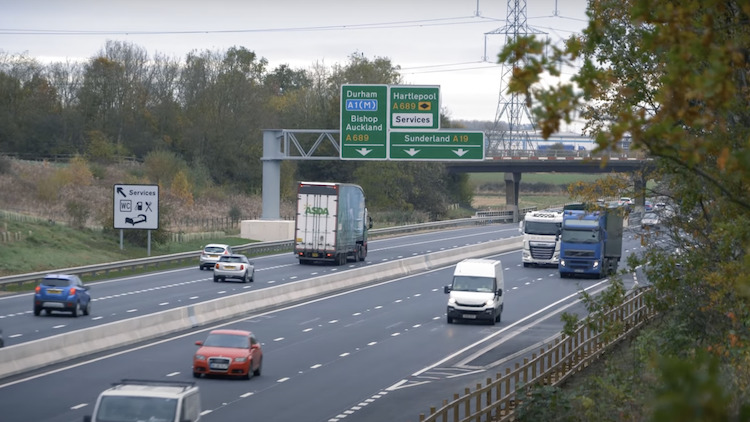
Balfour Beatty Atkins pushed new boundaries in the handover of major highway projects to the maintenance contractor through its work on the A19 Norton to Wynyard improvement scheme in the North East. Its work secured the joint venture the Digital Innovation in Asset Management trophy at the Digital Construction Awards 2023. Denise Chevin spoke with AtkinsRéalis practice manager Brian Russell to learn more.
BIMplus: In just a few sentences before we get into the detail, please explain what Balfour Beatty Atkins did that won you this prestigious award?
Brian Russell: We used a data-rich 3D project information model developed throughout design and construction of a road-widening project on the A19 to hand over a robust and accurate digital twin. The digital twin contained all newly constructed and existing highway elements present, such as pavement, barriers, lighting and drainage – geospatially positioned to their real-world coordinates. There were 4,500-plus newly constructed or modified elements.
The entire digital twin and attached asset data was also viewable on mobile devices. The benefits of this exercise included time saved from drawing/model production and the relevant check, review and approval process. This was estimated to have saved around 1,700 hours of project work with a fee saving of around £67,000.
I can see why the judges were impressed. Let’s go back to the start: when did you get appointed as the contractor on the A19 project?

“We used a data-rich 3D project information model developed throughout design and construction of the A19 to hand over a robust and accurate digital twin.”
It was part of the Routes to Market framework, created by Highways England (now called National Highways) as its procurement model in 2019. Balfour Beatty Atkins had the partnership for several other schemes as well as the A19.
I joined Atkins in February 2020 and started working on site a few days a week with the construction team, in our Atkins team as part of the Balfour Beatty Atkins JV, supporting them on our model-based delivery approach.
Talk us through the project
The A19 is close to Middlesbrough and Balfour Beatty Atkins was contracted to widen the road all along its five miles while it continued to remain a ‘live’ highway.
The A19 was our first project under the Routes to Market schemes and our approach – as it was to be on all our Routes to Market projects – was to look at the traditional handover process, with all its drawings, files, reports, folders etc and look to digitalise it.
We wanted to achieve digital delivery – that way, using our federated digital design process, we were able to provide enough information to the contractor, within our federated models, to allow them to construct the job from those models. By federated, I mean all the information from both us and the contractor, and bringing all the different disciplines together into one model. That allows the team to look at how they’re going to construct certain aspects and elements of the job, while keeping the network open for traffic.
Was that part of the employer’s requirements?
Yes. Part of our contract and our scope is to deliver our assets to ADMM, which is the asset data management manual for National Highways. It’s part of our employer’s requirements to deliver our models in that way, and make sure they have the right asset information that we can then give back to the client, to ensure they have that information on what has been built on their assets.
Does that mean you went about building the model in a different way?
Yes, we made sure our approach to model delivery incorporated those asset requirements. That meant making sure our ADMM information was contained within those models, and making sure any additional information that would benefit our contracting partner was also in the models. That way, the work breakdown structure and all the health and safety risks were embedded within the model, so they could identify areas on site that were possibly going to be challenging.
But as well as giving them as much information as possible to be able to go and construct from those models, we also worked with them to demonstrate how to use the models to their advantage. For example, how they could get that asset information out, how it will enable us at the end to make a smooth digital handover to the road’s maintainer.

What software did you use to create all this?
We use various Autodesk products to do the physical modelling of the different disciplines, and we’ve used NavisWorks to federate our models, bring them together, and set that up in a way that you could then show the asset information within the model on the different elements.
That way we can export the GIS information to the client at the end of the project. So that would be all the individual discipline models – signs, lighting, fencing, barriers – everything was provided in GIS information, as well as the native format, with the asset data embedded within it, so that our maintainer can use that information to populate their asset databases. And that ensures that they’ve got all that ADMM information and they can move that straight into their database.
Take signs, for example. It would give them the sign face requirements, what material was used, what the foundation lengths were for the base for the signs, and so on.
It’s so much easier than with a 2D drawing, because you’d have to start digging through various files and folders. By giving them this data-rich model, and all the GIS information, they’re able to get all of that information on their asset within the model, within the GIS information in the asset reports that we’ve provided.
It sounds pretty groundbreaking – was it?
Not with the tool itself, but rather in the way we used it to support the handover, yes. We worked with an Autodesk tool called MDM – Model Development Manager. It allows us to tag our models in a certain way, and put an attribution on those assets.
Was that difficult?
Yes, there was a learning process because it was new to us. We decided to start tagging information during design, getting it to a point where the detailed design was complete, and then when it went to construction, continuing to populate that information. So as the life cycle of that asset progressed, the information was getting richer and richer. To the point that, come handover, everything’s already produced and ready, so we can just export it and give it to the maintainer.
How is National Highways going to use it? I understand that Balfour Beatty Atkins held workshops with them and the maintenance contractor to detail the benefits of a digital scheme handover
“We linked the asset information to the maintainer’s network, so that we could link where they save all of their information on lighting columns, and we could assign those to the lighting columns within the model.”
Yes, that’s right. We engaged with National Highways and the maintainer, right at the start of this process, and said ‘this is what our approach is going to be’, to try to get some buy-in from them.
And it’s already part of the scope that we’re doing. So we basically agreed to sit down with all parties and run through some workshops to show them how they can get the benefit from it as well, and take them on that journey.
When we started doing that, we instantly got a lot of good buy-in from the maintainer and National Highways, who said ‘this is how we think this model can be used, this is how we think our asset information can be used to support that maintenance’. And once they’d recognised those benefits, it was quite a seamless process to get them on board.
We did some guidance training in terms of the software, how to use it, how to use the model, and how to get the asset information out of it. We linked the asset information to the maintainer’s network, so that we could, for example, link where they save all of their information on lighting columns, and we could assign those to the lighting columns within the model. That way, it could reference all of the schedules that the maintainer had – all of the historical information that they had on the asset.
So it started linking the new construction information with everything previous that the maintainer had as well.
Have you had any feedback on how they’re using it?
It’s been pretty positive. It’s given National Highways and its maintenance contractor all of the information that’s stored within the model. It allows them, when they go and plan the maintenance, to access all of that information on when it was built, what material it is, where it is on the network in terms of its geographical reference. They can locate all of that information much quicker, which allows them to plan their maintenance operations in a much more efficient way.
Is National Highways rolling this out now?
Yes, it is being asked for under the terms of the ADMM requirement. It’s something that we’re delivering as standard as part of our Balfour Beatty Atkins approach. We’re trying to do digital delivery as standard. The world is moving away from traditional drawings. We’re trying to have that model-based delivery, and push that as much as we can, because we understand the benefits, and we’re trying to show our clients the benefits. And that the handover process can be much more streamlined than it would otherwise have been.
Don’t miss out on BIM and digital construction news: sign up to receive the BIMplus newsletter.