- Client: Transport for London
- Lead Contractor: BAM Nuttall
- BIM Tools: Autodesk Revit, Navisworks, BIM 360 Field; Bentley ProjectWise
All things being equal, the £9m refurbishment of Chiswick Bridge would have presented some special problems to the contractor carrying out the work. When it was completed in 1933 it was hailed as a marriage of classical design and cutting-edge engineering. Its five shallow arches and bottle balustrades evoked the Palladian styling of an English country house, whereas the cellular reinforced concrete of the main structure was, at the time, just about the last word in advanced materials.
So the challenge was to repair the parts of the bridge that time had eroded without making any changes at all to their appearance.
But all things were not equal. When the civil engineers from BAM Nuttall sized up the job as part of an “early contractor involvement” (ECI) process agreed with client Transport for London (TfL), it found that the bridge as built did not quite measure up to the drawings that have survived from the original construction process. Everything was a little bit out, and the bridge itself was rather longer than its Wikipedia entry suggested.
On top of this, Chiswick Bridge holds a special place of England’s rowing community, as it forms the finish line for the Oxford–Cambridge boat race. This meant that the whole job had to be fitted into a 52-week schedule, beginning straight after the end of the 2014 race and ending directly before the start of the 2015. What’s more, it is surrounded by rowing clubs whose members form a particularly attentive audience.
On top of that, the bridge is in two London boroughs, Richmond and Hounslow, so that meant two councils and two conservation officers to keep happy, apart from English Heritage and TfL, all of whom could be relied on to examine every square inch of the contractor’s work with a jeweller’s loupe.
The point cloud solution
To help with all the complications, BAM Nuttall decided to use BIM, by adding information to a point cloud representation of the existing structure that was created by a laser scanner.
Jay Moorhouse, the contracts manager for the project, says that this had multiple advantages for the project team: “The point cloud survey we did of the balustrades and the arches revealed that the bridge was actually longer than records showed, and it allowed us to gain a good understanding of the other dimensions, because they were all slightly different to each other and to the drawings.
“So once we had the BIM model we knew where everything was and we could make sure we put all the bottles back in their original position, which was important because the bays were all different by a few millimetres. We also had a full record for each bay pinned to the model so we knew which ones were new and old and we could add all the certificates, so quality insurance was tied into the model.
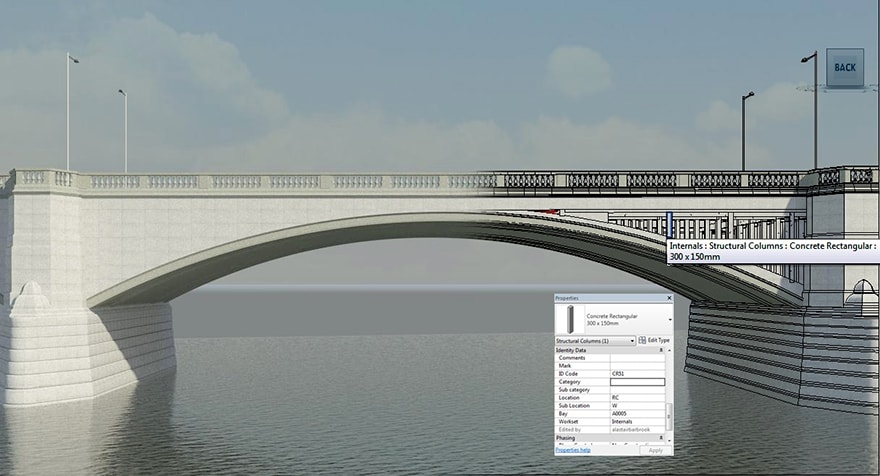
TfL was left with a perfect digital model of the bridge as it actually existed
“And we could use it to make a 3D print-out that we could take and show English Heritage and the council conservation officers, so they could see what it would look like and how it would all fit together.”
Although the “bottles” had been taken from the same seam of Portland Stone, they had all decayed at different rates, mostly over the previous 10 years. Some were as good as new, some had almost completely eroded, and others looked okay but were in fact split by hairline cracks.
The restoration method chosen was to mill out the centre of the original balustrades where possible and replace it with high-grade stainless steel, and here BIM allowed the contractor to order the precise length for each of the steel skeletons that would fill each bottle, and then to allow for their different coefficients of expansion.
As for the new bottles, they were made from the same seam of stone as the original, so although the business of matching them to the original was challenging, the team has the consolation that they could hardly have done it better any other way – and they ordered a lot of spare bottles, just in case.
The second major category of work was repairs to the concrete of the arches, which had areas of spalling that represented a danger to rowers passing beneath. “There were a lot of concrete repairs internally to the structure on the underside of the arches,” says Moorhouse.
“We worked on a barge using two lifts and we got into the bridge internally as well, which was difficult because it was a very confined space with small openings. We did things like get the fire brigade round before we started to show them what we were doing and run through any emergency response procedures.”
Paperless project management
While all this was going on, the bridge had to be kept open at all times to foot passengers, although there were a couple of weekend closures to vehicular traffic to accommodate tasks such as waterproofing the carriageway.
“This was incredibly challenging,” says Moorhouse. “We put some temporary works on the pavement and that produced a walkway on the outside of the balustrades but we had a lot of marshals on duty, and if we had a concrete pour we’d have to stop while pedestrians or cyclists went past. It was tough, but it was important to us that we kept connectivity across the bridge.”
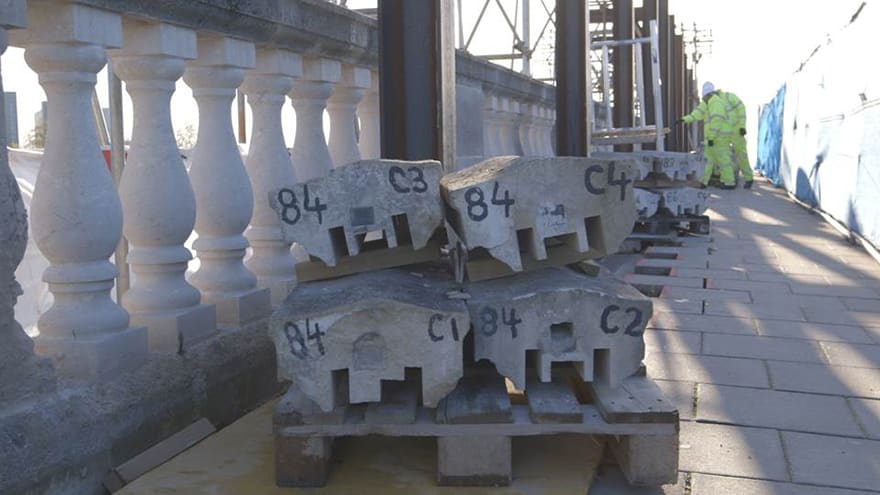
The new bottles were made from the same seam of stone as the original
Although accommodating the public was unavoidably disruptive to the progress of the works, this was another area where BIM helped to smooth the process. The team used Bentley’s ProjectWise to provide the common data environment, and Autodesk’s Revit and Navisworks to create and manipulate the model, but the program that really helped on site was another Autodesk product, BIM 360 Field.
Moorhouse says: “I remember 20 years ago you’d be in the rain standing out there with a sodden drawing trying to get the dimensions from it. Now we have about 10 iPads that contain all the main drawings. And if you’ve done a bit of work, say a concrete repair, you could record it on your iPad check sheet, attach the sheet to the model and take a photo. So if anyone wants to look at a repair they can bring it up on the model and it will bring up the check sheet and photos of the repair before during and after it was carried out. Compare that to the reams of paper we used to keep, the huge boxes of paper we used to give to the client.”
The take-aways
The special advantage of making the work visible to the client and stakeholders on this job was that, as Moorhouse says, “it helped to give them confidence that they were involved and we were thinking about them, and it gave us more confidence that we would get approval”.
Finally, the client, TfL, was left with a perfect digital model of the bridge as it actually existed, including the new lighting system and the status of every individual bottle in the parapet, and this will be used for asset management over the next 80 years between now and the next major refurbishment.
BAM Nuttall’s project team acquired a much better idea of how BIM could be used. Moorhouse says: “We learned a lot about the potential uses of BIM and we got to know the software a bit more, and we’ll certainly use things like 4D programming on future jobs. When you link the programme to the model you can watch the bridge refurbish itself right before your eyes.”
Finally, the citizens of Mortlake and Chiswick, whether travelling on foot, bike or boat got their beloved bridge back, good as new. “A lot of people came up to us at the end of the project and told us it looks really good,” says Moorhouse. “It was quite heart-warming.”
Once we had the BIM model we knew where everything was and we could make sure we put all the bottles back in their original position, which was important because the bays were all different by a few millimetres.– Jay Moorhouse, BAM Nuttall