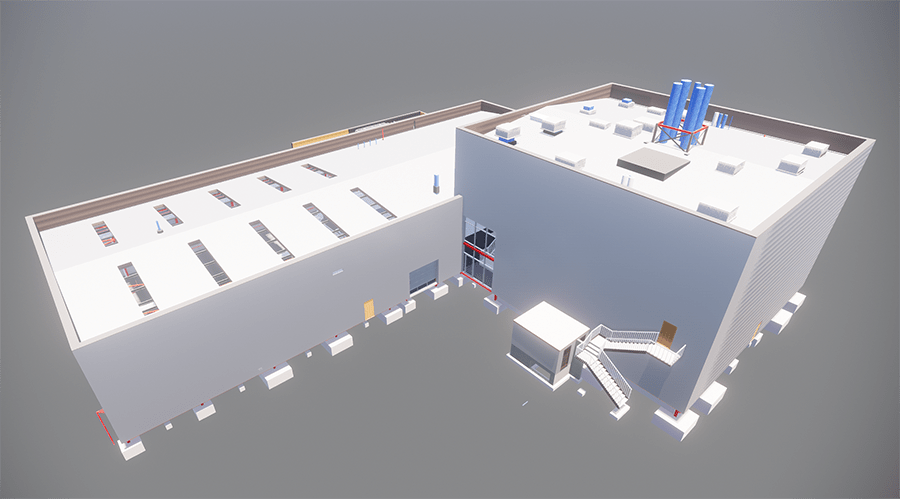
BIM was considered critical to the project due to the large amount of offsite manufacturing
Coordinated design models were produced by various consultants and supply chain partners, including the architect, Broadway Malyan, structural engineer CWA Engineering, M&E contractor NG Bailey, steel frame contractor Midland Erection and civils and groundworks contractor Dunton Environmental.
BIM was considered critical to the project due to the large amount of offsite manufacturing, particularly M&E systems, such as hot rolled pipeworks (spoils), cassette units with pipework and cable trays and chillers. NG Bailey refined the consultant’s design to include the procured components before the systems went into production.
Willmott Dixon extended its role as information manager to produce a construction simulation site model. The 4D animations of set sequences of work linked to the construction programme helped its design and construction managers refine the programme and delivery times.
Johnston said: “It helped to really crystallise the thinking of construction managers because they could clearly see where activities were happening where, what was going on around them, and the health and safety considerations around those activities.
“A regular construction programme shows where production is going to start and things like what side the steel structure will be erected from, or what will happen when the cladding meets it from another direction. It helped them think through the sequencing.”
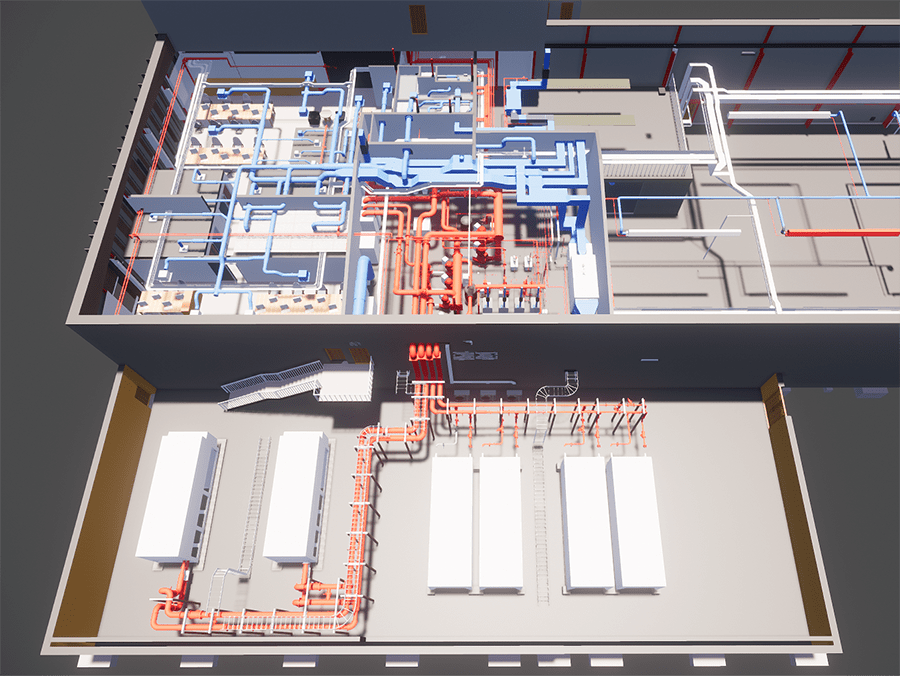
The building is complex with lots of associated maintenance
The innovative car engines will be tested to failure in the test cells, large concrete tanks with complex service requirements designed to provide protection and moderate noise.
3D models of the test cells were produced by FEV in a Siemens suite of software, which raised challenges when it had to be transferred into BIM.
Simon Graham, BIM manager at Willmott Dixon, commented: “The engineering design came in a completely different orientation, which meant we really had to grapple with it to use it as coordination. The consultants were very constrained on where they could install equipment in the test cell areas, such as fuel intake and waste extract etc, so they had to design around the tenant’s requirements and visually see the detail.”
The interoperability challenge was compounded by the fact the project had “stepped outside the Autodesk bubble” and allowed consultants and suppliers to utilise a range of software, including Solibri Model Checker, Tekla Structures, and Synchro for the 4D construction rehearsals. As such, IFC files were required to perform clash detection.
As the project progressed, a Faro laser scanner was deployed to capture the completed primary frame, and subsequently post-first fix M&E, and the 3D point clouds overlaid on top of BIM to check that the as-built asset was in alignment with the design.
A Matterport scanner was deployed to capture the building and create a Google Streetview-style click-through model designed to allow the client’s offsite estate teams and FEV, which is based in Germany, to navigate the building remotely.
Johnston commented: “It meant they didn’t have to fly people over to look around, we just sent them a URL address, they saw it as a very valuable tool for things like inductions.”
Images: Simon Graham of Willmott Dixon produced the screengrabs using the visualisation product Enscape