- Client: Bradford College
- Lead Contractor: BAM Construct UK
- BIM Tools: Navisworks, BIM 360 Field, Asta Power Project, Costx, ArchiCAD, Revit & Autocad fabrication MEP
Bradford College is an important part of West Yorkshire’s higher education landscape, with a 182-year history and 25,000 students. It is also in rapid transition: rebranding, sprouting satellite colleges, laboratories, sports centres and renewing its accommodation. The six-storey, £50m David Hockney Building, named after the college’s most famous old boy, replaces three existing teaching blocks and is designed by Bond Bryan Architects to evoke the wool mills of Yorkshire’s past. Turner & Townsend worked as project and cost manager.
Contractor Bam Construct UK decided to make it a pathfinder project for Autodesk’s BIM 360 Field, which uses mobile technologies and a cloud-based software platform for collaborating, data capture, management and reporting functions. This means that site managers and foremen can access the BIM model in real time on site using tablet computers.
Mark Taylor, the BIM manager for BAM, says that initially there was a mixed reaction from subcontractors: those who hadn’t used the system before would have preferred to work in a familiar environment, but others bought iPads for their operatives.
But the first time the site staff and the subcontractors saw the model on their tablets, it seemed the fears of the doubters were realised: Taylor says the model looked like “a white shoe-box”. Investigation revealed that the colour information from the architect’s Graphisoft ArchiCAD ifc files were not being translated in BAM’s Navisworks platform. The solution was to work with AutoDesk to produce a patch, which fixed the issue.
BAM was using Navisworks and Asta Power Project as its planning and coordination tools, and worked with the architect to make sure its design model facilitated the construction process as well.
Taylor says: “We wanted to timeline the work, then following that we worked with the architect so that the model fitted with the build process and allowed us to try out scenario planning. For example, the tendency is to model something full height, but we wouldn’t build it like that, so we worked with the architect to break the model down and add phasing data.
“We also exported space information to help create a planning and logistics model that also included the works from our temporary works guys. It was a concrete frame with large atrium that required a lot of propping, so we incorporated the formwork into the BIM model. And as we had a tightly constrained site, with multiple demolition and construction phases, we also modelled site set up and hoarding lines.”
The next phase of the trial was to look at how site teams could be made more efficient and collaborative. The aim was to minimise rework and defects, and ensure health and safety best practice was adhered to. Here, BIM 360 really made a difference, Taylor says. “It allows you to do health and safety checks, quality assurance checks, raise issues and it meant we could stop somebody and say ‘you shouldn’t be doing this’, and you could show them why because you’d got the information at hand.
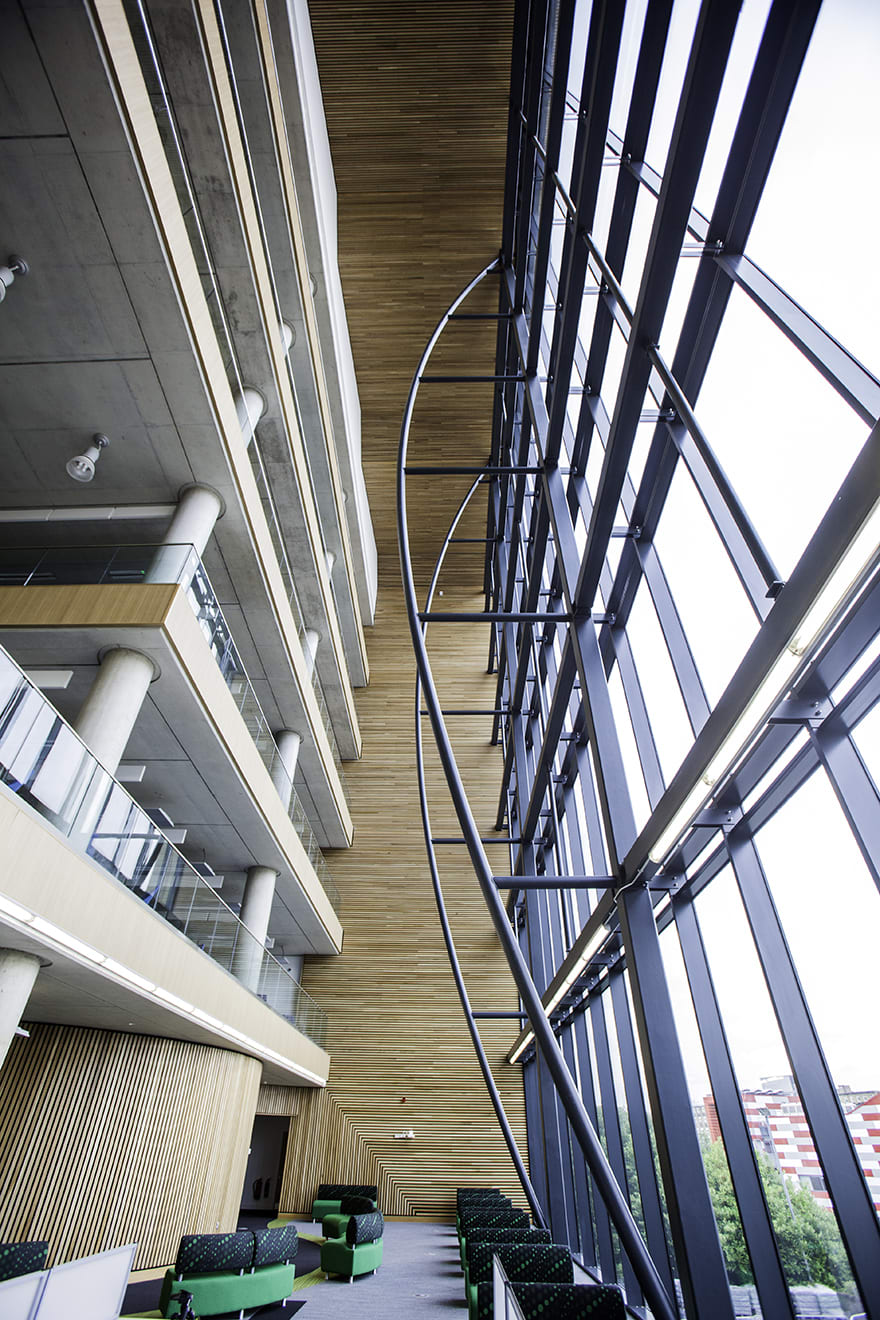
The BIM 360 system had a big effect on how quickly and effectively problems could be dealt with
We wanted to timeline the work, then following that we worked with the architect so that the model fitted with the build process and allowed us to try out scenario planning.– Mark Taylor, BAM
“Traditionally, you’d use paper checklists completed in the office, but this was a large complex site and you need to be out all day to manage the works. What BIM 360 Field did was to let the guys be out on the site and have their health and safety checklist, their quality assurance checklist, their drawings and logistics plans and safety briefing notes. The guys could look ahead and see when something’s being erected or cast, and what the next element of work is going to be, and they can prevent work from taking place that may need corrective action later.”
The BIM 360 system had a big effect on how quickly and effectively problems could be dealt with, Taylor says. “When we found issues on site, say reinforcement was missing or missplaced, we’d be able to take a picture, attach drawings and specification and send it to the relevant subcontractor.
Usually, the first thing that happens if you tell someone something’s wrong is that they ask you for a load of information and then you have to walk for 20 minutes to go and find the information and while you’re doing it someone asks you 10 questions about something else. For safety inspections, it cuts the time required by half as you can do the work there and then. And because you’re working more efficiently you can ensure the project’s quality and reduce defects.”
The cloud computing part of the process allows the team to build up a constantly updated picture of site progress, and create a record of the project at every stage in its life. This can have unexpected benefits for a main contractor that wants to claim extra time for an unexpected weather event, as BAM found out when 2ft of snow fell on the site. Taylor says: “Because we were using this system and we were very quickly able to pull the information together, saving many man hours.”
Despite its size and complexity, the project was finished on time, and Bam estimates that the effect of coordination using the BIM on elements such as “BWICS” [builders work in connection with services] was to make it 60% more efficient.
So, how will Taylor use BIM 360 Field next time? The answer is that there will be no great changes, but some fine-tuning: as the software can be reconfigured by the user, BAM will be looking to try different ways to organise the workflow. Also, the team will have more confidence to explore all the possibilities and extend its use further.
As for the doubting subcontractors, Taylor says most bought into the system after they’d familiarised themselves with what it could do. He says: “The feedback was that everyone said they wanted to use the Field BIM more – it had a ripple effect throughout the team because the information was as much help for the subcontractors as for us, and everyone embraced it in the end.”