- Client: Stavanger University Hospital
- BIM Tools: 100% international open standards, compatible with Revit, ArchiCAD, Solibri and others
Oslo-based BIM developer Imerso has been given responsibility to monitor work progress in one of the biggest public construction projects in Scandanavia.
The new Stavanger University Hospital is being built in Stavanger, 300km from Oslo. The first stage of the construction, which should be ready in 2023, covers 130,000 sq m, the equivalent of more than 14 football pitches. It has been designed by COWI, the Norwegian-based international consulting group, and the Nordic Office of Architecture. In November 2018, the project was named BIM World Champion in the large project category in the annual Autodesk Awards
At peak times, up to 1,000 people will be working on the project. The new hospital has a planned capacity for 640 patients and specialised world-class laboratories for day care, radiology and emergency departments. The total budget of the project is approximately £800m.
The client is the hospital’s project management team, which wanted an automated project oversight tool to help it manage the size and complexity of the project.
This is the first time that a public organisation opened a competition for such an advanced AI system in Norway. Imerso was selected out of seven companies that applied in early 2020.
Virtual checking
Imerso is responsible for creating an accurate digital twin of the new hospital. The construction is 3D scanned continuously to check the work status against the building plans using Imerso’s AI software. The platform compares the scan and the BIM and immediately catches any problematic discrepancy.
Instead of the traditional methods of manual inspections and spot checks, which can take weeks, the platform allows a faster examination of the work quality and avoids subjective evaluations. The goal is to be aware of costly work mistakes as soon as they happen.
Software development
Imerso AS was established in 2014 as a deep-tech software company conducting R&D in collaboration with SINTEF and Simula Research Laboratory, with sponsorship from the European Commission and the Norwegian Research Council. It is privately owned.
The company developed a platform that uses AI to track work quality and progress in real time, while creating a full 3D digital twin of the job site. This virtual copy is created by combining BIM and 3D scanning technology, which Imerso makes as simple as taking a photo. Instead of manual inspections that can take days, or even weeks, everything built at the site is inspected by a computer within minutes and with millimetre accuracy.

Imerso has also established a partnership with the 3D scanner manufacturer Leica Geosystems to integrate the system with the latest and fastest scanning equipment available
Imerso’s system uses the BIM plans as inspection targets and automatically analyses the as-built reality captured in the 3D scans to detect work deviations. The digital twin evolves in parallel with the construction activities and gives early alerts of potential problems before they happen. This allows projects to avoid huge unnecessary costs, delays and disputes, by enabling the work teams to rectify any issues proactively.
With this 3D copy of the construction site available online, all project stakeholders can navigate the virtual job site together from their browser in a collaborative workflow, just like being there in person. Users can take any measurements, screenshots from any perspective, prepare upcoming work packages, and append comments directly to the virtual objects.
Imerso has also established a partnership with the 3D scanner manufacturer Leica Geosystems to integrate the system with the latest and fastest scanning equipment available. With a measuring rate of up to 360,000 points per second and an advanced 360-degree imaging system, the creation of a coloured 3D copy of the construction site can be done in a matter of hours. Imerso delivers all data in 100% international open formats to ensure compatibility with any industry tools.
Preventing disciplinary clashes – how it works
All details of a construction site are captured with the 3D laser scanner. The building plans, like the coloured pipes, are laid over the scan data. The result is a ‘mixed reality’ view, where you can access the construction site via your web browser (see image 1, top).
The results from the scanner are automatically uploaded to Imerso’s web platform and compared to the plans. In image 2 the left image is the scan data. In the right image, the scan data is colour coded: everything according to the plans is in green, while all deviations are in red. It shows that the column and left-side wall are different from the building plans.
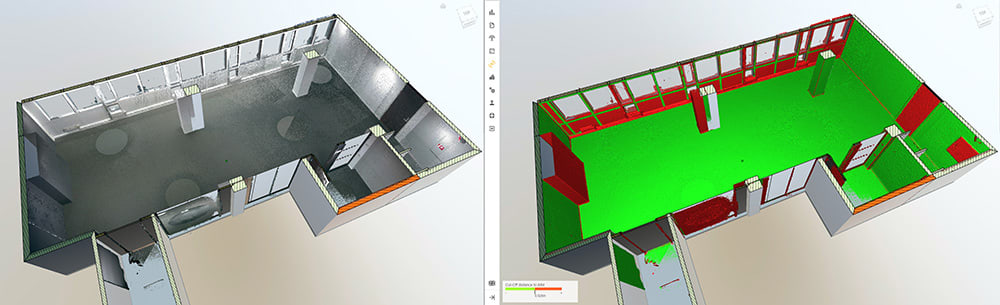
Image 2: The results from the scanner are automatically uploaded to Imerso’s web platform and compared to the plans
Image 3 shows the scan data alone on the left. In the right image, the wall is tilted, and falling on the right upper corner – the colours go from green (within tolerance) to red (outside tolerance). Doing this flatness analysis on any walls or floors is done automatically and only takes a few minutes.
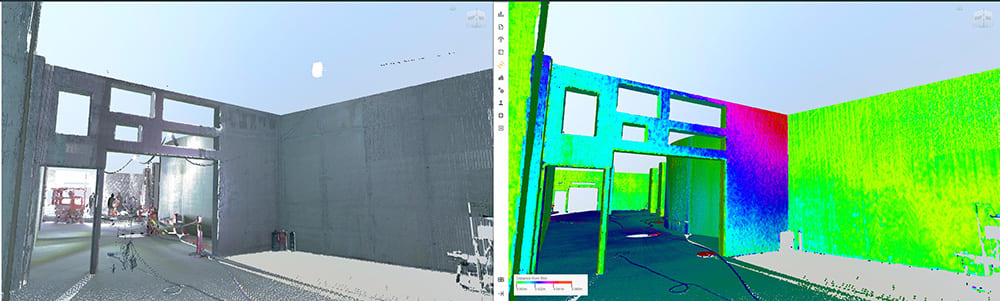
Image 3: The left image shows the scan data alone. In the right image, the wall is tilted, and falling on the right upper corner
Image 4 shows that the wall opening is misplaced, and the technical installations will not fit according to plan. Fixing this deviation now is much cheaper than having the teams arrive onsite, and not being able to do their work.
Software interoperability
Imerso’s software is based 100% on international open standards to ensure interoperability with any other industry tools. Its scans and deviations reports can be exported to any of the most common industry tools, including Revit, ArchiCAD or Solibri.
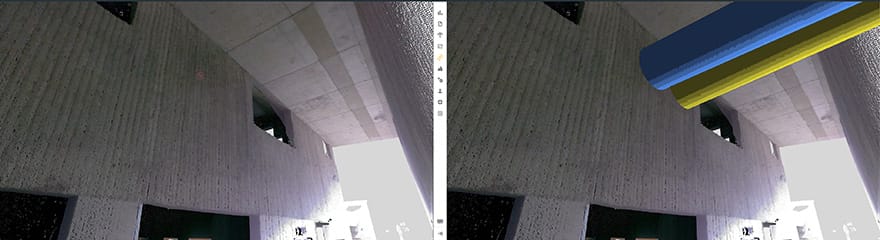
Image 4: the wall opening is misplaced
Comments
Comments are closed.
Wouldn’t it be better to use VR or AR to build it right the first time?
@Paul, Both flows of information are indeed needed, not mutuality exclusive. Many of our customers are using VR in planning as well as AR within quality control, but these are still visual inspections that take a lot of time onsite, and also cannot control everything (especially with tight tolerances). Per example, floor flatness is not possible with AR.
In addition, those approaches produce no documentation of status and progress, and each work milestone needs to be documented and approved (all green) before the next phase. That’s where Imerso comes in.
Our solution goes beyond all of this, leaving subjectivity aside and reporting potential issues automatically in minutes after a scan is submitted.
Happy to discuss more ideas with you! Ping us on [email protected] for a chat – Best wishes, Sarah