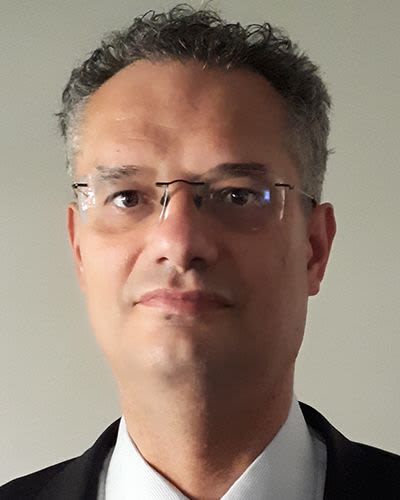
‘All parties to the building process can see the potential IoT brings with retrofitting. Both major and minor retrofits could be performed more effectively with smart connected operations, thus increasing a building’s performance and reducing its environmental impact over its lifecycle.’ Angelo Ciribini
Lavinia Chiara Tagliabue, Angelo Luigi Camillo Ciribini and Marzia Bolpagni discuss research into the possibilities new technology can bring for facilities management and smart contracts.
The IoT (Internet of Things) offers exciting opportunities to the AECO (architecture, engineering, construction and owner-operated) sector. It opens up a multiplicity of options for capturing, integrating and interrogating databases in a way that allows the sector to enhance processes and exponentially develop its business model.
At this stage of IoT, one of the most achievable of these options is the ability to monitor and track in real time the performance of building components over their lifecycle. This tracking can extend throughout the supply chain.
It’s not just AECO companies that can see the possibilities IoT offers to improve building performance. Insurance companies and financial institutions are hopeful it can help them improve building performance and reduce contractual disputes.
All parties to the building process can see the potential IoT brings with retrofitting. Both major and minor retrofits could be performed more effectively with smart connected operations (SCOs), thus increasing a building’s performance and reducing its environmental impact over its lifecycle.
Much work to investigate the possibilities of IoT is being done by the University of Brescia in north Italy. There, the Department of Civil, Environmental, Architectural Engineering and Mathematics and the Department of Information Engineering have produced a sensorised ETICS (External Thermal Insulation Composite System). Together, the departments have produced a prototype which has been tested at the experimental facilities provided by ESEB (Ente Sistema Edilizia Brescia/Building System Institute Brescia), in conjunction with members of the AECO sector.
The sensorised ETICS aims to monitor and control the installation procedures and the operational life of the system itself. As far as the installation stage is concerned, contracts could be arranged and managed in a more effective way, while, within a performance-based contract (eg an energy performance contract), the SCO might make the agreements and payments less controversial.
The research programme has been managed with the support of Weber (Saint-Gobain), starting from the ETICS-focused FMEA (Failure Mode and Effect Analysis). Consequently, a sensorised prototype has been established adopting two different insulation materials, to establish data lakes and assess the prospective performances.
Tied to the research programme, the automation of a traditional contract, related to the installation of an ETICS, has been analysed to detect the main and most meaningful steps and validation processes. Usually, electronic tools are not used to validate the correct installation of the building components. Moreover, there is currently no national or international standard dealing with the installation steps.
For this reason, a handbook edited and published by the Italian external thermal insulation committee (CORTEXA, 2017) has been used, together with some best practices gained through working with Weber (Saint-Gobain).
Usually, building component-related installation contracts do not define requirements in detail: rather, they state that the work should be done “in accordance to the best practices”. However, the “best practice” is an undefined notion and computable values are not provided. To create a smart contract, computable values must be defined so that the actual performance can be measured against the expected contract requirements.
These initial requirements have been included in a python code for the purpose of creating a smart contract. The ultimate goal lies with monitoring the installation process and to link the smart contract to Blockchain technology (which can be used for payments too). Each step should be individually chipped, and once big data sourced by sensors can demonstrate the installation has been successful, then payments could be generated automatically and without human intervention.
Currently, the research group is working on linking data gathered from sensors and other data-capturing technologies (such as photogrammetry) to the smart contract to achieve the stated targets and goals.
This work is one of the first examples of the application of smart contracts in the AECO sector and it aims to serve as a guideline for the sector to refer to and use.
Professor Angelo Luigi Camillo Ciribini conceived the scope of the research; Professor Lavinia Chiara Tagliabue is following and coordinating the development of the prototyping and testing phases; and Dr. Marzia Bolpagni, as part of her PhD thesis, collaborated with the research group to show the automation of a traditional contract
Image: Stepanenko Oksana/Dreamstime.com