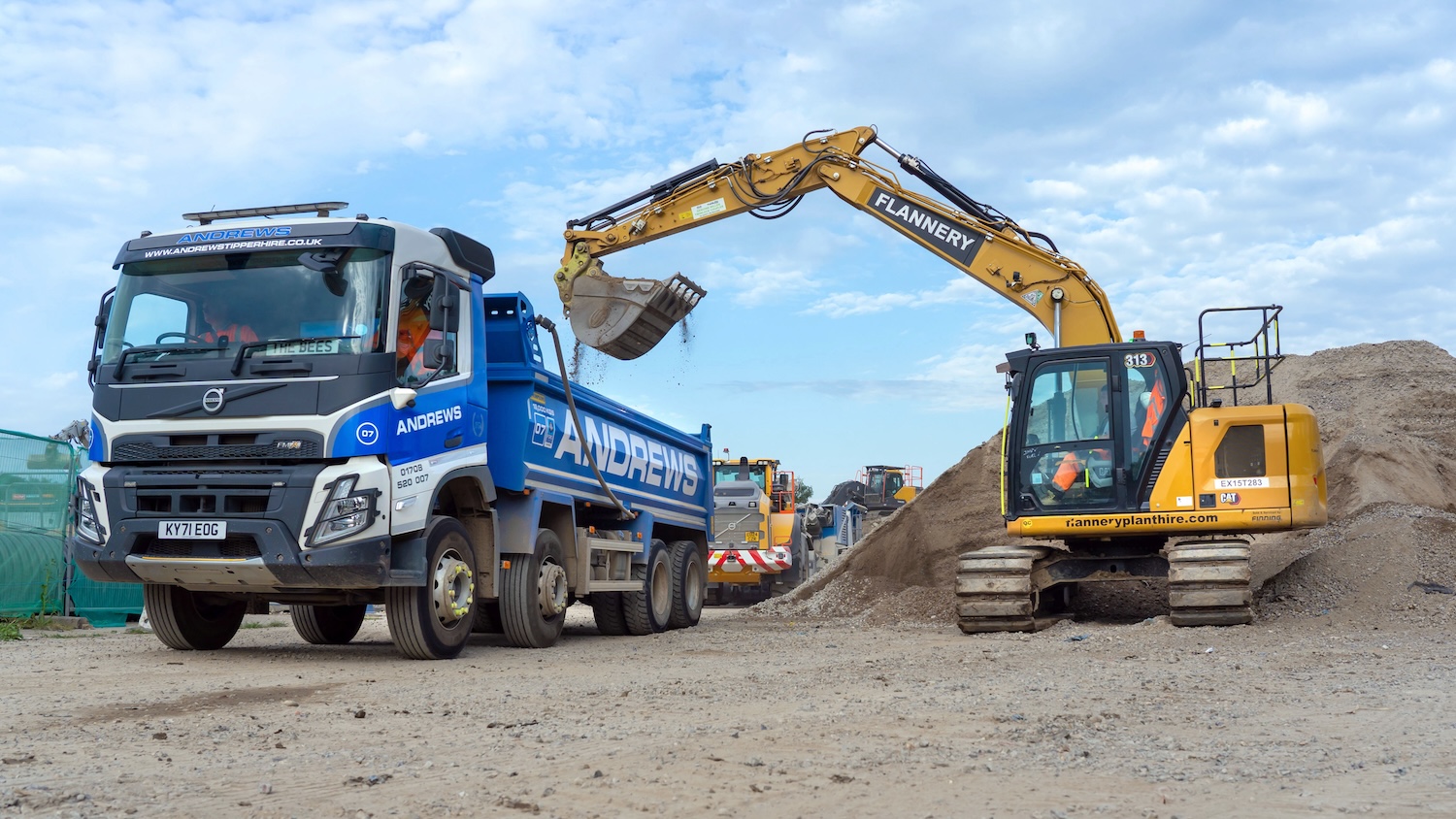
Andrews Tipper Hire is using Podfather logistics software to manage the transport of materials to and from Balfour Beatty’s improvement of M25 Junction 10.
Around 300,000 vehicles travel through Junction 10 of the M25 (near Wisley in Surrey) every day. Balfour Beatty is delivering the three-year improvement scheme of the junction for National Highways.
Digital tickets, including collection and tip locations, as well as the type of material to be moved, are sent to the driver’s tablet and accessed using Podfather. At the start of each shift, drivers are guided through a series of vehicle checks to ensure the road-worthiness of the vehicle. Responses are captured with the app and stored for compliance and health and safety monitoring.
Moving between 150 and 300 loads a day, Andrews’ drivers also use the Podfather app to record evidence of materials transported or loads dropped. Date-, time- and location-stamped photographs, together with signatures from the onsite plant vehicle marshal, are also captured and used to produce daily reports and inform billing.
Visibility and reporting
“Podfather simplifies the management of a complex, fast-moving and ever-changing schedule,” said Tim Page, transport manager at Andrews. “Using Podfather, we have complete visibility of where our drivers are, what materials they are carrying, and where they are going. This information is available to our client’s onsite management team, which means we, and they, can react as situations change and evolve.
“Not only does Podfather improve our onsite performance, it also makes reporting on the project much easier. I can produce the required daily reports in literally 10 minutes, something that would probably have taken me several hours.”
Page continued: “We also use the Podfather data to understand the efficiency of each section of works. We can assess how much material is being used internally versus material that is imported. As information is held digitally, it reduces the amount of time spent transferring data between systems and it is available as needed.”
Michael Ward, logistics coordinator at Balfour Beatty, added: “The use of Podfather was a contributing factor in our selection of Andrews as haulage partner. Digital ticketing, real-time visibility and enhanced reporting all make for a more efficient and more reactive operation.”
Don’t miss out on BIM and digital construction news: sign up to receive the BIMplus newsletter.